Composite material for wind power generator blade and preparation method thereof
A technology for wind turbines and composite materials, applied in the field of fiber-reinforced thermoplastic resin composite materials, can solve the problems of affecting blade strength and low bonding strength, and achieve the effect of ensuring mechanical properties and non-toxic and harmless production environment.
- Summary
- Abstract
- Description
- Claims
- Application Information
AI Technical Summary
Problems solved by technology
Method used
Image
Examples
Embodiment 1
[0032] 70 kg of maleic anhydride grafted polypropylene powder, 0.3 kg of UV absorber, and 0.5 kg of antioxidant were mixed evenly and placed in a high-voltage electrostatic fluidized bed. 40 kg of glass fibers are passed continuously through the fluidized bed. Adjust the electrostatic voltage of the fluidized bed to adjust the amount of glass fiber adsorption resin, so that the weight fraction of maleic anhydride grafted polypropylene is kept at 60, and the glass fiber adsorbed with resin is continuously fed from the oven and a belt with a diameter of 2.5-5.5 The high-temperature die head with a mm circular hole passes through, and after cooling, the continuous strip-shaped composite material is cut into 12.5-25mm long pellets with a pelletizer, and then molded at 230°C to form a test standard sample.
Embodiment 2
[0034] Mix 70 kg of nylon 66 powder, 0.3 kg of ultraviolet absorber, and 0.5 kg of antioxidant, and place them in a high-voltage electrostatic fluidized bed. 45 kg of glass fibers were passed continuously through the fluidized bed. Adjust the electrostatic voltage of the fluidized bed to adjust the amount of glass fiber adsorption resin, so that the weight fraction of nylon 66 is kept at 55. The glass fiber adsorbed with resin passes continuously through the oven and a high-temperature die head with a circular hole with a diameter of 2.5-5.5mm, and then after cooling, the continuous strip-shaped composite material is cut into 12.5-25mm long granular particles with a pelletizer , and then molded into test standard specimens at 270°C.
Embodiment 3
[0036] 70 kg of polypropylene copolymer powder, 0.3 kg of UV absorber, and 0.5 kg of antioxidant were mixed evenly and placed in a high-voltage electrostatic fluidized bed. 40 kg of glass fibers are passed continuously through the fluidized bed. Adjust the electrostatic voltage of the fluidized bed to adjust the amount of glass fiber adsorption resin, so that the weight fraction of polypropylene copolymer is kept at 60. The glass fiber adsorbed with resin passes continuously through the oven and a high-temperature die head with a circular hole with a diameter of 2.5-5.5mm, and then after cooling, the continuous strip-shaped composite material is cut into 12.5-25mm long granular particles with a pelletizer . Then it was molded at 230°C into a test standard bar.
PUM
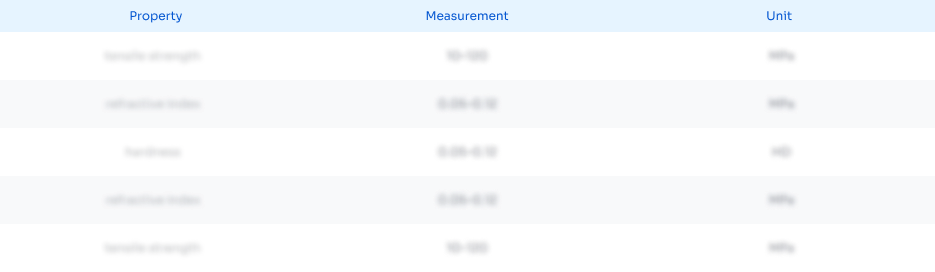
Abstract
Description
Claims
Application Information

- R&D
- Intellectual Property
- Life Sciences
- Materials
- Tech Scout
- Unparalleled Data Quality
- Higher Quality Content
- 60% Fewer Hallucinations
Browse by: Latest US Patents, China's latest patents, Technical Efficacy Thesaurus, Application Domain, Technology Topic, Popular Technical Reports.
© 2025 PatSnap. All rights reserved.Legal|Privacy policy|Modern Slavery Act Transparency Statement|Sitemap|About US| Contact US: help@patsnap.com