Composite pre-heater
A preheater and separator technology, applied in the directions of preheating cost, lighting and heating equipment, furnaces, etc., can solve the problems of low heat exchange efficiency, low preheating efficiency, large heat dissipation loss, etc., and achieve high heat exchange efficiency, The effect of long residence time and less heat loss
- Summary
- Abstract
- Description
- Claims
- Application Information
AI Technical Summary
Problems solved by technology
Method used
Image
Examples
Embodiment 1
[0027] Example 1. Preheating cement raw meal
[0028] Manufacture of composite preheater: use ordinary steel plate to roll and weld the partial cone chamber 1, spray chamber 2, separator 4, spray chamber 2 and separator 4 connecting pipe, separator 4 discharge pipe. The partial cone chamber 1 is tapered on one side, and the upper part of the other side is cylindrical and the lower part is tapered. The height value is h 1 / h=0.5, there is an opening at the upper and lower ends, the inlet air speed is 8m / s, the outlet air speed is 9m / s, the cross-sectional wind speed is 4m / s; the eccentricity e is e / R 1 = 1.5, h 1 / h=0.5, h 2 / h=0.5, h / R 1 =3; The spray chamber 2 is a cylindrical hollow structure, the shell is made of steel plate welding, the inlet is frustum-shaped, the outlet is inverted frustum-shaped, the inlet and outlet air speed is 9m / s, the section wind speed is 6m / s, and the height value is h 2 / h=0.5. O 1 It is the center of the welding port of the partial cone chamber 1 a...
Embodiment 2
[0030] Example 2. Drying desulfurized gypsum
[0031] Manufacture of composite preheater: use ordinary steel plate to roll and weld the partial cone chamber 1, spray chamber 2, separator 4, spray chamber 2 and separator 4 connecting pipe, separator 4 discharge pipe. The partial cone chamber 1 is tapered on one side, and the upper part of the other side is cylindrical and the lower part is tapered. The height value is h 1 / h=0.2, there is an opening at the upper and lower ends, the inlet air speed is 10m / s, the outlet air speed is 12m / s, the cross-sectional wind speed is 6m / s; the eccentricity e is e / R 1 = 2, h 1 / h=0.2, h 2 / h=0.6, h / R 1 =4; The spray chamber 2 is a cylindrical hollow structure, the shell is made of steel plate welding, the inlet is frustum-shaped, the outlet is inverted frustum-shaped, the inlet and outlet air speed is 11m / s, the cross-section wind speed is 8m / s, and the height value is h 2 / h=0.6. O 1 It is the center of the welding port of the partial cone cham...
PUM
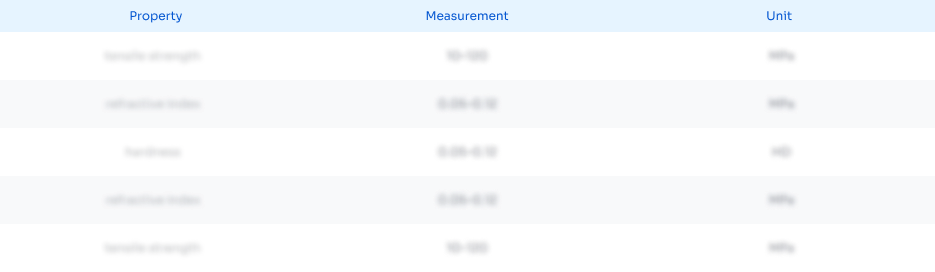
Abstract
Description
Claims
Application Information

- R&D
- Intellectual Property
- Life Sciences
- Materials
- Tech Scout
- Unparalleled Data Quality
- Higher Quality Content
- 60% Fewer Hallucinations
Browse by: Latest US Patents, China's latest patents, Technical Efficacy Thesaurus, Application Domain, Technology Topic, Popular Technical Reports.
© 2025 PatSnap. All rights reserved.Legal|Privacy policy|Modern Slavery Act Transparency Statement|Sitemap|About US| Contact US: help@patsnap.com