Leaching method of vanadium in vanadium-containing stone coal
A vanadium stone and leaching technology, which is applied in the field of vanadium extraction, can solve the problems of environmental pollution, vanadium leaching rate decline, loss, etc.
- Summary
- Abstract
- Description
- Claims
- Application Information
AI Technical Summary
Problems solved by technology
Method used
Image
Examples
Embodiment 1
[0018] ① 100g vanadium-containing stone coal containing 1.25% vanadium is crushed, ball-milled to 80 mesh, and then added to the reaction kettle, 12g 98% sulfuric acid and 2.5g fluorite are added, and water is added to control the liquid-solid weight ratio to 1:1, and react at 90°C for 10 hours Then, liquid-solid separation was performed to obtain 100 g of leachate.
[0019] ②After adjusting the pH of the leaching solution to 2.5 with lime milk, at room temperature, extract the leaching solution with 100g 10% P204 and 5% TBP extractant diluted with kerosene at 7 levels, and the raffinate is returned to the reactor with 7 level sulfuric acid with a concentration of 3N The organic phase is loaded by back extraction to obtain a back extraction solution rich in vanadium ions.
[0020] ③After adding 0.75g sodium chlorate to the stripping solution, adding 12% ammonia water to adjust the pH to 2.2, filtering and washing the precipitate, calcining the precipitate in an electric calciner at...
Embodiment 2
[0023] ① 100g vanadium-containing stone coal containing 1.18% vanadium is crushed, ball-milled to 80 mesh, and then added to the reactor, 20g 98% sulfuric acid, 2.5g fluorite and 0.2g sodium chlorate are added, and water is added to control the liquid-solid weight ratio to 1:1 After reacting at 90°C for 2h, add 1g of fluorite, and after leaching at 90°C for 10h, liquid-solid separation to obtain 100g of leaching solution.
[0024] ②After adjusting the pH of the leaching solution to 2.5 with lime milk, at room temperature, the leaching solution is extracted with 100g 10% P204 and 5% TBP extractant diluted with kerosene at 7 levels, and the raffinate is returned to the reactor with 2N sulfuric acid 7 The organic phase is loaded by stage back extraction to obtain a back extraction liquid rich in vanadium ions.
[0025] ③After adding 0.65g sodium chlorate to the stripping solution, adding 12% ammonia water to adjust the pH to 2.2, filtering and washing the precipitate, calcining the pr...
Embodiment 3
[0028] ① 100g vanadium-containing stone coal containing 0.96% vanadium is crushed, ball-milled to 80 mesh, and then added to the reaction kettle, 25g 98% sulfuric acid, 4.0g fluorite and 0.3g sodium chlorate are added, and water is added to control the liquid-solid weight ratio to 1:1 After reacting at 90°C for 2h, add 2g of fluorite. After reacting for 2h, add the remaining 2g of fluorite. After leaching at 90°C for 10h, liquid-solid separation yields 100g of leachate.
[0029] ②After adjusting the pH of the extract with lime milk to 2.5, at room temperature, extract the extract with 100g of 10% P204 and 5% TBP extractant diluted with kerosene at 7 levels. The raffinate is returned to the reaction kettle with 7 levels of 2N sulfuric acid. The organic phase is loaded by back extraction to obtain a back extraction solution rich in vanadium ions.
[0030] ③After adding 0.60g of sodium chlorate to the stripping solution, adding 12% ammonia water to adjust the pH to 2.2, filtering and ...
PUM
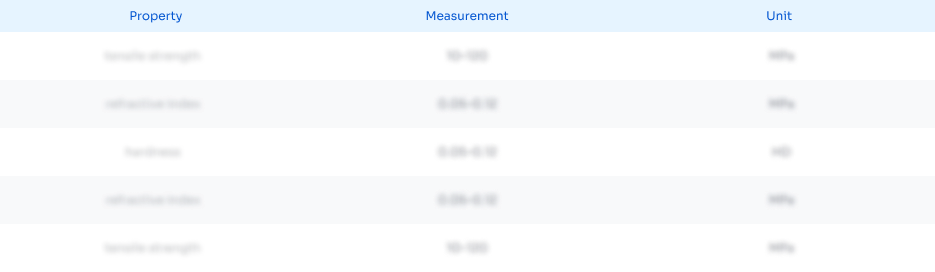
Abstract
Description
Claims
Application Information

- R&D
- Intellectual Property
- Life Sciences
- Materials
- Tech Scout
- Unparalleled Data Quality
- Higher Quality Content
- 60% Fewer Hallucinations
Browse by: Latest US Patents, China's latest patents, Technical Efficacy Thesaurus, Application Domain, Technology Topic, Popular Technical Reports.
© 2025 PatSnap. All rights reserved.Legal|Privacy policy|Modern Slavery Act Transparency Statement|Sitemap|About US| Contact US: help@patsnap.com