Preparation method for organically-modified nano-silica/nylon 66 composite material
A nano-silica, composite material technology, applied in the direction of dyeing low-molecular-weight organic compounds, fibrous fillers, etc., can solve the problems of limited performance improvement, poor dispersion of nano-silica, reduce agglomeration, improve dispersive effect
- Summary
- Abstract
- Description
- Claims
- Application Information
AI Technical Summary
Problems solved by technology
Method used
Examples
Embodiment 1
[0015] The first step: preparation of organically modified nano-silica
[0016] Add 40mL of ethyl orthosilicate, 80mL of absolute ethanol, and 12mL of distilled water into a 500mL three-neck flask, raise the temperature to 45°C, stir mechanically for 10min, add ammonia water 2.0mL, and hydrolyze for 6-8h. Then 1.2 mL of silane coupling agent γ-aminopropyltriethoxysilane was added, and the reaction was continued at 45° C. for 8 h. Then add 100mL of distilled water, remove ethanol and ammonia water under vacuum at 50°C, and obtain 100mL of γ-aminopropyltriethoxysilane organically modified nano-silica suspension, wherein γ-aminopropyltriethoxysilane The mass of organically modified nano silicon dioxide is 10g.
[0017] The second step: preparation of organically modified nano-silica / nylon 66 composites
[0018] Add the suspension of 100mL of γ-aminopropyltriethoxysilane organically modified nano-silica prepared above to 990g of nylon 66 salt, then add distilled water to 1430g t...
Embodiment 2
[0020] The first step: preparation of organically modified nano-silica
[0021] Add 80 mL of tetraethyl orthosilicate, 160 mL of absolute ethanol, and 24 mL of distilled water into a 500 mL three-necked flask, raise the temperature to 50°C, stir mechanically, add 4.0 mL of ammonia water after 5 min, and hydrolyze for 8 h. Then 2.4 mL of silane coupling agent γ-(2,3-glycidoxy)propyltrimethoxysilane was added, and the reaction was continued at 50° C. for 8 h. Then add 200mL of distilled water, and remove ethanol under vacuum at 65°C to obtain a suspension of 200mL of γ-(2,3-epoxypropoxy)propyltrimethoxysilane organically modified nano-silica, wherein γ-(2 , 3-glycidoxy) propyltrimethoxysilane organically modified nano-silica quality is 20g.
[0022] The second step: preparation of organically modified nano-silica / nylon 66 composites
[0023] Add the suspension of 200mL of γ-(2,3-glycidyloxy)propyltrimethoxysilane organically modified nano-silica prepared above to 980g of nylon...
Embodiment 3
[0025] The first step: preparation of organically modified nano-silica
[0026] Add 120 mL of tetraethyl orthosilicate, 240 mL of absolute ethanol, and 36 mL of distilled water into a 1000 mL three-neck flask, raise the temperature to 55°C, stir mechanically, add 6.0 mL of ammonia water after 5 minutes, and hydrolyze for 8 hours. Then 3.6 mL of silane coupling agent γ-aminopropyltriethoxysilane was added, and the reaction was continued at 55° C. for 8 h. Then add 300mL of distilled water, vacuumize at 65°C to remove ethanol, and obtain 300mL of γ-aminopropyltriethoxysilane organically modified nano-silica suspension, in which γ-aminopropyltriethoxysilane is organically modified The mass of nanometer silicon dioxide is 30g.
[0027] The second step: preparation of organically modified nano-silica / nylon 66 composites
[0028] Add the suspension of 300mL of γ-aminopropyltriethoxysilane organically modified nano-silica prepared above to 960g of nylon 66 salt, and then add distil...
PUM
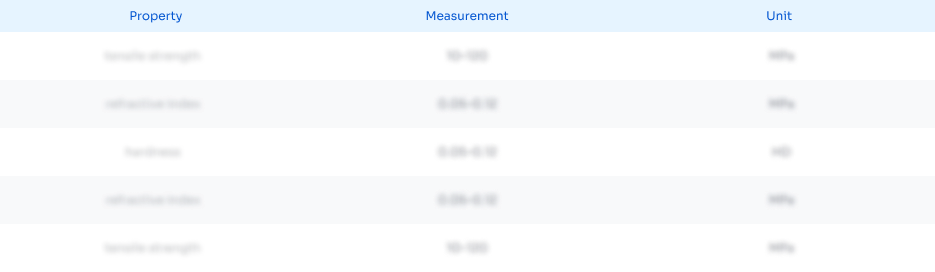
Abstract
Description
Claims
Application Information

- R&D
- Intellectual Property
- Life Sciences
- Materials
- Tech Scout
- Unparalleled Data Quality
- Higher Quality Content
- 60% Fewer Hallucinations
Browse by: Latest US Patents, China's latest patents, Technical Efficacy Thesaurus, Application Domain, Technology Topic, Popular Technical Reports.
© 2025 PatSnap. All rights reserved.Legal|Privacy policy|Modern Slavery Act Transparency Statement|Sitemap|About US| Contact US: help@patsnap.com