Hollow glass microballoons and production method thereof
A technology of hollow glass microspheres and parts by weight, which is applied in glass forming, glass manufacturing equipment, manufacturing tools, etc., can solve the problems of high production cost, poor adjustability, and small particles.
- Summary
- Abstract
- Description
- Claims
- Application Information
AI Technical Summary
Problems solved by technology
Method used
Examples
Embodiment Construction
[0024] 1. The preparation method of hollow glass microspheres, which includes batching, melting, crushing, drying, pulverizing, grading, hollow spheroidizing, collecting, winnowing, and testing. The breakdown is as follows.
[0025] 1. Ingredients: Weigh the raw materials according to the chemical composition formula of the glass frit and mix them evenly.
[0026] 2. Melting: Put the uniformly mixed material into the crucible, and then send the crucible to the optical glass melting furnace for melting. The melting temperature is 1400-1600°C.
[0027] 3. Water crushing: Pour the melted glass liquid into the water tank to cool it.
[0028] 4. Drying: Dry the crushed material.
[0029] 5. Crush: crush the dried glass.
[0030] 6. Classification: Classify the pulverized glass powder into a powder with a particle size distribution of 30-100 μm.
[0031] 7. Hollow spheroidization: Put the processed glass raw materials into the feed bin, the feed port is set at the bottom of the...
PUM
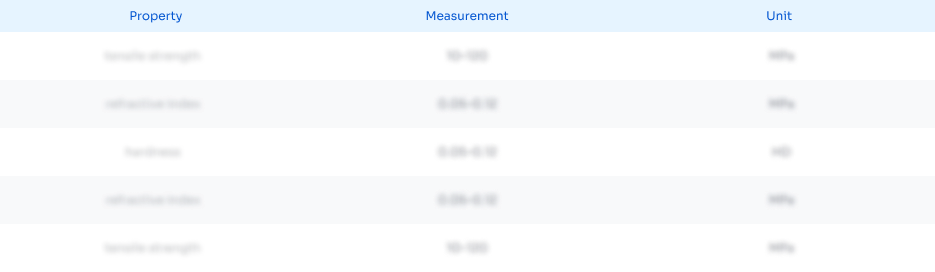
Abstract
Description
Claims
Application Information

- R&D
- Intellectual Property
- Life Sciences
- Materials
- Tech Scout
- Unparalleled Data Quality
- Higher Quality Content
- 60% Fewer Hallucinations
Browse by: Latest US Patents, China's latest patents, Technical Efficacy Thesaurus, Application Domain, Technology Topic, Popular Technical Reports.
© 2025 PatSnap. All rights reserved.Legal|Privacy policy|Modern Slavery Act Transparency Statement|Sitemap|About US| Contact US: help@patsnap.com