Multiphase ceramic hybrid composite reinforced metal matrix composite material and preparation process thereof
A composite material and composite reinforcement technology, used in heat exchange equipment, stators, transmissions, etc., can solve the problems of poor particle uniformity, insufficient reinforcement effect of a single reinforcement phase, and low performance such as modulus, and achieve clean surface and market application. The effect of great potential and simple preparation process
- Summary
- Abstract
- Description
- Claims
- Application Information
AI Technical Summary
Problems solved by technology
Method used
Examples
Embodiment 1
[0026] Multiphase ceramic composite hybrid reinforced metal matrix composites are specifically (TiC+TiB 2 +SiC) / ZL108 aluminum matrix composite.
[0027] ZL108 cast aluminum alloy is selected as the base, and the base is melted in the furnace by the common aluminum alloy melting method. After adding CH-T type sodium-free covering agent on the surface of the melt, the temperature is raised to 660-900°C, argon is passed through, and the preheated Al-Ti master alloy and KBF are added. 4 reaction salt and B 4 C prefabricated blocks, the amount added is based on the generation of enhanced phase TiC, TiB 2 The mass percentages of the SiC particles are controlled at 4% and 6%, respectively, and stirred at a speed of 500-2000r / min for 10-20min; The volume percentage of SiC particles is 5%, and the reinforcement phase TiC, TiB 2 , The mass ratio of SiC is 1:1.5:1. Start the stirring system and stir at a speed of 1200r / min for 20 to 30 minutes. After the particles are evenly distri...
Embodiment 2
[0029] Multiphase ceramic composite hybrid reinforced metal matrix composites are specifically (TiC+TiB 2 +SiC) / 2024 aluminum matrix composite.
[0030] 2024 is selected as the matrix, and the matrix is melted by the ordinary aluminum alloy melting method in the melting furnace. After the matrix is melted, the melt is finely modified, slag-removed, and refined. After adding CH-T type sodium-free covering agent on the surface of the melt, the temperature is raised to 660~900°C, argon is passed through, and the preheated Al-Ti master alloy and NaBF are added. 4 Reactive salt and Al-Ti-C prefabricated blocks, the amount added is based on the formation of reinforcement phase TiC, TiB 2 The mass percentages of the SiC particles are controlled at 8% and 10%, respectively, and stirred at a speed of 500-2000r / min for 10-20min; after the reaction is completed, the reaction salt slag is removed, and the stirring and compounding process of the reinforced phase SiC particles is carri...
Embodiment 3
[0032] Multiphase ceramic composite hybrid reinforced metal matrix composites are specifically (TiC+TiB 2 +SiC) / AZ31 magnesium matrix composite.
[0033] AZ31 is selected as the matrix, and the matrix is melted by the ordinary magnesium alloy melting method in the smelting furnace. After the matrix is melted, the melt is refined, slag-blasted, and refined. After adding a covering agent on the surface of the melt, the temperature is raised to 660-900°C, argon is passed through, and the preheated Mg-Ti master alloy and KBF are added. 4 reaction salt and B 4 C prefabricated blocks, the amount added is based on the product TiC, TiB 2 The mass percentages of the SiC particles are controlled at 10% and 20%, respectively, and stirred at a speed of 500-2000r / min for 10-20min; after the reaction is completed and the reaction salt slag is removed, the stirring and compounding process of the reinforced phase SiC particles is carried out in a vacuum furnace, and the control The vol...
PUM
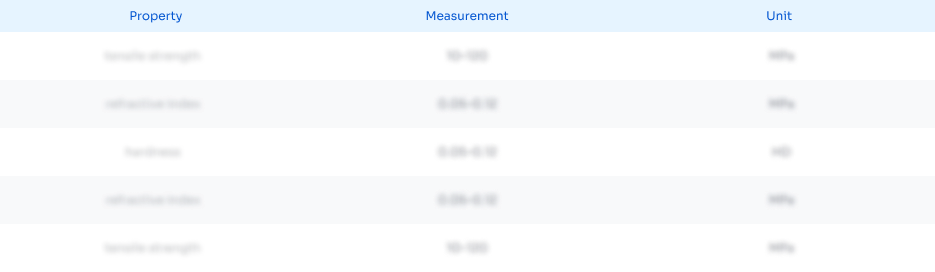
Abstract
Description
Claims
Application Information

- Generate Ideas
- Intellectual Property
- Life Sciences
- Materials
- Tech Scout
- Unparalleled Data Quality
- Higher Quality Content
- 60% Fewer Hallucinations
Browse by: Latest US Patents, China's latest patents, Technical Efficacy Thesaurus, Application Domain, Technology Topic, Popular Technical Reports.
© 2025 PatSnap. All rights reserved.Legal|Privacy policy|Modern Slavery Act Transparency Statement|Sitemap|About US| Contact US: help@patsnap.com