Method for preparing polyurethane-polyacrylic ester microemulsion
A polyacrylate and microemulsion technology, applied in the field of polymer chemistry, can solve the problems of difficult process control, easy gelation, and low cost, and achieve the effects of reducing VOC content, protecting the environment, and saving costs
- Summary
- Abstract
- Description
- Claims
- Application Information
AI Technical Summary
Problems solved by technology
Method used
Examples
Embodiment 1
[0025] 1) Add 8 parts of poly(hexanediol adipate) to the drying reactor in parts by mass and degas it in vacuum at 120°C for 2 hours, then pass nitrogen into it, and cool down to 70°C;
[0026] 2) Add 23 parts of methyl methacrylate and 13 parts of hexamethylene diisocyanate (HDI) to poly(hexanediol adipate) successively at 70°C, and react for 1 hour;
[0027] 3) Add 3 parts of N-methyldiethanolamine and 0.005 parts of dibutyltin dilaurate to it, and continue the reaction at 70° C. for 1 hour;
[0028] 4) After cooling the system temperature to 50°C, add 5 parts of dimethyl sulfate, 100 parts of water and 0.5 parts of unsaturated ethylenic monomer hydroxyethyl methacrylate for half an hour, then raise the temperature to 70°C, and finally add 0.5 parts of hydrogen peroxide, continue to keep warm and react for 8 hours until the reaction is completed without the smell of acrylate monomers, and a yellow translucent polyurethane-polyacrylate microemulsion is obtained.
Embodiment 2
[0030] 1) Add 15 parts of polybutylene adipate to the drying reactor in parts by mass and degas it under vacuum at 115°C for 1 hour, then pass nitrogen into it, and cool down to 60°C;
[0031] 2) Add 17 parts of methyl acrylate and 18 parts of isophorone diisocyanate (IPDI) to polybutylene adipate successively at 60°C, and react for 2 hours;
[0032] 3) Add 5 parts of N-methyldiethanolamine and 0.008 parts of dibutyltin diacetate to it, and continue the reaction at 60° C. for 3 hours;
[0033] 4) Then cool the system temperature to 30°C, then add 3 parts of 1mol / l hydrochloric acid, 230 parts of water and 4 parts of unsaturated ethylenic monomer hydroxyethyl acrylate for half an hour, then raise the temperature to 90°C, and finally add 2 100% water-soluble azo initiator, continue the heat preservation reaction for 5 hours until the reaction is completed without the smell of acrylate monomers, and a yellow translucent polyurethane-polyacrylate microemulsion is obtained.
Embodiment 3
[0035] 1) Add 23 parts of polyethylene adipate to the drying reactor in parts by mass and degas it in vacuum at 118°C for 1.5 hours, then pass in nitrogen and cool down to 50°C;
[0036] 2) Add 8 parts of ethyl acrylate and 6 parts of toluene diisocyanate (TDI) to polyethylene adipate in turn at 50°C, and react for 4 hours;
[0037] 3) Add 8 parts of N-methyldiethanolamine and 0.02 parts of stannous octoate to it, and continue the reaction at 50° C. for 4 hours;
[0038]4) After cooling the system temperature to 20°C, add 8 parts of or anhydrous acetic acid, 360 parts of water and 8 parts of unsaturated ethylenic monomer hydroxypropyl acrylate for half an hour, then raise the temperature to 60°C, and finally add 4 parts hydrogen peroxide, and continue to keep warm for 3 hours until the reaction is completed without the smell of acrylate monomers, and a yellow translucent polyurethane-polyacrylate microemulsion is obtained.
PUM
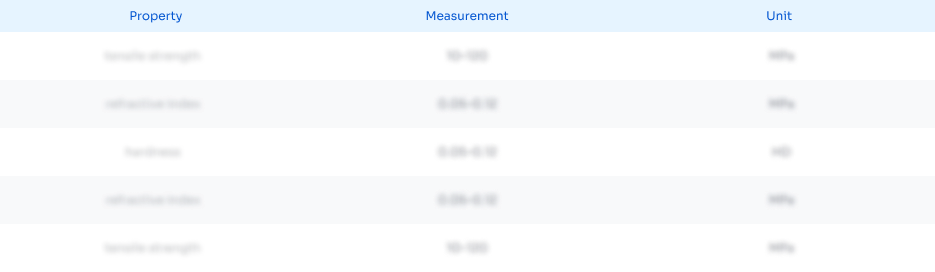
Abstract
Description
Claims
Application Information

- R&D Engineer
- R&D Manager
- IP Professional
- Industry Leading Data Capabilities
- Powerful AI technology
- Patent DNA Extraction
Browse by: Latest US Patents, China's latest patents, Technical Efficacy Thesaurus, Application Domain, Technology Topic, Popular Technical Reports.
© 2024 PatSnap. All rights reserved.Legal|Privacy policy|Modern Slavery Act Transparency Statement|Sitemap|About US| Contact US: help@patsnap.com