Non-carbon residue feather edge brick for refining steel ladle and preparation method thereof
A technology of carbon slag wire brick and refined steel, which is applied in the field of refractory materials, can solve the problem of carbon increase, restrict the smelting process of ultra-low carbon steel, and the problems of unsynchronized service life of refractory lining and low service life, so as to improve anti-stripping Sex and thermal shock stability, improved thermal shock stability, and improved compressive strength
- Summary
- Abstract
- Description
- Claims
- Application Information
AI Technical Summary
Problems solved by technology
Method used
Image
Examples
Embodiment 1
[0028] Put high-alumina corundum particles, fused spinel particles, and fused magnesia particles into the wheel mill and mix for 3 minutes, then add aluminum dihydrogen phosphate solution and mix for 5 minutes; then add high-alumina corundum fine powder, fused magnesia Sand fine powder, chromium trioxide fine powder, high-temperature alumina fine powder and other fine powders were mixed for 10 minutes; then dextrin solution was added and mixed for 3 minutes; after mixing evenly, the materials were discharged, and the materials were mixed for 24 hours at 20°C; bricks were pressed by friction Machine molding, the molding pressure is 150MPa. After baking at 180°C for 24 hours, a carbon-slag-free line brick was obtained. Its apparent porosity is 10±2%, its bulk density is 3.10±0.02g / cm3, its compressive strength is 60±10MPa, and its permanent line change after burning at 1550°C is ±1%. Raw materials used and proportioning (proportioning is mass percent) are as follows:
[0029] ...
Embodiment 2
[0034] Put white corundum particles, fused spinel particles, and fused magnesia particles into the wheel mill and mix for 3 minutes, then add water glass solution and mix for 5 minutes; then add white corundum fine powder, fused magnesia fine powder, three Fine powders such as chromium oxide fine powder and high-temperature alumina fine powder were mixed for 8 minutes; then sodium carboxymethyl cellulose solution was added and mixed for 5 minutes; after mixing evenly, the material was discharged, and the material was dried at 20°C for 18 hours; the molding pressure was 180MPa. After baking at 180°C for 24 hours, the carbon slag-free wire brick can be obtained. The apparent porosity is 8.5±1.5%, the bulk density is 3.12±0.02g / cm3, the compressive strength is 70±10MPa, and the permanent line change after burning at 1550℃ is ±1%. Raw material weight ratio is as follows:
[0035] raw material name
Specification
purity
% by weight / %
White corundum parti...
Embodiment 3
[0041] Put white corundum particles, tabular corundum particles, fused spinel particles, and fused magnesia particles into the wheel mill and mix for 2 minutes, then add sodium tripolyphosphate solution and mix for 8 minutes; then add platy corundum fine powder , fused magnesia fine powder, chromium trioxide fine powder, high-temperature alumina fine powder and other fine powders were mixed for 10 minutes; then polyvinyl alcohol solution was added and mixed for 5 minutes; after mixing evenly, the material was discharged, and the material was mixed for 18 hours at 20°C ; Molding pressure is 200MPa. After baking at 180°C for 24 hours, the carbon slag-free wire brick can be obtained. The apparent porosity is 11±2%, the bulk density is 3.08±0.02g / cm3, the compressive strength is 55±10MPa, and the permanent line change after burning at 1550°C is ±1%. Raw material weight ratio is as follows:
[0042] raw material name
[0043] raw material name
PUM
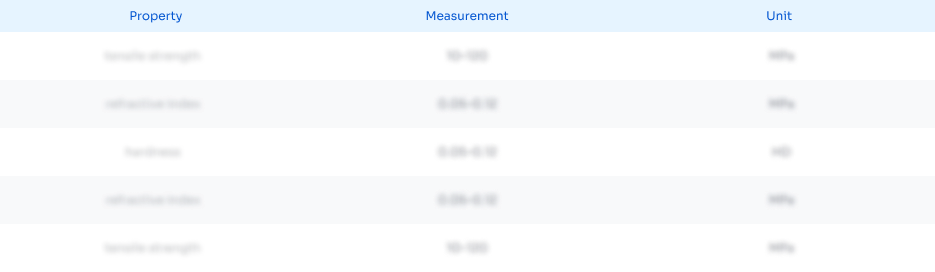
Abstract
Description
Claims
Application Information

- R&D
- Intellectual Property
- Life Sciences
- Materials
- Tech Scout
- Unparalleled Data Quality
- Higher Quality Content
- 60% Fewer Hallucinations
Browse by: Latest US Patents, China's latest patents, Technical Efficacy Thesaurus, Application Domain, Technology Topic, Popular Technical Reports.
© 2025 PatSnap. All rights reserved.Legal|Privacy policy|Modern Slavery Act Transparency Statement|Sitemap|About US| Contact US: help@patsnap.com