Technique for distilling oil from waste carclazyte by extraction method and device thereof
An extraction device and a technology for waste clay, which are used in the recovery of fatty oils/fatty acids from waste, recycling technology, and fat production. The effect of complete separation, unique extraction device and low production cost
- Summary
- Abstract
- Description
- Claims
- Application Information
AI Technical Summary
Problems solved by technology
Method used
Image
Examples
Embodiment 1
[0024] Embodiment 1: This embodiment adopts secondary extraction.
[0025] Fig. 1 has shown the concrete process flow of the present invention. In the figure: closed valve 1, feed screw conveyor 2A, sedimentation net filter extractor 3A, 3B, 3C, plate filter 4, mesh bucket drain conveyor 5, thin mixed oil tank 6-1, thick mixed oil tank 6-2, first evaporator 7, second evaporator 8, stripping tower 9, product oil temporary storage tank 10, primary desolventizer 11-1, secondary desolventizer 11-2, desolventizer condenser 12 -1. First steam condenser 12-2, second steam condenser 12-3, stripping condenser 12-4, free gas condenser 13, tail gas recovery device 14, water separation tank 15, solvent circulation storehouse 16.
[0026] The specific steps of the oil extraction process of waste white clay (powder) directly by solvent extraction are:
[0027] 1. Raw material pretreatment. Carry out preheating treatment to the raw material oil-containing powdery waste clay with a particl...
Embodiment 2
[0035] Embodiment 2: according to the technological process described in embodiment 1, adopt three extractions.
[0036] The oil-containing waste clay (powder) is fed quantitatively, and the drying and tempering machine is used to control the water content to ≤10%, the temperature is 50-55°C, and 5 extraction machines are fed in and out sequentially. The daily processing capacity is about 50T / D. The extraction consists of 6% dilute mixed oil, 2% dilute mixed oil, and fresh solvent soaked three times in sequence. The soaking and sedimentation time is 2h, 0.5h, and 0.5h respectively. The residual solvent of clay after dissolution is ≤700PPM. The dry basis of residual oil in clay after immersion is ≤1%. Mixed oil evaporation, solvent-containing white clay precipitation, and solvent vapor condensation recovery follow the process of Example 1, and the equipment is adjusted in proportion, and its production technical indicators are basically close to Example 1.
PUM
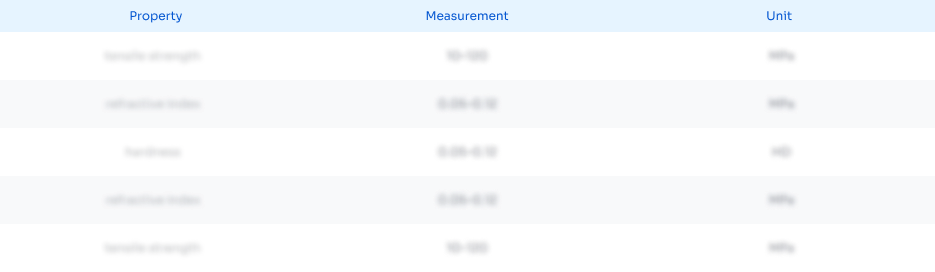
Abstract
Description
Claims
Application Information

- R&D
- Intellectual Property
- Life Sciences
- Materials
- Tech Scout
- Unparalleled Data Quality
- Higher Quality Content
- 60% Fewer Hallucinations
Browse by: Latest US Patents, China's latest patents, Technical Efficacy Thesaurus, Application Domain, Technology Topic, Popular Technical Reports.
© 2025 PatSnap. All rights reserved.Legal|Privacy policy|Modern Slavery Act Transparency Statement|Sitemap|About US| Contact US: help@patsnap.com