Melting method of sintered samarium cobalt base rare earth permanent magnet material master alloy
A rare earth permanent magnet and master alloy technology, applied in the direction of magnetic materials, magnetic objects, electrical components, etc., can solve the problems of slow cooling of alloy ingots, difficult composition control, large difference in melting point, etc., to reduce the thickness of ingots, avoid Decomposition of phases, effect of high uniformity of magnetic properties
- Summary
- Abstract
- Description
- Claims
- Application Information
AI Technical Summary
Problems solved by technology
Method used
Examples
Embodiment 1
[0017] 1. Raw material of 2:17 SmCo alloy
[0018] Sm, Co, Fe, Cu, Zr
[0019] 2. Chemical composition of ingredients
[0020] Sm (wt%)
Co (wt%)
Fe(wt%)
Cu(wt%)
Zr (wt%)
25
50
16
7
2
[0021] 3. Preparation process of 2:17 type SmCo master alloy
[0022] ①Pack Fe, Co, Zr, Cu in the crucible in the vacuum quick-setting melting furnace, and Sm in the feeder in the vacuum quick-setting melting furnace;
[0023] ②Vacuumize, the vacuum degree in the furnace reaches 1.33×10 -2 Pa;
[0024] ③Pass high-purity argon gas to make the pressure in the vacuum quick-setting melting furnace 50kPa, and melt it with electricity;
[0025] ④ After all the raw materials in the crucible are melted, add metal Sm, and use electromagnetic force to automatically stir the liquid for refining. The temperature of the alloy liquid is about 1320, and keep it warm for 4 minutes;
[0026] ⑤ Cast the uniformly smelted alloy liquid onto a rotatin...
Embodiment 2
[0030] 1. Raw material of 2:17 SmCo alloy
[0031] Sm, Co, Fe, Cu, Zr
[0032] 2. Chemical composition of ingredients
[0033] Sm (wt%)
Co (wt%)
Fe(wt%)
Cu(wt%)
Zr (wt%)
25
50
16
7
2
[0034] 3. Preparation process of 2:17 type SmCo master alloy
[0035] ①Pack Fe, Co, Zr, Cu in the crucible in the vacuum quick-setting melting furnace, and Sm in the feeder in the vacuum quick-setting melting furnace;
[0036] ②Vacuumize, the vacuum degree in the furnace reaches 1.33×10 -2 Pa;
[0037] ③Pass high-purity argon gas to make the pressure in the vacuum quick-setting melting furnace 70kPa, and melt it with electricity;
[0038] ④ After all the raw materials in the crucible are melted, add metal Sm, and use electromagnetic force to automatically stir the liquid for refining. The temperature of the alloy liquid is about 1300, and it is kept for 10 minutes;
[0039] ⑤ Cast the uniformly smelted alloy liquid onto a rotating...
Embodiment 3
[0043] 1. Raw material of 2:17 SmCo alloy
[0044] Sm, Er, Co, Fe, Cu, Zr
[0045] 2. Chemical composition of ingredients
[0046] Sm (wt%)
Er (wt%)
Co (wt%)
Fe(wt%)
Cu(wt%)
Zr (wt%)
16
9
49.6
15
8
2.4
[0047] 3. Preparation process of 2:17 type SmCo master alloy
[0048] ① Install Er, Fe, Co, Zr, Cu in the crucible in the vacuum quick-setting melting furnace, and Sm in the feeder in the vacuum quick-setting melting furnace;
[0049] ②Vacuumize, and the vacuum degree in the vacuum quick-setting melting furnace reaches 1.33×10 -2 Pa;
[0050] ③Pass high-purity argon gas to make the pressure in the vacuum quick-setting melting furnace 70kPa, and melt it with electricity;
[0051] ④ After all the raw materials in the crucible are melted, metal Sm is added, and the liquid is automatically stirred by electromagnetic force for refining. The temperature of the alloy liquid is 1400°C, and it is kept for 10 minu...
PUM
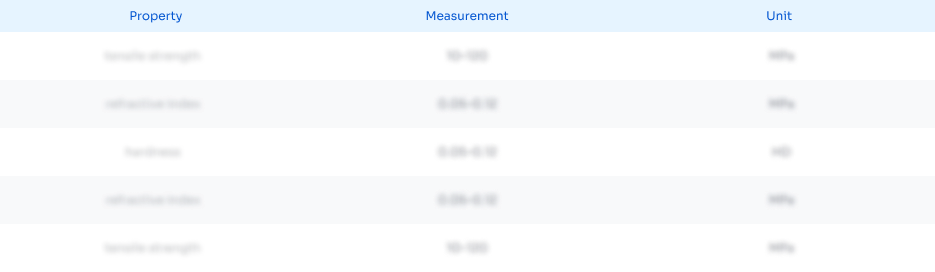
Abstract
Description
Claims
Application Information

- R&D
- Intellectual Property
- Life Sciences
- Materials
- Tech Scout
- Unparalleled Data Quality
- Higher Quality Content
- 60% Fewer Hallucinations
Browse by: Latest US Patents, China's latest patents, Technical Efficacy Thesaurus, Application Domain, Technology Topic, Popular Technical Reports.
© 2025 PatSnap. All rights reserved.Legal|Privacy policy|Modern Slavery Act Transparency Statement|Sitemap|About US| Contact US: help@patsnap.com