Process for performing steel-strip film coating by using pulse laser evaporation ablation in vacuum
A pulsed laser, strip steel technology, applied in vacuum evaporation coating, metal material coating process, sputtering coating and other directions, can solve problems such as inability to meet, and achieve high production efficiency, good product quality, and fast response speed. Effect
- Summary
- Abstract
- Description
- Claims
- Application Information
AI Technical Summary
Problems solved by technology
Method used
Examples
Embodiment 1
[0037] Deposition of antibacterial TiO on 100mm wide stainless steel plate 2 film.
[0038] In the present embodiment, select the TiO that only contains pure anatase phase for use 2 As a target, TiO is deposited on the surface of stainless steel coils 2 plating.
[0039] Use a KrF excitation source laser with a wavelength of 248nm, a repetition rate of 10Hz, an incident angle of 45 degrees, and a vacuum degree of 3.5×10 -5 mbar. A laser can be placed on both sides of the steel plate, and a 100mm rectangular target can be used in the vacuum chamber.
[0040] The cold-rolled sheet passes through at 0.1mm / min, which can achieve 20nm anatase phase TiO2 coating. XRD analysis shows that the sample coating is pure anatase phase, which has good antibacterial properties. The error of thickness from the surface analyzed by ellipsometer is within 1%.
Embodiment 2
[0042] A wear-resistant Fe-V 10nm thick alloy coating was prepared on a stainless steel plate.
[0043]In this embodiment, a Fe-V alloy with a Fe content of 48% is selected as the target material, and Fe-V alloy with the same composition is deposited on the surface of the stainless steel coil to improve its wear resistance.
[0044] Use Nd:YAG laser with a wavelength of 532nm, a repetition rate of 10Hz, an incident angle of 45 degrees, and a vacuum degree of 3.5×10 -5 mbar; pulse interval is 10ns; laser energy is 5.3J / cm 2 . A laser can be placed on both sides of the steel plate, and a 100mm rectangular target can be used in the vacuum chamber.
[0045] The stainless steel passes through at 0.5m / min, which can realize the coating preparation of 10nm Fe-V alloy. EDX results show that the content of Fe on the surface varies between 43-58%, which is very similar to the composition of the target.
Embodiment 3
[0047] Preparation of stainless steel coatings on cold-rolled panels.
[0048] In this embodiment, block 304 stainless steel is selected as the target material, and a stainless steel coating with the same composition is deposited on the surface of the cold-rolled plate to improve corrosion resistance.
[0049] Use a pulsed ruby laser with a wavelength of 694nm, a repetition rate of 5Hz, an incident angle of 45 degrees, and a vacuum of 3.5×10 -5 mbar; the pulse interval is 30ns; after the steel plate is preheated by the laser beam, it enters the pulse laser coating unit. Laser energy at 10J / cm 2 . A laser can be placed on both sides of the steel plate, and three sets of targets and lasers can be placed in the running direction of the steel strip to increase the coating speed.
[0050] The stainless steel passes through at 5m / min, which can realize the coating preparation of 30nm Fe-V alloy. EDX analysis shows that the surface is similar to the original target material. SE...
PUM
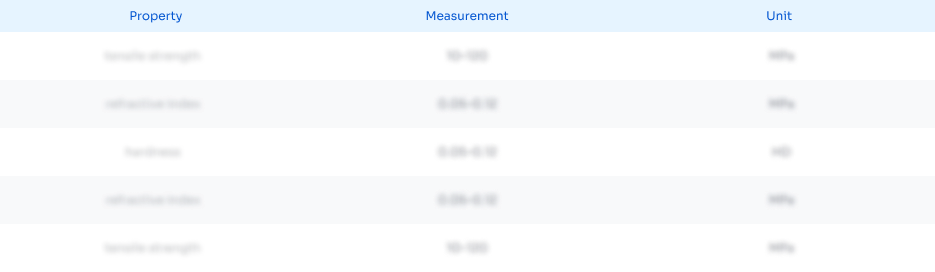
Abstract
Description
Claims
Application Information

- Generate Ideas
- Intellectual Property
- Life Sciences
- Materials
- Tech Scout
- Unparalleled Data Quality
- Higher Quality Content
- 60% Fewer Hallucinations
Browse by: Latest US Patents, China's latest patents, Technical Efficacy Thesaurus, Application Domain, Technology Topic, Popular Technical Reports.
© 2025 PatSnap. All rights reserved.Legal|Privacy policy|Modern Slavery Act Transparency Statement|Sitemap|About US| Contact US: help@patsnap.com