Raw material formulation of ladle heat insulation cover and preparation method of ladle heat insulation cover
A technology of thermal insulation cover and ladle, applied in the field of refractory materials, can solve the problems of erosion, deterioration and hardening of thermal insulation cotton, long residence time, poor thermal insulation effect, etc., and achieve the effect of reducing raw material cost, good construction performance, and good thermal shock resistance stability.
- Summary
- Abstract
- Description
- Claims
- Application Information
AI Technical Summary
Problems solved by technology
Method used
Examples
Embodiment 1
[0019] Embodiment 1, the raw material formula of ladle insulation cover, described raw material (mass percentage) is made of 45% brown corundum hollow ball, 15% brown corundum, 26% mullite, 6% alumina fine powder, 6% silicon fine powder, 1.9% ρ-Al 2 o 3 Powder, 0.1% dispersant composition. The granularity requirements of the raw materials are brown corundum hollow sphere particles of 8-0.1 mm, brown corundum fine powder of 180 mesh, and mullite fine powder of 180 mesh.
[0020] The preparation method that adopts above-mentioned raw material formula to make ladle insulation cover comprises the steps:
[0021] 1) Stir the prepared raw materials evenly, and the raw materials are added in the order of brown corundum hollow sphere particles-silica powder and ρ-Al 2 o 3 , Dispersant fine powder - brown corundum and mullite fine powder - superplasticizer;
[0022] 2) Add 6% water of the total mass of raw materials to the stirred raw materials and mix and stir for 3-5 minutes;
...
Embodiment 2
[0025] Embodiment 2, the raw material formula of ladle insulation cover, described raw material (mass percentage) is made of 50% brown corundum hollow ball, 18% brown corundum, 15% mullite, 8% alumina micropowder, 5% silicon micropowder, 3.8% ρ-Al 2 o 3 Powder, 0.2% dispersant composition. The granularity requirements of the raw materials are brown corundum hollow sphere particles of 8-0.1 mm, brown corundum fine powder of 180 mesh, and mullite fine powder of 180 mesh.
[0026] The preparation method that adopts above-mentioned raw material formula to make ladle insulation cover comprises the steps:
[0027] 1) Stir the prepared raw materials evenly, and the raw materials are added in the order of brown corundum hollow sphere particles-silica powder and ρ-Al 2 o 3 , Dispersant fine powder - brown corundum and mullite fine powder - superplasticizer;
[0028] 2) Add water with 8% of the total mass of raw materials to the stirred raw materials and mix and stir for 3-5 minute...
Embodiment 3
[0031] Embodiment 3, the raw material formula of ladle insulation cover, described raw material (mass percentage) is made of 40% brown corundum hollow ball, 16.8% brown corundum, 25% mullite, 7% alumina micropowder, 6% silicon micropowder, 5% ρ-Al 2 o 3 Powder, 0.2% dispersant composition. The granularity requirements of the raw materials are brown corundum hollow sphere particles of 8-0.1 mm, brown corundum fine powder of 180 mesh, and mullite fine powder of 180 mesh.
[0032] The preparation method that adopts above-mentioned raw material formula to make ladle insulation cover comprises the steps:
[0033] 1) Stir the prepared raw materials evenly, and the raw materials are added in the order of brown corundum hollow sphere particles-silica powder and ρ-Al 2 o 3 , Dispersant fine powder - brown corundum and mullite fine powder - superplasticizer;
[0034] 2) Add water with 7% of the total mass of raw materials to the stirred raw materials and mix and stir for 3-5 minute...
PUM
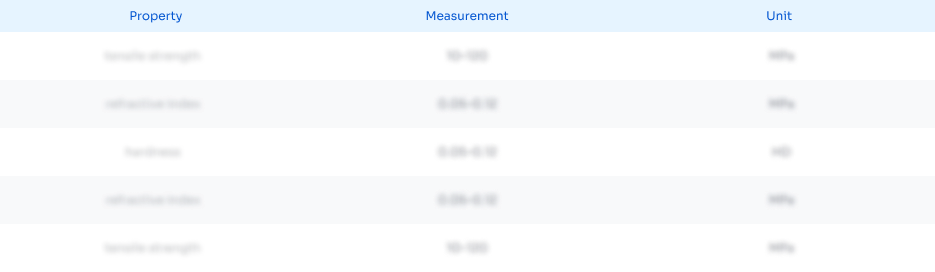
Abstract
Description
Claims
Application Information

- Generate Ideas
- Intellectual Property
- Life Sciences
- Materials
- Tech Scout
- Unparalleled Data Quality
- Higher Quality Content
- 60% Fewer Hallucinations
Browse by: Latest US Patents, China's latest patents, Technical Efficacy Thesaurus, Application Domain, Technology Topic, Popular Technical Reports.
© 2025 PatSnap. All rights reserved.Legal|Privacy policy|Modern Slavery Act Transparency Statement|Sitemap|About US| Contact US: help@patsnap.com