High-boron low-carbon abrasion resistant cast steel and heat treatment method thereof
A heat treatment method and steel casting technology, which is applied in the field of steel materials, can solve problems such as high brittleness, achieve the effects of improving the hardness of cast steel, low production costs, and improving the wear resistance of cast steel
- Summary
- Abstract
- Description
- Claims
- Application Information
AI Technical Summary
Problems solved by technology
Method used
Examples
Embodiment 1
[0033] Using a 500 kg medium frequency induction furnace to melt high boron and low carbon wear-resistant cast steel, the manufacturing process steps are:
[0034] 1) Use scrap steel, ferroboron, ferrosilicon, ferrochromium, and ferromanganese as ingredients, and adjust the carbon content with waste graphite electrodes. After the molten steel is melted and the composition is adjusted before the furnace, the temperature is raised to 1592°C, and 0.24% of the mass of the molten steel is added. Aluminum deoxidation, and then out of the furnace;
[0035] 2) Crushing the cerium-based rare earth, ferro-titanium and ferro-vanadium into small pieces with a particle size of less than 12mm, drying at 180-200°C, placing them at the bottom of the ladle, and compounding and modifying the molten steel by pouring into the ladle;
[0036] 3) pouring molten steel into castings after metamorphic treatment;
[0037] 4) After the casting is austenitized at 900°C×2h, it is directly austempered in ...
Embodiment 2
[0043] Using a 500 kg medium frequency induction furnace to melt high boron and low carbon wear-resistant cast steel, the manufacturing process steps are:
[0044] 1) Use scrap steel, ferroboron, ferrosilicon, ferrochrome, and ferromanganese as ingredients, adjust the carbon content with pig iron, melt the molten steel, adjust the composition before the furnace, raise the temperature to 1598°C, and add aluminum deoxidation accounting for 0.30% of the mass of molten steel , and then released;
[0045] 2) Crushing the cerium-based rare earth, ferro-titanium and ferro-vanadium into small pieces with a particle size of less than 12mm, drying at 180-200°C, placing them at the bottom of the ladle, and compounding and modifying the molten steel by pouring into the ladle;
[0046] 3) pouring molten steel into castings after metamorphic treatment;
[0047] 4) After the casting is austenitized at 920℃×1h, it is directly austempered in an isothermal salt bath furnace at a temperature of...
Embodiment 3
[0053] Using a 750 kg medium frequency induction furnace to melt high boron and low carbon wear-resistant cast steel, the manufacturing process steps are:
[0054] 1) Use scrap steel, ferroboron, ferrosilicon, ferrochrome, and ferromanganese as ingredients, adjust the carbon content with pig iron, melt the molten steel, adjust the composition before the furnace, raise the temperature to 1581°C, and add 0.15% of the mass of the molten steel to deoxidize aluminum , and then released;
[0055] 2) Crushing the cerium-based rare earth, ferro-titanium and ferro-vanadium into small pieces with a particle size of less than 12mm, drying at 180-200°C, placing them at the bottom of the ladle, and compounding and modifying the molten steel by pouring into the ladle;
[0056] 3) pouring molten steel into castings after metamorphic treatment;
[0057] 4) After the casting is austenitized at 880°C for 3h, it is directly austenitized in an isothermal salt bath furnace at a temperature of 300...
PUM
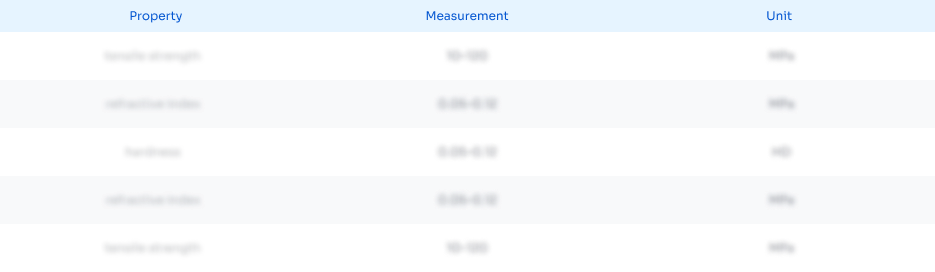
Abstract
Description
Claims
Application Information

- R&D
- Intellectual Property
- Life Sciences
- Materials
- Tech Scout
- Unparalleled Data Quality
- Higher Quality Content
- 60% Fewer Hallucinations
Browse by: Latest US Patents, China's latest patents, Technical Efficacy Thesaurus, Application Domain, Technology Topic, Popular Technical Reports.
© 2025 PatSnap. All rights reserved.Legal|Privacy policy|Modern Slavery Act Transparency Statement|Sitemap|About US| Contact US: help@patsnap.com