Inorganic porous ceramic material and preparation method thereof
A ceramic material and inorganic porous technology, which is applied in the field of inorganic porous ceramic materials and their preparation, can solve the problems of non-porous inorganic ceramic materials, and achieve the effect of low cost and simple process
- Summary
- Abstract
- Description
- Claims
- Application Information
AI Technical Summary
Problems solved by technology
Method used
Image
Examples
Embodiment 1
[0030] According to the material dry mixing and sintering process, Mg is used as the magnesium source, Fe(OH) 3 is the iron source, H 3 BO 3 As the boron source, the preparation steps of the inorganic porous ceramic material are as follows. The first step ingredients: Mg, Fe(OH) 3 、H 3 BO 3 All are analytical reagents, weighing 19.56g Mg, 28.51g Fe(OH) 3 , 16.54gH 3 BO 3 , wherein the molar ratio Mg:Fe:B is 1:0.33:0.33. The second step of mixing: the weighed Mg, Fe(OH) 3 and H 3 BO 3 Add a high-speed mixer (18000 rpm) and mix for 5 minutes to make it fully uniform. The third step of molding: Pour the mixture into a steel mold, use a 500-ton press, hold the pressure for 18 minutes, shape it, and take it out. The fourth step is reaction sintering: put the formed material into the reaction tank without sealing. Put the reaction tank into a heating furnace, keep it warm at 650°C for 20 minutes, cool naturally, open the tank and take out the product, the appearance is ...
Embodiment 2
[0032] According to the material ball milling and sintering process, Mg(OH) 2 , Mg is magnesium source, ferric nitrate is iron source, B 2 o 3 As the boron source, the preparation steps of the inorganic porous ceramic material are as follows. The first step ingredients: Mg(OH) 2 , Mg, Fe(NO3) 3 , B 2 o3 All are analytical reagents, weigh 15.31g Mg(OH) 2 , 38.31g Mg, 63.46g Fe(NO3) 3 , 36.55g B 2 o 3 , wherein the molar ratio Mg:Fe:B is 1:0.14:0.57. The second step of ball milling: Pour the prepared raw materials into the steel ball mill tank, adjust the parameters of the ball mill, rotate at 500 rpm, revolution at 250 rpm, and mill for 16 hours. The third step of molding: pour the ball mill material into a steel mold, and use a 500-ton press to hold the pressure for 18 minutes. The fourth step is reaction sintering: put the formed material into the reaction tank without sealing. Put the reaction tank into a heating furnace, keep it warm at 700°C for 15 minutes, cool...
Embodiment 3
[0034] According to the liquid phase composite and sintering process, MgCO 3 , Mg is magnesium source, FeCl 3 , iron boron (FeB 1.3 ), B 2 o 3 The preparation process of MgFeBO inorganic porous ceramic material is introduced for iron source and boron source. The first step ingredients: MgCO 3 , Mg, FeCl 3 , ferroboron powder, B 2 o 3 All are analytical reagents, weigh 8.06g MgCO 3 , 20.93g Mg, 15.51g FeCl 3 , 50g ferroboron powder, 20.01gB 2 o 3 , wherein the molar ratio Mg:Fe:B is 1:0.85:1.58. The second step of reaction coating: pour the weighed material into a 1000ml beaker, add 40g of concentrated ammonia water with a mass fraction of 25-28%, and stir for 5 hours. The third step is water removal and pulverization process: the mixed solution is suction filtered and washed. The filter cake was dried in a vacuum oven at 80°C for 6 hours, then taken out and pulverized. The fourth step of molding: Pour the mixture into a steel mold, and use a 500-ton press to keep...
PUM
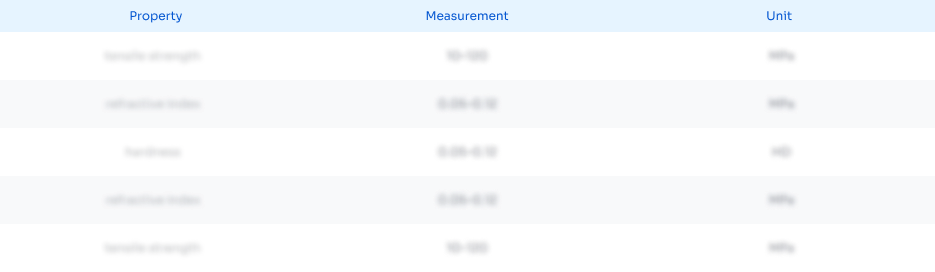
Abstract
Description
Claims
Application Information

- R&D
- Intellectual Property
- Life Sciences
- Materials
- Tech Scout
- Unparalleled Data Quality
- Higher Quality Content
- 60% Fewer Hallucinations
Browse by: Latest US Patents, China's latest patents, Technical Efficacy Thesaurus, Application Domain, Technology Topic, Popular Technical Reports.
© 2025 PatSnap. All rights reserved.Legal|Privacy policy|Modern Slavery Act Transparency Statement|Sitemap|About US| Contact US: help@patsnap.com