New production process of polyacrylamide-based high-efficiency paper fiber dispersant
A technology of polyacrylamide and acrylamide monomer, which is applied in fiber dispersant addition, papermaking, textiles and papermaking, etc. It can solve the problems of slow dissolution rate, poor dispersion effect, and high water insoluble matter, so as to improve the hydration rate, The effect of reducing the critical concentration and regularizing the main chain of the molecule
- Summary
- Abstract
- Description
- Claims
- Application Information
AI Technical Summary
Problems solved by technology
Method used
Examples
Embodiment 1
[0008] Example 1: Weigh 210 grams of acrylamide monomer, 45 grams of sodium carbonate, 1 gram of octylphenol polyoxyethylene ether, 10 grams of sodium bicarbonate, 42 grams of thiourea and 2.1 grams of allyloxynonylphenoxypropyl Alcohol polyoxyethylene ether sulfate is filled in a beaker with 790 grams of water, fully stirred, and the temperature is adjusted to 15°C. Then, the solution was poured into a vacuum flask to reduce the heat exchange between the system and the outside world, and nitrogen gas was introduced for 30 minutes to fully remove oxygen. Add 2 ml of 1% sodium formate, 1 ml of 1% 2,2-azobis(2-amidinopropane) hydrochloride, 1 ml of 1% sodium sulfite, 1 ml of 1% sodium persulfate, and cover the thermos cup Above, the polymerization was complete after 4 hours of adiabatic polymerization. The obtained jelly substance was taken out, heated to 80°C in a plastic bag for hydrolysis for 8 hours, purified with absolute ethanol, and dried in a vacuum desiccator at 65°C u...
Embodiment 2
[0009] Example 2: Weigh 210 grams of acrylamide monomer, 40 grams of sodium carbonate, 1 gram of sodium dodecylbenzenesulfonate, 15 grams of sodium bicarbonate, 12 grams of sodium hexametaphosphate and 2.1 grams of allyloxyhydroxypropyl Sodium sulfonate is contained in a beaker with 790 grams of water, fully stirred, and the temperature is adjusted to 15°C. Then, the solution was poured into a vacuum flask to reduce the heat exchange between the system and the outside world, and nitrogen gas was introduced for 30 minutes to fully remove oxygen. Add, 1 ml of 1% sodium formate, 1 ml of triethanolamine, 1 ml of 1% sodium sulfite, 1 ml of 1% sodium persulfate, cover the thermos cup, and complete the adiabatic polymerization after 4 hours. The obtained jelly substance was taken out, heated to 80°C in a plastic bag for hydrolysis for 8 hours, purified with absolute ethanol, and dried in a vacuum desiccator at 65°C until constant weight. The molecular weight of the obtained product ...
Embodiment 3
[0010] Example 3: Weigh 210 grams of acrylamide monomer, 45 grams of sodium carbonate, 10 grams of sodium bicarbonate, 12 grams of potassium pyrophosphate, 1 gram of sodium dodecylbenzenesulfonate and 2.1 grams of allyloxy hydroxypropyl sulfonate Sodium acid is contained in a beaker with 790 grams of water, fully stirred, and the temperature is adjusted to 15°C. Then, the solution was poured into a vacuum flask to reduce the heat exchange between the system and the outside world, and nitrogen gas was introduced for 30 minutes to fully remove oxygen. Add 1 milliliter of 1% azobisisobutylamidine hydrochloride, 1 milliliter of 1% sodium sulfite, and 1 milliliter of 1% sodium persulfate, cover the thermos cup, and complete the polymerization after 4 hours of adiabatic polymerization. The obtained jelly substance was taken out, heated to 80°C in a plastic bag for hydrolysis for 8 hours, purified with absolute ethanol, and dried in a vacuum desiccator at 65°C until constant weight. ...
PUM
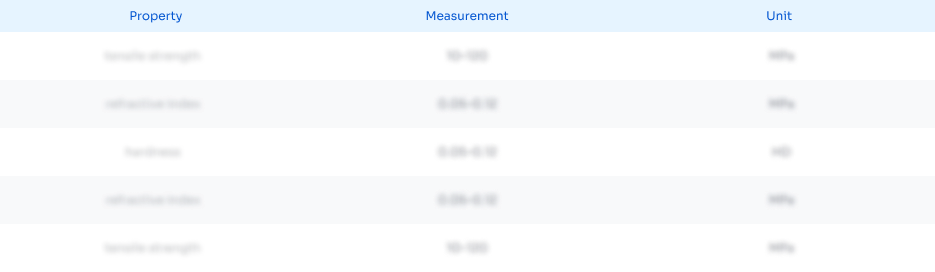
Abstract
Description
Claims
Application Information

- R&D
- Intellectual Property
- Life Sciences
- Materials
- Tech Scout
- Unparalleled Data Quality
- Higher Quality Content
- 60% Fewer Hallucinations
Browse by: Latest US Patents, China's latest patents, Technical Efficacy Thesaurus, Application Domain, Technology Topic, Popular Technical Reports.
© 2025 PatSnap. All rights reserved.Legal|Privacy policy|Modern Slavery Act Transparency Statement|Sitemap|About US| Contact US: help@patsnap.com