Anode oxidation method
A technology of anodic oxidation and anode, which is applied in the direction of anodic oxidation, can solve the problems of poor corrosion resistance, and achieve the effect of strong corrosion resistance and improved corrosion resistance
- Summary
- Abstract
- Description
- Claims
- Application Information
AI Technical Summary
Problems solved by technology
Method used
Image
Examples
Embodiment 1
[0026] This example is used to illustrate the anodic oxidation method provided by the present invention.
[0027] 1. Pretreatment
[0028] (1) Grinding
[0029] The AZ91D magnesium alloy substrate (Nanjing Yunhai Special Metal Co., Ltd.) with a size of 80×50×2 mm is polished with sandpaper, and the rough natural oxide film on the surface of the magnesium alloy substrate is removed until the surface of the magnesium alloy substrate shows metal Gloss is enough.
[0030] 2. Anodizing
[0031] The above-mentioned pretreated magnesium alloy substrate is used as an anode and immersed in an electrolyte solution, and at the same time, stainless steel is used as a cathode, and the cathode and anode are respectively electrically connected to the positive and negative electrodes of the power supply. Using 2 g / L sodium hydroxide, 5 g / L sodium fluoroborate, 10 g / L sodium silicate, 0.5 g / L sodium tetraborate, 1 g / L potassium oxalate and 1 mL / L The solution composed of glycerol is used a...
Embodiment 2
[0039] This example is used to illustrate the anodic oxidation method provided by the present invention.
[0040] Prepare the AZ91D magnesium alloy base material (Nanjing Yunhai Special Metals Co., Ltd.) with the same method as Example 1 and carry out pretreatment and anodic oxidation. The difference is that the anodic oxidation adopts the following method:
[0041] The above-mentioned pretreated magnesium alloy substrate is used as an anode and immersed in an electrolyte solution, and at the same time, stainless steel is used as a cathode, and the cathode and anode are respectively electrically connected to the positive and negative electrodes of the power supply. Using 5 g / L of sodium hydroxide, 8 g / L of sodium fluoroborate, 12 g / L of sodium silicate, 1 g / L of sodium tetraborate, 1.5 g / L of potassium oxalate and 2 mL / L The solution composed of isopropylene glycol is used as the electrolyte, the power supply used is a pulse power supply, the adjustment frequency is 400 Hz, th...
Embodiment 3
[0043] This example is used to illustrate the anodic oxidation method provided by the present invention.
[0044] Prepare the AZ91D magnesium alloy base material (Nanjing Yunhai Special Metals Co., Ltd.) with the same method as Example 1 and carry out pretreatment and anodic oxidation. The difference is that the anodic oxidation adopts the following method:
[0045] The above-mentioned pretreated magnesium alloy substrate is used as an anode and immersed in an electrolyte solution, and at the same time, stainless steel is used as a cathode, and the cathode and anode are respectively electrically connected to the positive and negative electrodes of the power supply. Using 7 g / L of sodium hydroxide, 10 g / L of sodium fluoroborate, 15 g / L of sodium silicate, 3 g / L of sodium tetraborate, 2 g / L of potassium oxalate and 3 mL / L The solution composed of glycerin is used as the electrolyte, the power supply used is a pulse power supply, the adjustment frequency is 500 Hz, the duty ratio...
PUM
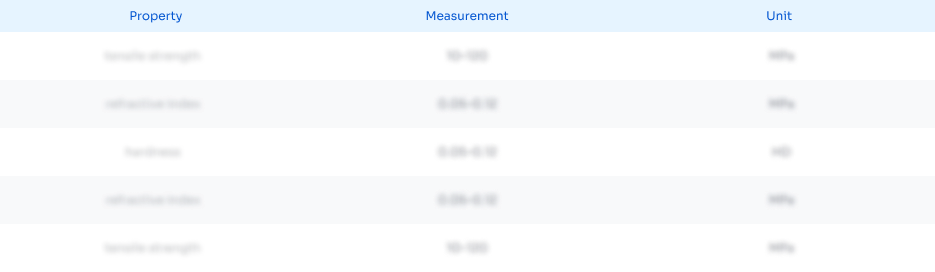
Abstract
Description
Claims
Application Information

- R&D
- Intellectual Property
- Life Sciences
- Materials
- Tech Scout
- Unparalleled Data Quality
- Higher Quality Content
- 60% Fewer Hallucinations
Browse by: Latest US Patents, China's latest patents, Technical Efficacy Thesaurus, Application Domain, Technology Topic, Popular Technical Reports.
© 2025 PatSnap. All rights reserved.Legal|Privacy policy|Modern Slavery Act Transparency Statement|Sitemap|About US| Contact US: help@patsnap.com