Making method for soft magnetic alloy compound material with high magnetic conductivity
A technology of high magnetic permeability and soft magnetic alloy, which is applied in the direction of magnetic properties of inorganic materials, can solve the problems of low resistivity and limitations of metal soft magnetic alloys, and achieve improved magnetic shielding effects, high magnetic permeability, and improved high-frequency magnetic properties. Can effect
- Summary
- Abstract
- Description
- Claims
- Application Information
AI Technical Summary
Problems solved by technology
Method used
Examples
Embodiment 1
[0017] 1) Put the raw materials in the mass ratio: iron 80%, titanium 5%, silicon 9.6%, aluminum 5.4% into an intermediate frequency vacuum induction furnace with alumina as a crucible for melting, and vacuumize to 10 -1 Pa, and then send electricity to preheat the charge to remove the adsorbed gas, moisture and organic matter of the charge. At this time, the vacuum degree in the furnace drops, and then it is evacuated again to 10 -2 Above Pa, fill the furnace with high-purity argon until the pressure in the furnace is 0.5×10 5 Pa, high-power transmission to completely melt the charge, and then low-power refining for 10 minutes before pouring.
[0018] 2) The smelted FeSiAlTi master alloy is put into the rapid quenching equipment, and the alloy ingot is quickly poured on the high-speed rotating roller after arc remelting under the protection of high-purity argon to obtain rapidly condensed flakes. The quenching speed is 15m / s;
[0019] 3) Put the FeSiAlTi flakes into a ball...
Embodiment 2
[0023] 1) The raw materials are melted in an intermediate frequency vacuum induction furnace with alumina as a crucible in a mass ratio of: iron 75%, titanium 10%, silicon 9.6%, aluminum 5.4%, and the vacuum is evacuated to 10 -1 Pa, and then send electricity to preheat the charge to remove the adsorbed gas, moisture and organic matter of the charge. At this time, the vacuum degree in the furnace drops, and then it is evacuated again to 10 -2 Above Pa, fill the furnace with high-purity argon until the pressure in the furnace is 0.5×10 5 Pa, high-power transmission to completely melt the charge, and then low-power refining for 10 minutes before pouring.
[0024] 2) The smelted FeSiAlTi master alloy is put into the rapid quenching equipment, and the alloy ingot is quickly poured on the high-speed rotating roller after arc remelting under the protection of high-purity argon to obtain rapidly condensed flakes. The quenching speed is 27.5m / s;
[0025] 3) Put the FeSiAlTi flakes ...
Embodiment 3
[0029] 1) Put the raw materials in the mass ratio: 70% iron, 15% titanium, 9.6% silicon, and 5.4% aluminum for melting in an intermediate frequency vacuum induction furnace with alumina as the crucible, and vacuumize to 10 -1 Pa, and then send electricity to preheat the charge to remove the adsorbed gas, moisture and organic matter of the charge. At this time, the vacuum degree in the furnace drops, and then it is evacuated again to 10 -2 Above Pa, fill the furnace with high-purity argon until the pressure in the furnace is 0.5×10 5 Pa, high-power transmission to completely melt the charge, and then low-power refining for 10 minutes before pouring.
[0030] 2) The smelted FeSiAlTi master alloy is put into the rapid quenching equipment, and the alloy ingot is quickly poured on the high-speed rotating roller after arc remelting under the protection of high-purity argon to obtain a rapidly condensed thin strip. 20m / s;
[0031] 3) Put the FeSiAlTi flakes into a ball mill for fl...
PUM
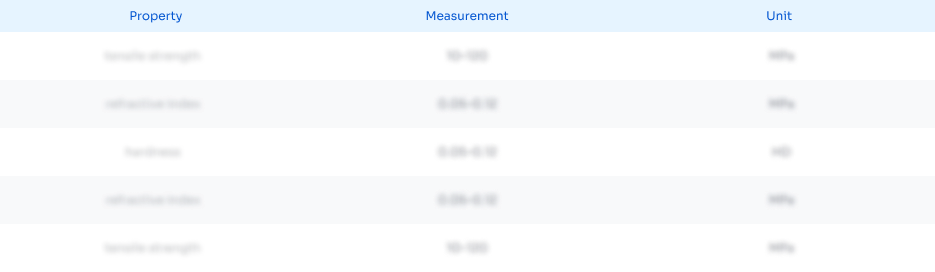
Abstract
Description
Claims
Application Information

- R&D Engineer
- R&D Manager
- IP Professional
- Industry Leading Data Capabilities
- Powerful AI technology
- Patent DNA Extraction
Browse by: Latest US Patents, China's latest patents, Technical Efficacy Thesaurus, Application Domain, Technology Topic, Popular Technical Reports.
© 2024 PatSnap. All rights reserved.Legal|Privacy policy|Modern Slavery Act Transparency Statement|Sitemap|About US| Contact US: help@patsnap.com