Epoxy resin curing agent, method for preparing same and application thereof
An epoxy resin curing and epoxy resin technology, which is applied in the field of epoxy resin curing agent and its preparation, can solve the problems of poor weather resistance, easy pulverization, brittleness, fatigue resistance, heat resistance, and poor impact toughness. , to achieve the effect of improving adhesion and flexibility, good low-temperature curing performance, and simple preparation process
- Summary
- Abstract
- Description
- Claims
- Application Information
AI Technical Summary
Problems solved by technology
Method used
Image
Examples
Embodiment 1
[0046] Take 1.0 mole of γ-aminopropylmethyldimethoxysilane and dilute it with 1.0 mole of ethanol to obtain an ethanol solution of alkoxysilane;
[0047] At 0°C, add 1.0 mole of water dropwise to the ethanol solution of alkoxysilane, stir for 2 hours, keep the temperature for 16 hours, remove the solvent, and obtain oligosiloxane;
[0048] At 45°C, add 10.0g of cardanol dropwise to 50.0g of oligosiloxane, and stir at a constant temperature for 16 hours; then add 3.0g of hydroxyethylethylenediamine dropwise, and stir at a constant temperature for 10 hours to obtain a new epoxy resin Resin curing agent.
[0049] Mix 30.0g of epoxy resin with 15.0g of titanium dioxide, 5.0g of talc, and 8.0g of barium sulfate; then add 14.0g of oligosilicon epoxy resin curing agent and mix evenly to obtain coating 1, which is evenly coated on the substrate. Under room temperature, after standing for seven days, the performance test of the paint film was carried out.
Embodiment 2
[0051] Take 0.5 moles of γ-aminopropylmethyldimethoxysilane and 0.5 moles of 3-aminopropyltriethoxysilane and dilute with 3.0 moles of ethanol to obtain an ethanol solution of alkoxysilane;
[0052] At 60°C, add 0.7 mol of water dropwise to the ethanol solution of alkoxysilane, stir for 1 hour, keep the temperature for 8 hours, remove the solvent, and obtain oligosiloxane;
[0053] At 75°C, add 5.0g of cardanol and 5.0g of 2,6-di-tert-butylphenol to 50.0g of oligosiloxane, and stir at constant temperature for 2 hours; then dropwise add 2.0g of triethylenetetramine and 1.2g of bis(4-amino-3-methylcyclohexyl)methane was stirred at constant temperature for 2 hours to prepare a novel epoxy resin curing agent.
[0054] Mix 32.0g of epoxy resin with 5.0g of talcum powder, 12.0g of mica iron oxide, and 10.0g of barium sulfate; then add 16.0g of oligosilicon epoxy resin curing agent and mix evenly to obtain coating 2, and evenly coat the substrate superior. Under room temperature, a...
Embodiment 3
[0056] Take 0.5 mole of 3-aminopropyltriethoxysilane and 0.5 mole of N-aminoethyl-3-aminopropylmethyldimethoxysilane and dilute with 4 moles of ethanol to obtain an ethanol solution of alkoxysilane;
[0057] At 20°C, add 0.9 moles of water dropwise to the ethanol solution of alkoxysilane, stir for 0.5 hours, keep the temperature for 12 hours, remove the solvent, and obtain oligosiloxane;
[0058] At 85°C, 5.8g of 2,6-di-tert-butylphenol and 6.4g of nonylphenol were added to 55.0g of oligosiloxane, stirred at constant temperature for 1.5 hours; then 3.0g of dicyandiamide was added dropwise, Stir at constant temperature for 1 hour to prepare a novel epoxy resin curing agent.
[0059] Mix 25.0g of epoxy resin with 12.0g of iron red, 6.0g of talcum powder, and 7.0g of mica powder; then add 15.0g of oligosilicon epoxy resin curing agent and mix evenly to obtain coating three, which is evenly coated on the substrate . Under room temperature, after standing for seven days, the perf...
PUM
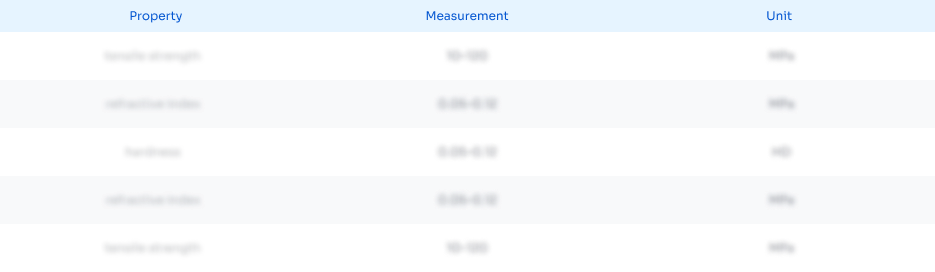
Abstract
Description
Claims
Application Information

- Generate Ideas
- Intellectual Property
- Life Sciences
- Materials
- Tech Scout
- Unparalleled Data Quality
- Higher Quality Content
- 60% Fewer Hallucinations
Browse by: Latest US Patents, China's latest patents, Technical Efficacy Thesaurus, Application Domain, Technology Topic, Popular Technical Reports.
© 2025 PatSnap. All rights reserved.Legal|Privacy policy|Modern Slavery Act Transparency Statement|Sitemap|About US| Contact US: help@patsnap.com