Method for processing polysaccharide material with polymer composition
A technology of polysaccharides and compositions, which is applied in the field of processing polysaccharide materials with polymer compositions, to achieve the effect of improving dimensional stability
- Summary
- Abstract
- Description
- Claims
- Application Information
AI Technical Summary
Problems solved by technology
Method used
Image
Examples
Embodiment 1
[0040] 432g of maltodextrin, 192g of citric acid, and 9g of boric acid were dissolved in 1.16kg of water, and the solution was stirred until the solution was clear and transparent. Put 3 fir planks of 100×60×20 (unit: mm) in an autoclave, first pump to a vacuum of 90%, and maintain the vacuum for 30 minutes, then inject the above solution into the autoclave, and wait for the solution to be added After completion, gradually increase the pressure to 18 atmospheres. The pressure was maintained for 5 hours, then the pressure was gradually reduced to normal pressure, and the solution was extracted from the reaction kettle. Reduce the pressure to 80% vacuum for about 20 minutes, then dry the boards at 95°C for 24 hours under normal pressure. After drying, the wood block was treated with high-pressure steam at 180° C. for 10 minutes in an autoclave, and then returned to normal temperature and pressure to obtain a composite polymer product. The comparison data of wood before and aft...
Embodiment 2
[0043] Dissolve 300g of water-soluble starch, 25g of citric acid, 48g of tartaric acid, 48g of maleic acid, 20g of triethanolamine, 5g of zinc bromide, and 2g of ammonium phosphate in 1.16kg of water, adjust the pH value to 6 with 30% ammonia water, and stir solution until the solution is clear and transparent. Put 3 paulownia planks of 100×60×20 (unit: mm) in an autoclave, first pump to a vacuum of 85%, and maintain the vacuum for 30 minutes, then inject the above solution into the autoclave, and wait until the solution is added After completion, gradually increase the pressure to 22 atmospheres. The pressure was maintained for 3 hours, then the pressure was gradually reduced to normal pressure, and the solution was extracted from the reaction kettle. The pressure was reduced to 80% vacuum for about 20 minutes, and then the board was dried at 110° C. for 24 hours under normal pressure. After drying, the wood block was treated with high-pressure steam at 180° C. for 10 minut...
Embodiment 3
[0046] 250g of polyhydroxyacrylic acid, 20g of 4-hydroxythreonine, 227g of glucaric acid, 15g of terephthalic acid, 15g of maleic anhydride, 10g of boric acid, 2.5g of zinc acetate, and 2g of ammonium phosphate were dissolved in 1.23kg of water. Adjust the pH value to 6 with 30% ammonia water, and stir the solution until the solution is clear and transparent. Put 3 bamboo slices of 200×25×5 (unit: mm) in an autoclave, first pump to a vacuum of 90%, and maintain the vacuum for 30 minutes, then inject the above solution into the autoclave, and wait until the solution is added After completion, gradually increase the pressure to 20 atmospheres. The pressure was maintained for 3.5 hours, then the pressure was gradually reduced to normal pressure, and the solution was extracted from the reaction kettle. The pressure was reduced to 80% vacuum for about 20 minutes, and then the board was dried at 110° C. for 24 hours under normal pressure. After drying, balance in a constant temper...
PUM
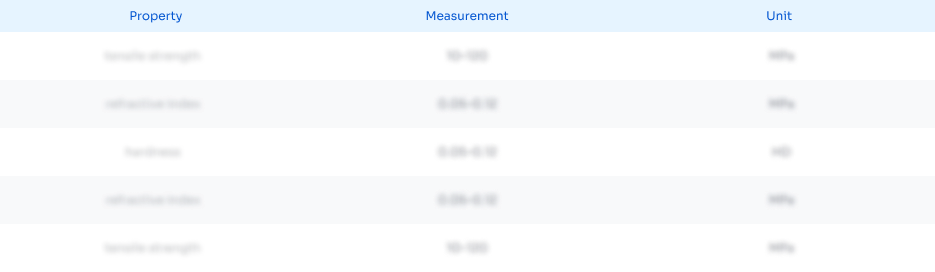
Abstract
Description
Claims
Application Information

- Generate Ideas
- Intellectual Property
- Life Sciences
- Materials
- Tech Scout
- Unparalleled Data Quality
- Higher Quality Content
- 60% Fewer Hallucinations
Browse by: Latest US Patents, China's latest patents, Technical Efficacy Thesaurus, Application Domain, Technology Topic, Popular Technical Reports.
© 2025 PatSnap. All rights reserved.Legal|Privacy policy|Modern Slavery Act Transparency Statement|Sitemap|About US| Contact US: help@patsnap.com