Production method of plane continuous diffraction condensing lens
A concentrating lens and plane technology, which is applied in the field of plane continuous diffraction concentrating lens, can solve the problems of cumbersome process, low processing precision, and low diffraction efficiency, and achieve the goal of improving diffraction efficiency, improving manufacturing accuracy, and high product qualification rate Effect
- Summary
- Abstract
- Description
- Claims
- Application Information
AI Technical Summary
Problems solved by technology
Method used
Examples
Embodiment 1
[0014] 1. Fabrication of planar continuous diffractive condenser lens mask
[0015] Soak in a mixed solution of potassium dichromate and concentrated sulfuric acid for 3.5 hours; scrub and rinse with deionized water; then spin dry with a glue spinner, bake in a dryer at 80°C for 35 minutes, and finally cool at room temperature. Coat photoresist on the cleaned substrate surface, photoresist type S1860. The gluing adopts the rotary gluing method, and the gluing equipment adopts a rotary gluing machine, and the thickness of the glue can be adjusted by controlling the speed. The speed is 4000 rpm, and the thickness of the glue layer is 2 μm. The substrate coated with the photoresist layer is placed in a vacuum oven for pre-baking, the pre-baking temperature is 90° C., and the baking time is 40 minutes, and then the photoresist plate is obtained. According to the relationship between the design data of the lens mask (writing radius, writing depth) and the laser energy, write and c...
PUM
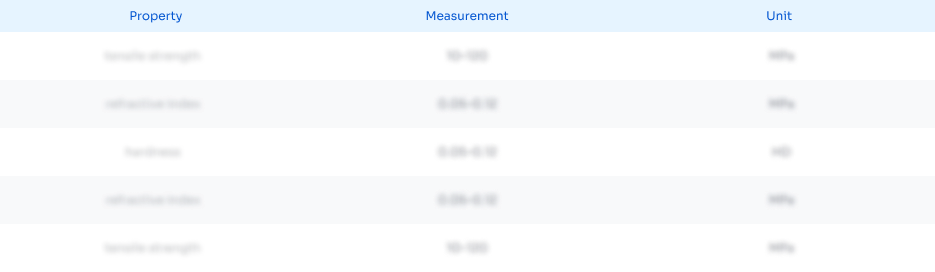
Abstract
Description
Claims
Application Information

- R&D Engineer
- R&D Manager
- IP Professional
- Industry Leading Data Capabilities
- Powerful AI technology
- Patent DNA Extraction
Browse by: Latest US Patents, China's latest patents, Technical Efficacy Thesaurus, Application Domain, Technology Topic, Popular Technical Reports.
© 2024 PatSnap. All rights reserved.Legal|Privacy policy|Modern Slavery Act Transparency Statement|Sitemap|About US| Contact US: help@patsnap.com