Silicon wafer stage double-stage exchange system by adopting air-floatation planar motor
A technology of plane motor and exchange system, which is applied to electrical components, electromechanical devices, and exposure devices for photoengraving processes, etc., can solve the problems of asymmetric force on the mover, complicated control, high precision of rail docking, etc., so as to avoid high motor power. , The effect of simplifying the control structure and improving the response speed
- Summary
- Abstract
- Description
- Claims
- Application Information
AI Technical Summary
Problems solved by technology
Method used
Image
Examples
Embodiment Construction
[0034] The specific structure, mechanism and working process of the present invention will be further described below in conjunction with the accompanying drawings.
[0035] The basic principle of step and scan projection lithography machine is as follows: figure 1 shown. The deep ultraviolet light from the light source 45 passes through the reticle 47 and the lens system 49 to image a part of the pattern on the reticle on a chip of the silicon wafer 50 . The reticle and the silicon wafer move synchronously in reverse at a certain speed ratio, and finally image all the patterns on the reticle on a specific chip (Chip) of the silicon wafer. The basic function of the wafer motion positioning system (wafer stage) is to carry the wafer during the exposure process and move according to the set speed and direction, so as to realize the precise transfer of the mask pattern to each area on the wafer.
[0036] The traditional step-and-scan projection lithography wafer stage such as ...
PUM
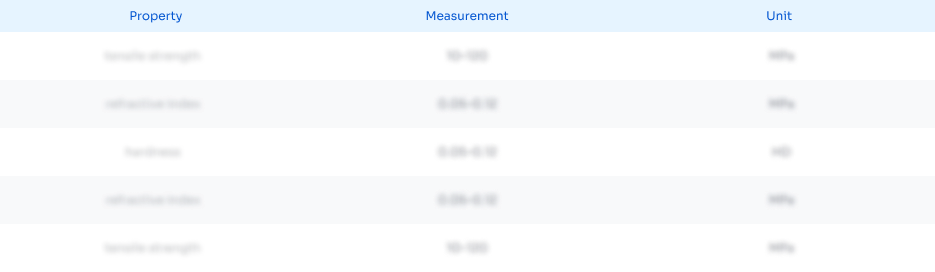
Abstract
Description
Claims
Application Information

- R&D
- Intellectual Property
- Life Sciences
- Materials
- Tech Scout
- Unparalleled Data Quality
- Higher Quality Content
- 60% Fewer Hallucinations
Browse by: Latest US Patents, China's latest patents, Technical Efficacy Thesaurus, Application Domain, Technology Topic, Popular Technical Reports.
© 2025 PatSnap. All rights reserved.Legal|Privacy policy|Modern Slavery Act Transparency Statement|Sitemap|About US| Contact US: help@patsnap.com