Gradient porous ceramics film and method for preparing the same
A gradient porous, ceramic membrane technology, applied in the field of porous ceramics, to achieve the effect of good application prospects
- Summary
- Abstract
- Description
- Claims
- Application Information
AI Technical Summary
Problems solved by technology
Method used
Image
Examples
Embodiment 1
[0017] Put 50g of zirconia ball mill in the ball mill pot, add 27.75g of water, 0.05g of ammonium polyacrylate and 5g of titanium dioxide powder for pre-ball milling, after ball milling for 24 hours, add 15g of polyvinyl alcohol aqueous solution with a concentration of 10wt%, and polyethylene Diol 2.25g, carry out secondary ball milling, the ball milling time is 24h, vacuum pump the ball milled slurry, and then cast on the metal substrate, the scraper height is 0.5mm, put the sample together with the substrate into the low temperature refrigerator Freeze in a freezer for 12 hours, then quickly transfer to a freeze dryer for vacuum drying, and dry at 50°C and 5Pa for 24 hours, and obtain a porous body after sublimation of ice crystals. The freeze-dried green body was placed in a muffle furnace, heated to 600°C at a rate of 2°C / min in an air atmosphere, kept at a temperature of 1h, and plastic ejected, and then kept at a rate of 5°C / min to 1000°C for 1h. Then it was cooled with ...
PUM
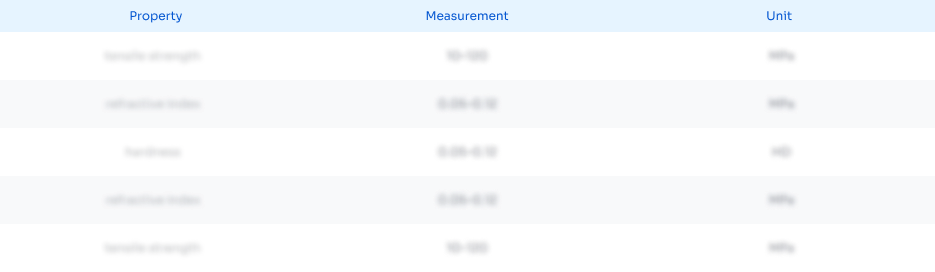
Abstract
Description
Claims
Application Information

- Generate Ideas
- Intellectual Property
- Life Sciences
- Materials
- Tech Scout
- Unparalleled Data Quality
- Higher Quality Content
- 60% Fewer Hallucinations
Browse by: Latest US Patents, China's latest patents, Technical Efficacy Thesaurus, Application Domain, Technology Topic, Popular Technical Reports.
© 2025 PatSnap. All rights reserved.Legal|Privacy policy|Modern Slavery Act Transparency Statement|Sitemap|About US| Contact US: help@patsnap.com