Preparation method of hemp fabric construction morph-genetic ceramic composite material
A technology of ceramic composite material and fabric structure, which is applied in the field of preparation of hemp fiber fabric structure remains ceramic composite material, can solve the problem that artificial improvement and reconstruction of biological template structure cannot be achieved, and achieve good sensing and electromagnetic shielding, and expand The effect of the field of application
- Summary
- Abstract
- Description
- Claims
- Application Information
AI Technical Summary
Problems solved by technology
Method used
Examples
Embodiment 1
[0053] Take the plain weave ramie fiber cloth purchased from the market or self-prepared by the existing weaving technology, and naturally impregnate the SiO after hydrolysis of ethyl orthosilicate at room temperature. 2 The sol was dried for 7 days, and after being naturally impregnated with phenolic resin, the hemp fiber fabric was stacked into 10 layers of cloth by lamination, hot-pressed on a molding machine at 150°C and 0.5MPa for 1 hour, and cured after molding to obtain plain weave hemp Fabric / SiO 2 Composite template. The prepared plain weave hemp fiber fabric / SiO 2 The composite template is placed in a vacuum hot-press furnace, under a vacuum protection atmosphere, the vacuum degree is 1×10 -1 Pa, at a heating rate of 20 °C / min, heat preservation at 1600 °C for 2 h, and cool with the furnace to prepare plain weave hemp fiber fabric silicon carbide ceramic composites. The prepared plain weave hemp fiber fabric structural remains ceramics were repeatedly impregnated ...
Embodiment 2
[0055] Take the sisal fiber cloth with twill weave that is purchased from the market or self-prepared by using the existing weaving technology. After impregnating epoxy resin under positive and negative pressure at room temperature, the hemp fiber fabric is stacked into 15 layers of cloth by lamination. 1. Hot pressing under 10MPa pressure for 0.5h, curing after forming, and obtaining a twill weave hemp fiber fabric template. The prepared twill weave hemp fiber fabric template was placed in a vacuum autoclave, under a nitrogen protective atmosphere, the pressure was 0.06MPa, and the heating rate was 3°C / min. Cooling at a rate to prepare a carbon template with a twill weave hemp fiber fabric structure. The carbon template of the prepared twill weave hemp fiber fabric structure remains in a vacuum of 1×10 -1 Pa, 1400 ℃ liquid-phase siliconizing reaction, obtained high-purity silicon carbide ceramics with sisal fiber fabric structure.
Embodiment 3
[0057] Take the linen fiber fabric with knitted structure purchased from the market or self-prepared by the existing weaving technology. After impregnating epoxy resin ultrasonically at room temperature, the linen fiber fabric is stacked into two layers of cloth by lamination. Hot-pressing under pressure for 5 hours, curing after molding, and obtaining the hemp fiber fabric template with knitted structure. The prepared hemp fiber fabric template with knitted structure was placed in a vacuum hot-press furnace, under an argon protective atmosphere, the pressure was 0.03MPa, and the heating rate was 20°C / min, kept at 1800°C for 1h, cooled with the furnace, and prepared A carbon template out of the remains of a hemp fiber fabric with a knitted structure. The carbon template of the prepared knitted hemp fiber fabric remains in a vacuum of 1×10 -1 Pa, 1600 ℃ liquid-phase siliconization reaction, obtained silicon carbide ceramics with knitting structure flax fiber fabric.
PUM
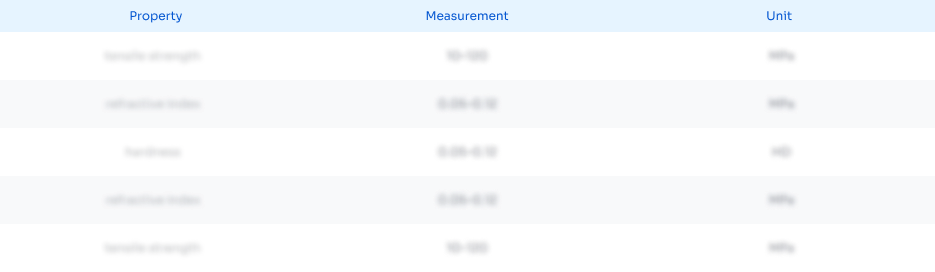
Abstract
Description
Claims
Application Information

- R&D
- Intellectual Property
- Life Sciences
- Materials
- Tech Scout
- Unparalleled Data Quality
- Higher Quality Content
- 60% Fewer Hallucinations
Browse by: Latest US Patents, China's latest patents, Technical Efficacy Thesaurus, Application Domain, Technology Topic, Popular Technical Reports.
© 2025 PatSnap. All rights reserved.Legal|Privacy policy|Modern Slavery Act Transparency Statement|Sitemap|About US| Contact US: help@patsnap.com