Method for inhibiting hydrocarbons steam cracking furnace from coking and carburizing
A technology of cracking furnace and steam, which is applied in cracking, non-catalytic thermal cracking, petroleum industry, etc. It can solve problems such as difficult maintenance, influence on downstream systems, and long time for injecting inhibitors, and achieves simple and easy operation methods and improved transmission Thermal effect, effect of suppressing catalytic coking
- Summary
- Abstract
- Description
- Claims
- Application Information
AI Technical Summary
Problems solved by technology
Method used
Image
Examples
Embodiment 1
[0046] Example 1 and Example 2 are the results of the treatment of the industrial cracking furnace.
[0047] Example 1
[0048] Set the solid content to 20%, SiO 2 / Al 2 O 3 =8, aluminosilicate sol with a pH of 3~4 is diluted with water to SiO with an oxide mass concentration of 1% 2 -Al 2 O 3 Sol aqueous solution. The device is a 60,000-ton / year ethylene SRT-IV (HC) industrial cracking furnace, which is divided into six groups of feeds, and three waste heat boilers are connected in parallel. The furnace tubes in the radiant section of the cracking furnace are arranged along the axial direction at intervals. The twisted piece tube made integrally with the furnace tube, the twisted piece is twisted by 180°, and the distance between two adjacent twisted pieces is 15 pitches; during the hot standby after the cracking furnace is scorched, the outlet temperature of the cracking furnace is 700 ~850℃, under 0.4Mpa operating pressure, the diluted SiO 2 -Al 2 O 3 The sol aqueous solution...
Embodiment 2
[0050] Set the solid content to 20%, SiO 2 / Al 2 O 3 =8, aluminosilicate sol with a pH of 3~4 is diluted with water to SiO with an oxide mass concentration of 2% 2 -Al 2 O 3 Sol aqueous solution. The device is a 30,000-ton / year ethylene GK-V cracking furnace, which is divided into four groups of feeds. There are two waste heat boilers. The radiant section of the cracking furnace is spaced apart in the form of twisted fin tubes. The twisted fins are twisted. 180°, the distance between two adjacent twisted pieces is 20 pitches; during the hot standby after the scorching of the cracking furnace, the outlet temperature of the cracking furnace is 700~850℃. Under the operating pressure of 0.3Mpa, it will dilute Good SiO 2 -Al 2 O 3 The sol aqueous solution is injected from the cross section of the cracking furnace with the carrier gas water vapor (10kg / h), in which SiO 2 / Al 2 O 3 The molar ratio is 8:1, the injection volume is 1.5kg / h, and the injection time is 2 hours. SiO 2 -Al 2 O 3...
Embodiment 3
[0055] To simulate the SRT-III cracking furnace, using the method of the present invention, three twisted sheet tubes are added to the radiant section of the furnace tube. When the outlet temperature of the cracking furnace is 800°C, the SiO 2 A neutral silica sol with a mass concentration of 20% and a pH of 6.5 to 7.5 is diluted with water into pure oxide SiO with a mass concentration of 0.5% 2 The sol aqueous solution is injected from the cross section of the cracking furnace, the injection rate is 200g / h, the injection time is 1 hour, and the SiO 2 The sol forms a ceramic film layer on the inner wall of the cracking furnace tube, which can inhibit the coking and carburization of the furnace tube. After the cracking furnace tube is treated with the above method, steam cracking is carried out with naphtha as the raw material. Its physical properties are: distillation range 48~211℃, specific gravity D 15.6 0.7287g / ml, sulfur content of 165PPM; cracking conditions: cracking tempera...
PUM
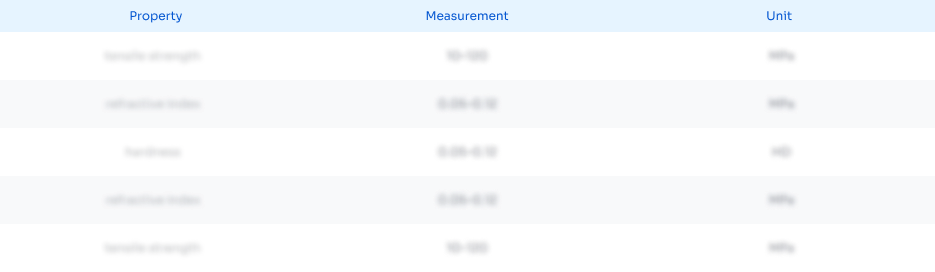
Abstract
Description
Claims
Application Information

- Generate Ideas
- Intellectual Property
- Life Sciences
- Materials
- Tech Scout
- Unparalleled Data Quality
- Higher Quality Content
- 60% Fewer Hallucinations
Browse by: Latest US Patents, China's latest patents, Technical Efficacy Thesaurus, Application Domain, Technology Topic, Popular Technical Reports.
© 2025 PatSnap. All rights reserved.Legal|Privacy policy|Modern Slavery Act Transparency Statement|Sitemap|About US| Contact US: help@patsnap.com