Epoxide resin based piezoelectric damping composite material and method for preparing the same
A technology of epoxy resin and composite materials, which is applied in the field of damping composite materials, can solve problems such as complex processes, and achieve the effect of improving damping performance and improving damping performance
- Summary
- Abstract
- Description
- Claims
- Application Information
AI Technical Summary
Problems solved by technology
Method used
Image
Examples
Embodiment 1
[0030] After the PZT powder obtained by sieving is treated with ethanol solution of silane coupling agent, it is filtered and dried, and mixed with bisphenol A diglycidol according to 40% of the total mass of all components of the epoxy resin-based piezoelectric damping composite material. Ether-type epoxy resin (such as CYD-127) is mixed, and then the conductive carbon black surface-treated by the ethanol solution of the silane coupling agent is added according to 0.5% of the mass of CYD-127. Stir mechanically at room temperature for 10 minutes, then place the mixture in an ultrasonic oscillator, vibrate at 90°C and 60Hz for 3 hours, then add polyetheramine T403, stir evenly, and pour it into the mold to 2 / 3 full , wait for it to gel, and then perform a second pour to fill the mold. Curing at room temperature for 3 hours, post-curing at 120°C for 3 hours, cooling in the furnace, demolding and grinding to obtain an epoxy resin-based piezo-resistance damping composite material....
Embodiment 2
[0032] After the PZT powder obtained by sieving is treated with ethanol solution of silane coupling agent, it is filtered and dried, and mixed with bisphenol A diglycidol according to 40% of the total mass of all components of the epoxy resin-based piezoelectric damping composite material. Ether-type epoxy resin (such as CYD-127) is mixed, and then the conductive carbon black surface-treated by the ethanol solution of the silane coupling agent is added according to 0.5% of the mass of CYD-127. Stir mechanically at room temperature for 10 minutes, then place the mixture in an ultrasonic oscillator, vibrate at 90°C and 60Hz for 4 hours, then add polyetheramine T403, stir evenly, and pour it into the mold to 2 / 3 full , wait for it to gel, and then perform a second pour to fill the mold. Curing at room temperature for 4 hours, post-curing at 120°C for 2 hours, cooling in the furnace, demolding and grinding to obtain an epoxy resin-based piezoelectric damping composite material. P...
Embodiment 3
[0034] The PZT powder obtained by sieving is treated with ethanol solution of silane coupling agent and then filtered and dried, mixed with bisphenol A diglycidol according to 75% of the total mass of all components of the epoxy resin-based piezoelectric damping composite material Ether-type epoxy resin (such as CYD-127) is mixed, and then the conductive carbon black surface-treated by the ethanol solution of the silane coupling agent is added according to 0.5% of the mass of CYD-127. Stir mechanically at room temperature for 15 minutes, then place the mixture in an ultrasonic oscillator, vibrate at 90°C and 80Hz for 4 hours, then add polyetheramine T403, stir evenly, and pour it into the mold to 1 / 2 full , wait for it to gel, and then perform a second pour to fill the mold. Curing at room temperature for 4 hours, post-curing at 120°C for 3 hours, cooling in the furnace, demolding and grinding to obtain an epoxy resin-based piezoelectric damping composite material. Put the sa...
PUM
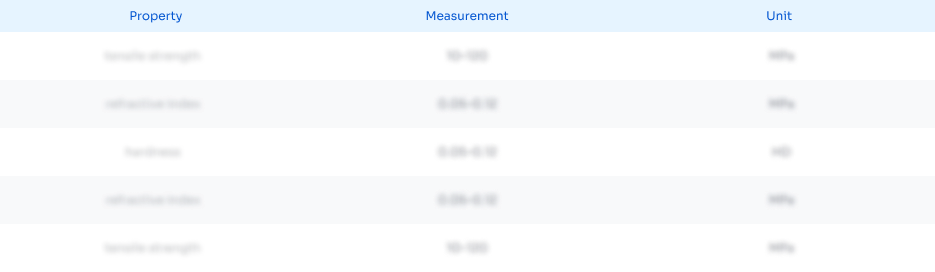
Abstract
Description
Claims
Application Information

- R&D
- Intellectual Property
- Life Sciences
- Materials
- Tech Scout
- Unparalleled Data Quality
- Higher Quality Content
- 60% Fewer Hallucinations
Browse by: Latest US Patents, China's latest patents, Technical Efficacy Thesaurus, Application Domain, Technology Topic, Popular Technical Reports.
© 2025 PatSnap. All rights reserved.Legal|Privacy policy|Modern Slavery Act Transparency Statement|Sitemap|About US| Contact US: help@patsnap.com