Method for preparing high critical current density yttrium barium copper oxide superconducting film
A yttrium barium copper oxide, superconducting thin film technology, applied in the usage of superconducting elements, superconducting devices, superconducting/high conducting conductors and other directions, can solve the problems of reducing the critical current density of thin films, etc. Simple, easy-to-use effects
- Summary
- Abstract
- Description
- Claims
- Application Information
AI Technical Summary
Problems solved by technology
Method used
Image
Examples
specific Embodiment approach
[0036] A specific embodiment of the present invention is: a method for preparing a high critical current density yttrium-barium-copper-oxygen superconducting thin film, and its specific method is:
[0037] a. Preparation of precursor solution: Dissolve yttrium acetate, barium acetate, copper acetate and cobalt acetate in propionic acid according to the stoichiometric ratio of yttrium: barium: copper: cobalt 1:2:2.999:0.001 to obtain a precursor solution. The impurity element in this example is cobalt, and the acetate of the impurity element is cobalt acetate.
[0038] b. Preparation of coating colloid: In the precursor solution of step a, add polymer material polyvinyl butyral (PVB), the mass ratio of the added polymer material to the precursor solution is 4:100, fully stir to obtain the coating layer colloid;
[0039] c. Coating and drying: apply the coating colloid prepared in step b on the substrate, form a thin film on the substrate, and dry at a temperature range of 150°...
Embodiment 2
[0046] The preparation method of this example is as follows:
[0047] A, preparation of precursor solution: yttrium acetate, barium acetate, copper acetate and zinc acetate are dissolved in propionic acid in the ratio of yttrium: barium: copper: zinc stoichiometric ratio 1:2:2.999:0.001, to obtain precursor solution;
[0048] b. Preparation of coating colloid: In the precursor solution of step a, add polymer material polyvinyl butyral (PVB), the mass ratio of the added polymer material to the precursor solution is 4:100, fully stir to obtain the coating layer colloid;
[0049] c. Coating and drying: apply the coating colloid prepared in step b on the substrate, form a thin film on the substrate, and dry at a temperature range of 100°C for 15 minutes;
[0050] d. Thermal decomposition treatment and phase forming heat treatment: the substrate with film obtained in step C is subjected to thermal decomposition treatment and then phase forming heat treatment is carried out. Its s...
Embodiment 3
[0055] The specific approach in this example is:
[0056] A, preparation of precursor solution: yttrium acetate, barium acetate, copper acetate and iron acetate are dissolved in propionic acid in the ratio of yttrium: barium: copper: iron stoichiometric ratio 1:2:2.999:0.001, obtain precursor solution;
[0057] b. Preparation of coating colloid: In the precursor solution of step a, add polymer material polyvinyl butyral (PVB), the mass ratio of the added polymer material to the precursor solution is 4:100, fully stir to obtain the coating colloid;
[0058] c. Coating and drying: apply the coating colloid prepared in step b on the substrate, form a thin film on the substrate, and dry at a temperature range of 160°C for 8 minutes;
[0059] d. Thermal decomposition treatment and phase forming heat treatment: the substrate with film obtained in step C is subjected to thermal decomposition treatment and then phase forming heat treatment is carried out. Its specific operation is a...
PUM
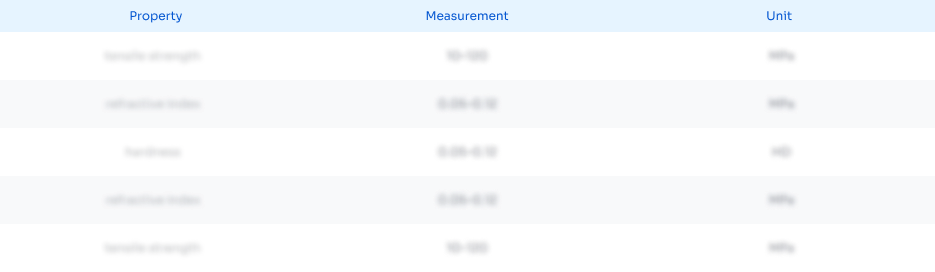
Abstract
Description
Claims
Application Information

- R&D
- Intellectual Property
- Life Sciences
- Materials
- Tech Scout
- Unparalleled Data Quality
- Higher Quality Content
- 60% Fewer Hallucinations
Browse by: Latest US Patents, China's latest patents, Technical Efficacy Thesaurus, Application Domain, Technology Topic, Popular Technical Reports.
© 2025 PatSnap. All rights reserved.Legal|Privacy policy|Modern Slavery Act Transparency Statement|Sitemap|About US| Contact US: help@patsnap.com