Method for extracting high purity alumina and silica gel from coal gangue
A coal gangue and alumina technology, applied in the direction of silica, silica, alumina/aluminum hydroxide, etc., can solve the problems of destroying the natural landscape of mining areas and occupying land resources, so as to reduce production costs, simplify production processes, The effect of high extraction rate
- Summary
- Abstract
- Description
- Claims
- Application Information
AI Technical Summary
Problems solved by technology
Method used
Image
Examples
Embodiment 1
[0051] 1. Take coal gangue and Na 2 CO 3 Mix according to the mass ratio of 1:1.2, pulverize and grind to 150 meshes, and roast at a temperature of 700°C for 60 minutes to obtain a roasted product. During calcination, the calcination equipment is connected to the gas output pipe and connected to the carbon separation tank, and the exhaust gas is directly used in the carbon separation process.
[0052] 2. Add water to the roasted product obtained in step 1, so that the solid-to-liquid ratio of the roasted product and water is 1:5, leach for 30 minutes at a temperature of 80° C., and then filter to obtain filtrate and filter residue.
[0053] 3. After concentrating the filtrate obtained in step 2 to 20% of the volume of the original solution, pass CO 2 Carry out carbonation. During the process of carbonization, keep the solution temperature at 60°C, filter the carbon after the pH value reaches 6, and the filter residue is H 2 SiO 3 and Al(OH) 3 mixture, the filtrate is Na ...
Embodiment 2
[0061] 1, with the obtained filter residue of step 3 in embodiment 1 and the Na that reclaims 2 CO 3 Mix according to the ratio of 1:0.8, grind to 200 mesh, stir evenly, and roast at 800°C for 40 minutes to obtain a roasted product. During calcination, the calcination equipment is connected to the gas output pipe and connected to the carbon separation tank, which is directly used in the carbon separation process.
[0062] 2. The roasted product obtained in step 1 is added with a concentration of 5% sodium hydroxide solution (obtained by dissolving and diluting sodium hydroxide with distilled water obtained in step 4 of Example 1), and the solid-liquid ratio is 1: 10, and the temperature is 50°C Under the conditions, leaching for 90 minutes and then filtering to obtain the filtrate and filter residue.
[0063] 3. Concentrate the filtrate obtained in step 2 to 15% of the original volume, and feed CO into the concentrated filtrate 2 , after the pH value reaches 8, filter, and ...
Embodiment 3
[0071] 1, with coal gangue, step 2 gained filter residue in embodiment 2 and the Na reclaimed in embodiment 2 2 CO 3 , followed by mixing, pulverizing, and grinding to 200 mesh in the ratio of 2:1:2, and roasting at a temperature of 600° C. for 70 minutes to obtain a roasted product. When roasting, the calcination equipment is connected to the gas output pipe and connected to the carbon separation tank, which is directly used in the carbon separation process.
[0072] 2. The roasted product obtained in step 1 is added with a concentration of 15% sodium hydroxide solution (obtained by dissolving and diluting sodium hydroxide with distilled water obtained in step 4 of embodiment 2), and the solid-to-liquid ratio is 1: 15, and the temperature is 60° C. Under the condition of leaching for 1 hour and then filtering, the filtrate and filter residue were obtained.
[0073] 3. Concentrate the filtrate obtained in step 2 to 15% of the original volume, and feed CO into the concentrate...
PUM
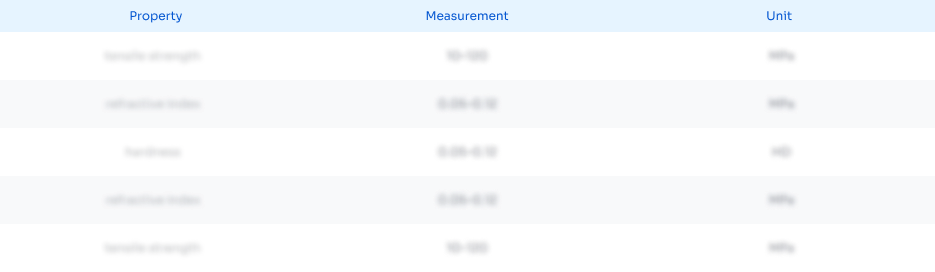
Abstract
Description
Claims
Application Information

- R&D Engineer
- R&D Manager
- IP Professional
- Industry Leading Data Capabilities
- Powerful AI technology
- Patent DNA Extraction
Browse by: Latest US Patents, China's latest patents, Technical Efficacy Thesaurus, Application Domain, Technology Topic, Popular Technical Reports.
© 2024 PatSnap. All rights reserved.Legal|Privacy policy|Modern Slavery Act Transparency Statement|Sitemap|About US| Contact US: help@patsnap.com