Method for preparing nanoscale anionic laminar material continuously
A layered material and anion technology, applied in chemical instruments and methods, inorganic chemistry, non-metallic elements, etc., can solve the problems of non-continuous production, complex processing, high reaction temperature, etc., and achieve shortened nucleation induction period and particle size distribution The effect of narrowing and uniform particle size distribution
- Summary
- Abstract
- Description
- Claims
- Application Information
AI Technical Summary
Problems solved by technology
Method used
Image
Examples
Embodiment 1
[0018] Such as figure 1 , figure 2 As shown, prepare 3.0L of Mg 2+ The concentration is 0.0067mol / L, Al 3+ MgCl with a concentration of 0.0033mol / L 2 ·6H 2 O and AlCl 3 ·6H 2 O Metal Salt Hydration, by Mg 2+ with Al 3+ The molar ratio is 2 to form a soluble metal salt mixture, in which Mg 2+ 0.0201mol, Al 3+ is 0.0099mol; the preparation concentration is 0.1mol / L ammonium carbonate (NH 4 ) 2 CO 3 solution as a precipitant solution, (NH 4 ) 2 CO 3 The amount of substance and the anion Cl in the soluble metal salt mixture - The total molar ratio is 0.5. Add the soluble metal salt mixture into the preheating tank of the spiral channel type rotating bed high gravity reactor 4 to preheat to 20°C, close the valve 3, and open the valve 14. Start up the spiral channel type rotating bed supergravity reactor 4, and after the liquid flow rate in the spiral channel type rotating bed supergravity reactor 4 reaches 50L / h and stabilizes, flow to the spiral channel type rota...
Embodiment 2
[0020] Such as figure 1 , figure 2 As shown, prepare 3.0L of Mg 2+ The concentration is 0.04mol / L, Al 3+ MgCl with a concentration of 0.01mol / L 2 ·6H 2 O and AlCl 3 ·6H 2 O Metal Salt Hydration, by Mg 2+ with Al 3+ The molar ratio is 4 to form a soluble metal salt mixture, in which Mg 2+ 0.12mol, Al 3+ is 0.03mol; the preparation concentration is 5.0mol / L ammonium carbonate (NH 4 ) 2 CO 3 solution as a precipitant solution, (NH 4 ) 2 CO 3 The amount of substance and the anion Cl in the soluble metal salt mixture - The total molar ratio is 3. 0.5% Mg(OH)2 The seed crystal is added to the soluble metal salt mixture, and the soluble metal salt and seed crystal mixture is added to the preheating tank of the spiral channel type rotating bed high-gravity reactor 4. After preheating to 60°C, close the valve 3 and open the valve 14. Start up the spiral channel type rotating bed supergravity reactor 4, and after the liquid flow rate in the spiral channel type rotatin...
Embodiment 3
[0022] Such as figure 1 , figure 2 As shown, prepare 3.0L of Mg 2+ The concentration is 0.075mol / L, Al 3+ Concentration of 0.025mol / L Mg(NO 3 ) 2 ·6H 2 O and Al(NO 3 ) 3 9H 2 O Metal Salt Hydration, by Mg 2 with Al 3+ The molar ratio is 3 to form a soluble metal salt mixture, in which Mg 2+ 0.225mol, Al 3+ 0.075mol; the preparation concentration is 10.0mol / L urea as precipitant solution, the amount of urea substance and the anion NO in the soluble metal salt mixture 3 - The total molar ratio is 5. Add 3.0% MgO seed crystals to the soluble metal salt mixture, add the soluble metal salt and seed crystal mixture to the preheating tank of the spiral channel type rotating bed supergravity reactor 4, preheat to 95°C, and then close Valve 3, open valve 14. Start up the spiral channel type rotating bed supergravity reactor 4, and after the liquid flow rate in the spiral channel type rotating bed supergravity reactor 4 reaches 700L / h and stabilizes, flow to the spiral c...
PUM
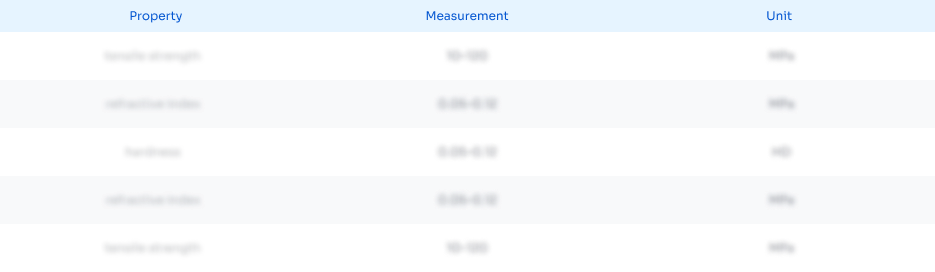
Abstract
Description
Claims
Application Information

- R&D
- Intellectual Property
- Life Sciences
- Materials
- Tech Scout
- Unparalleled Data Quality
- Higher Quality Content
- 60% Fewer Hallucinations
Browse by: Latest US Patents, China's latest patents, Technical Efficacy Thesaurus, Application Domain, Technology Topic, Popular Technical Reports.
© 2025 PatSnap. All rights reserved.Legal|Privacy policy|Modern Slavery Act Transparency Statement|Sitemap|About US| Contact US: help@patsnap.com