Method for preparing extra-coarse grained carbide alloy
A hard alloy and coarse-grained technology, which is applied in the field of metal materials, can solve the problems of grinding alloys that are not ultra-coarse grains, and achieve the effect of improving toughness and wear resistance and making raw materials easy to obtain
- Summary
- Abstract
- Description
- Claims
- Application Information
AI Technical Summary
Problems solved by technology
Method used
Examples
Embodiment 1
[0016] Example 1: Premix ultra-coarse tungsten carbide powder and cobalt powder with a Fischer particle size greater than 6 μm in the ground state, and after adding a molding agent, press the powder into agglomerates and put them into a degumming furnace with ammonia decomposition gas for pre-sintering; Put the pre-sintered tungsten carbide-cobalt agglomerate together with tungsten carbide powder and cobalt powder into a ball mill for crushing and wet grinding; the prepared mixture containing 6-13% cobalt is added with a molding agent and pressed into a product, and re- After degumming, it is sintered in a pressure sintering furnace at a high temperature, and the temperature is controlled at 1430-1480°C; the sintered product is then heat-treated in a double-chamber high-pressure air-cooled vacuum furnace. The weight ratio of the premixed tungsten carbide powder and cobalt powder is: 91.5 parts of tungsten carbide powder, 8.5 parts of cobalt powder, and 2.5 parts of forming agen...
Embodiment 2
[0017] Example 2: Premix ultra-coarse tungsten carbide powder and cobalt powder with a Fischer particle size greater than 6 μm in the ground state, and after adding the molding agent, press the powder into agglomerates, put it into a degumming furnace with ammonia decomposition gas for pre-sintering, The pre-sintering temperature is 630-820°C, solid-phase diffusion of cobalt and tungsten carbide, strong coating force, part of the residual carbon is conducive to sintering densification, reducing porosity, so that the toughness of cemented carbide is improved and wear-resistant Reinforcement; put the pre-sintered tungsten carbide-cobalt agglomerate together with tungsten carbide powder and cobalt powder into a ball mill for crushing and wet grinding; the prepared mixture containing 6-13% cobalt is added with a molding agent and then pressed into The product is sintered at high temperature in a pressure sintering furnace after re-degumming, and the temperature is controlled at 143...
Embodiment 3
[0018] Example 3: Premix ultra-coarse tungsten carbide powder and cobalt powder with a Fischer particle size greater than 6 μm in the ground state, and after adding a molding agent, press the powder into agglomerates and put them into a degumming furnace with ammonia decomposition gas for pre-sintering; Put the pre-sintered tungsten carbide-cobalt agglomerate together with tungsten carbide powder and cobalt powder into a ball mill for crushing and wet grinding; the prepared mixture containing 6-13% cobalt is added with a molding agent and pressed into a product, and re- After degumming, it is sintered at high temperature in a pressure sintering furnace, and the temperature is controlled at 1430-1480°C; the sintered product is then heat-treated in a double-chamber high-pressure air-cooled vacuum furnace, and the heat treatment temperature of the vacuum furnace is 1320-1430°C. Grindability can be further improved. The weight ratio of the premixed tungsten carbide powder and coba...
PUM
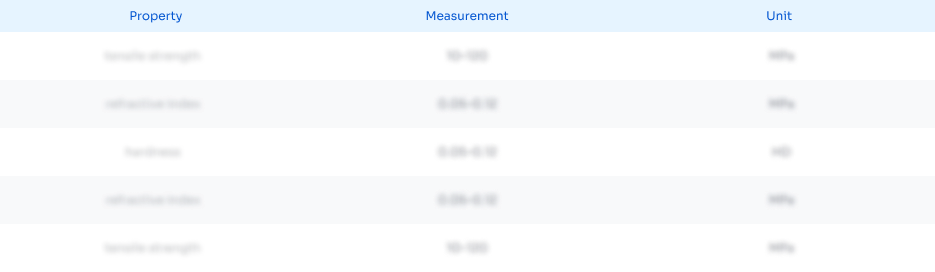
Abstract
Description
Claims
Application Information

- R&D
- Intellectual Property
- Life Sciences
- Materials
- Tech Scout
- Unparalleled Data Quality
- Higher Quality Content
- 60% Fewer Hallucinations
Browse by: Latest US Patents, China's latest patents, Technical Efficacy Thesaurus, Application Domain, Technology Topic, Popular Technical Reports.
© 2025 PatSnap. All rights reserved.Legal|Privacy policy|Modern Slavery Act Transparency Statement|Sitemap|About US| Contact US: help@patsnap.com