Preparation method of silicon rubber foam material
A foam material and silicone rubber technology, which is applied in the field of polymer material processing, can solve the problems of inconsistent degree of cross-linking between the surface layer and the interior of the rubber compound, uneven foam density, poor heat transfer, etc., and achieves low compression permanent deformation and small cells. Uniform, smooth surface effect
- Summary
- Abstract
- Description
- Claims
- Application Information
AI Technical Summary
Problems solved by technology
Method used
Examples
Embodiment 1
[0030] Embodiment 1: 100 grams of dimethyl silicone rubber, 15 grams of fumed silica, and 2 grams of hydroxyl silicone oil were mixed at room temperature for 4 minutes using a double-roller open mill, and 3 grams of azodicarbonamide were added. 1 gram of zinc oxide and 4 grams of triallyl isocyanurate were mixed for 4 minutes, and then compression molded on a flat vulcanizer at room temperature to form a plate. A cylindrical cobalt 60 gamma ray source is used to carry out radiation crosslinking on the silicone rubber compound in air at room temperature, and the radiation dose is 6kGy. The cross-linked silicone rubber is foamed in hot air, the temperature of the hot air is 200° C., and the foaming time is 5 minutes. After the silicone rubber is foamed, the cobalt 60 gamma ray source is used for secondary radiation crosslinking immediately, and the radiation dose is 50kGy.
Embodiment 2
[0031] Example 2: 100 grams of methyl vinyl silicone rubber, 30 grams of fumed silica, and 6 grams of diphenylsilanediol were mixed at room temperature for 7 minutes using an internal mixer, and 8 grams of dinitroso Pentamethylenetetramine, 2 grams of urea, and 2 grams of trimethylolpropane trimethacrylate were kneaded for 5 minutes, and then compression molded on a flat vulcanizing machine at room temperature to form a plate. Using a JJ-2 electrostatic accelerator, the silicone rubber compound is irradiated and cross-linked in air at room temperature, and the irradiation dose is 10kGy. The crosslinked film was foamed in hot air, the temperature of the hot air was 190° C., and the foaming time was 8 minutes. After the silicone rubber is foamed, the JJ-2 type electrostatic accelerator is used for secondary radiation crosslinking immediately, and the radiation dose is 30kGy.
PUM
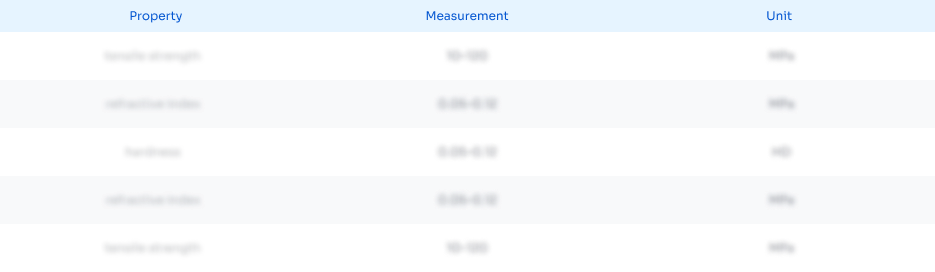
Abstract
Description
Claims
Application Information

- Generate Ideas
- Intellectual Property
- Life Sciences
- Materials
- Tech Scout
- Unparalleled Data Quality
- Higher Quality Content
- 60% Fewer Hallucinations
Browse by: Latest US Patents, China's latest patents, Technical Efficacy Thesaurus, Application Domain, Technology Topic, Popular Technical Reports.
© 2025 PatSnap. All rights reserved.Legal|Privacy policy|Modern Slavery Act Transparency Statement|Sitemap|About US| Contact US: help@patsnap.com