High-alloy centrifugal compound cast steel supporting roll and manufacturing technology thereof
A technology of centrifugal composite and backup rolls, which is applied in manufacturing tools, metal rolling, metal rolling, etc., can solve the problems of reduced production efficiency, short service life, large economic burden on enterprises, etc., so as to improve the work yield and service life. The effect of improving and anti-accident performance
- Summary
- Abstract
- Description
- Claims
- Application Information
AI Technical Summary
Problems solved by technology
Method used
Image
Examples
Embodiment 1
[0026] Example 1: According to the composition of the working layer of the high-alloy centrifugal composite cast steel backup roll, put the proportioned scrap steel into the induction furnace for smelting, analyze the chemical substances of the original molten steel after melting, and then add the corresponding alloy raw materials according to the process, and smelt to obtain chemical Composition: Working layer: C 0.40%, S 0.025%, Si 0.46%, Mn 0.40%, P 0.030%, Ni 0.20%, Cr 4.50%, Mo 0.35%, and the rest is scrap steel and impurities in the working layer molten steel (the scrap steel is 93.36 %, impurity is 0.05%), core: C 3.00%, S 0.008%, Si 2.00%, Mn 0.20%, P 0.050%, Ni 0.20%, Cr 1.00%, Mo 0.50%, Re 0.040%, Mg 0.03% , the rest is molten iron with iron and impurities (including 45% pig iron, 20% steel scrap, 27.99% recycled materials, and 0.012% impurities), centrifugally cast high-alloy centrifugal composite cast steel backup rolls, and the tapping temperature of the working la...
Embodiment 2
[0027] Example 2: According to the composition of the working layer of the high-alloy centrifugal composite cast steel backup roll, put the proportioned scrap steel into the induction furnace for smelting, analyze the chemical substances of the original molten steel after melting, and then add the corresponding alloy raw materials according to the process, and smelt to obtain chemical Composition: Working layer: C 0.45%, S 0.020%, Si 0.30%, Mn 0.62%, P 0.025%, Ni 0.60%, Cr 4.00%, Mo 0.20%, and the rest is scrap steel and impurities in the working layer molten steel (the proportion of scrap steel 93.75%, impurity proportion 0.035%, core: C 3.60%, S 0.003%, Si 1.70%, Mn 0.63%, P 0.069%, Ni 0.50%, Cr 0.55%, Mo 0.10%, Re 0.02%, Mg 0.055 %The rest is molten iron of iron and impurities (wherein pig iron accounts for 46%, steel scrap accounts for 22.5%, returned material accounts for 24.22%, and impurities account for 0.053%). Centrifugally cast high-alloy centrifugal composite cast s...
Embodiment 3
[0028] Example 3: According to the composition of the working layer of the high-alloy centrifugal composite cast steel backup roll, put the proportioned scrap steel into the induction furnace for melting, analyze the chemical substances of the original molten steel after melting, and then add the corresponding alloy raw materials according to the process, and melt to obtain chemical Composition: Working layer: C 0.50%, S 0.028%, Si 0.60%, Mn 0.80%, P 0.034%, Ni 1.00%, Cr 3.50%, Mo 0.50%, and the rest is scrap steel and impurities in the working layer molten steel, (of which scrap steel accounts for Specific gravity 93%, impurity proportion 0.038%) Core: C 3.60%, S 0.005%, Si 2.70%, Mn 1.00%, P 0.045%, Ni 0.80%, Cr 0.20%, Mo 1.00%, Re 0.010%, Mg The rest of 0.08% is molten iron of iron and impurities (wherein pig iron accounts for 44%, steel scrap accounts for 20.8%, recycled material accounts for 25.73%, and impurities account for 0.03%). Centrifugal casting of high-alloy cent...
PUM
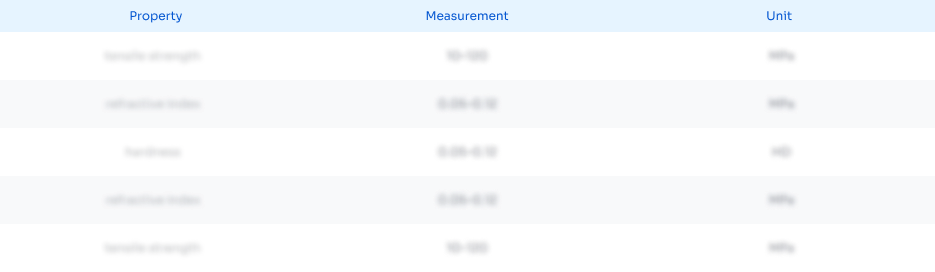
Abstract
Description
Claims
Application Information

- R&D
- Intellectual Property
- Life Sciences
- Materials
- Tech Scout
- Unparalleled Data Quality
- Higher Quality Content
- 60% Fewer Hallucinations
Browse by: Latest US Patents, China's latest patents, Technical Efficacy Thesaurus, Application Domain, Technology Topic, Popular Technical Reports.
© 2025 PatSnap. All rights reserved.Legal|Privacy policy|Modern Slavery Act Transparency Statement|Sitemap|About US| Contact US: help@patsnap.com