Direct spinning process for preparing PPTA fibre by end capping resin method
A resin and process technology, applied in the field of chemical and polymer materials, can solve the problems of corrosion of production equipment, damage to the human body, and complicated operation processes, and achieve the effect of improving production efficiency, reducing human damage and environmental pollution
- Summary
- Abstract
- Description
- Claims
- Application Information
AI Technical Summary
Problems solved by technology
Method used
Image
Examples
Embodiment 1
[0009] In a 200L polymerization kettle, inject 80 kilograms of N-methylpyrrolidone (NMP) solutions that are dissolved with 5% lithium chloride (LiCl), and add 3.244 kilograms (30mol) of p-phenylenediamine (PPDA) at 15° C. Make it fully dissolved, make NMP-LiCl-PPDA solution, carry out stirring reaction under normal pressure, keep the reaction temperature at -5°C ~ 5°C, slowly add 6.091 kg (30mol) of terephthaloyl chloride (TPC) After 1 to 5 minutes, 0.23 kg of phenylethylamine was added, and after 1 to 5 minutes of reaction, 0.23 kg of benzoic acid was added to obtain a blocked PPTA oligomer-NMP-LiCl composite solution. At room temperature, add 7L of pyridine and 5.0 kg of p-phenylenediamine powder to the composite solution, and after it is completely dissolved, cool to a certain temperature, then add 9.45 kg of terephthaloyl chloride powder, and react with high-speed stirring for 20 to 25 minutes . The solution spinning temperature was adjusted to 85°C, and PPTA fibers were ...
Embodiment 2
[0011] In a 200L polymerization kettle, inject 7% calcium chloride (CaCl 2 ) of N-methylpyrrolidone (NMP) solution 100 kg, add 3.244 kg (30mol) of p-phenylenediamine (PPDA) at 15°C to fully dissolve it, and make NMP-LiCl-PPDA solution, Stir the reaction under pressure, maintain the reaction temperature at -5°C to 5°C, slowly add 6.091 kg (30mol) of terephthaloyl chloride (TPC), add 0.30 kg of phenethylamine after 1 to 5 minutes, and react 1 to 5 minutes. Minutes later, 0.30 kg of benzoic acid was added to obtain a capped PPTA oligomer-NMP-LiCl composite solution. At room temperature, add 5 L of pyridine and 4.0 kg of p-phenylenediamine powder to the composite solution, after it is completely dissolved, cool to a certain temperature, then add 7.56 kg of terephthaloyl chloride powder, and react with high-speed stirring for 20 to 25 minutes . The solution spinning temperature was adjusted to 85°C, and PPTA fibers were obtained through extrusion-wet spinning-coagulation bath pro...
Embodiment 3
[0013] In a 200L polymerization kettle, inject 100 kg of N-methylpyrrolidone (NMP) solution that is dissolved with 5% lithium chloride (LiCl), add 3.244 kg (30mol) of p-phenylenediamine (PPDA) at 15°C, Make it fully dissolved, make NMP-LiCl-PPDA solution, carry out stirring reaction under normal pressure, keep the reaction temperature at -5°C ~ 5°C, slowly add 6.091 kg (30mol) of terephthaloyl chloride (TPC) After 1 to 5 minutes, 0.45 kg of phenylethylamine was added, and after 1 to 5 minutes of reaction, 0.45 kg of benzoic acid was added to prepare a blocked PPTA oligomer-NMP-LiCl composite solution. At room temperature, add 5 L of pyridine and 5.0 kg of p-phenylenediamine powder into the composite solution, and after it is completely dissolved, cool to a certain temperature, then add 9.45 kg of terephthaloyl chloride powder, and react with high-speed stirring for 20 to 25 minutes . The solution spinning temperature was adjusted to 85°C, and PPTA fibers were obtained through...
PUM
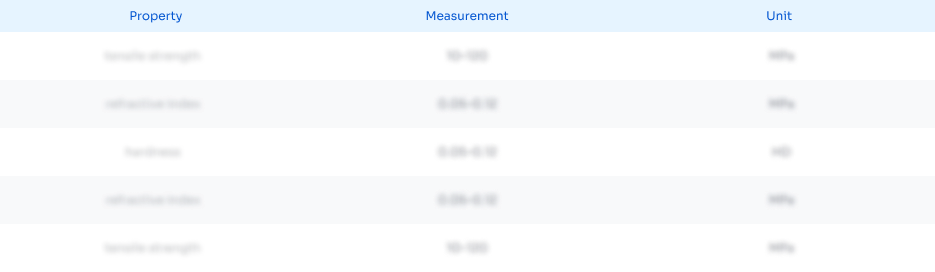
Abstract
Description
Claims
Application Information

- R&D
- Intellectual Property
- Life Sciences
- Materials
- Tech Scout
- Unparalleled Data Quality
- Higher Quality Content
- 60% Fewer Hallucinations
Browse by: Latest US Patents, China's latest patents, Technical Efficacy Thesaurus, Application Domain, Technology Topic, Popular Technical Reports.
© 2025 PatSnap. All rights reserved.Legal|Privacy policy|Modern Slavery Act Transparency Statement|Sitemap|About US| Contact US: help@patsnap.com