Cast-in-situ fire-proof door and method for manufacturing same
A fire door, cast-in-place technology, applied in fire doors, chemical instruments and methods, door leaves, etc., can solve the problems of increased weight of door leaves, insufficient flexibility, and long fixed molding time.
- Summary
- Abstract
- Description
- Claims
- Application Information
AI Technical Summary
Problems solved by technology
Method used
Image
Examples
Embodiment 2
[0036] Embodiment 2: be respectively magnesium oxide 30% by weight: magnesium chloride solution 50%: modification agent 3%: short fiber 1%: fly ash 5%, all the other add wood sawdust, this example adopts light material wood sawdust to further The weight of the entire inorganic cementitious material is reduced, and the gaps of the wood sawdust soaked in magnesium chloride solution are completely filled with flame retardants, so that the entire door leaf is completely isolated from heat transmission due to the uniform distribution of flame retardant materials when it encounters fire.
Embodiment 3
[0037] Embodiment 3: respectively by weight magnesia 60%: magnesium chloride solution 17%: modification agent 0.5%: short fiber 1%: fly ash 5%, all the other add 8% vitrified microbead particles and 8.5% glass microspheres beads. In this example, the use of light-weight material vitrified microspheres and glass microspheres can enhance the compression resistance of the entire fire door in the context of the aforementioned beneficial effects, and is suitable for buildings that require hardness and strength.
Embodiment 4
[0038] Embodiment 4: be respectively magnesium oxide 35% by weight: magnesium chloride solution 40%: modification agent 0.5%: short fiber 1%: fly ash 5%, all the other add 3% ceramic mud ball, 1.5% glass microsphere, 3% wood sawdust, 3% slag, 3% expanded perlite particles, 2% high phosphorus soil, 3% plant fiber. This example not only has high fire resistance, but also has the characteristics of light weight, heat insulation, high strength and high hardness.
[0039] The magnesium chloride solution glassy degree is 22 °-29 ° among the above each embodiment.
[0040] In this program, when filling the space of the keel skeleton, the inorganic gelling material is foamed and mixed, and the foaming agent used in the foam is 85% by weight of animal protein, 14.9% of sodium lauryl sulfate solution and a foam stabilizer 0.1% mixed, this combination can make the generated foam have the best stability, not easy to burst and the volume of the foam is not far apart. The foam stabilizer ...
PUM
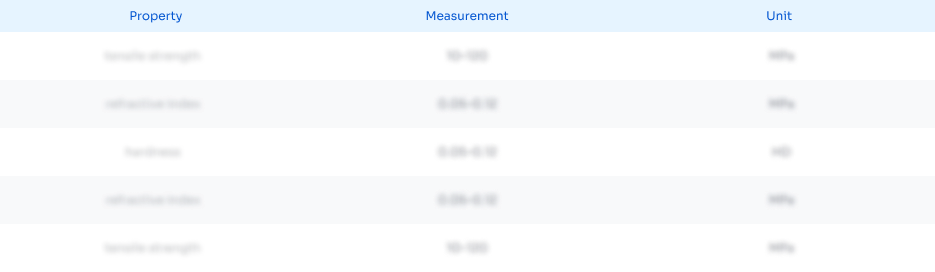
Abstract
Description
Claims
Application Information

- Generate Ideas
- Intellectual Property
- Life Sciences
- Materials
- Tech Scout
- Unparalleled Data Quality
- Higher Quality Content
- 60% Fewer Hallucinations
Browse by: Latest US Patents, China's latest patents, Technical Efficacy Thesaurus, Application Domain, Technology Topic, Popular Technical Reports.
© 2025 PatSnap. All rights reserved.Legal|Privacy policy|Modern Slavery Act Transparency Statement|Sitemap|About US| Contact US: help@patsnap.com