Method for preparing globular high-nitrogen stainless steel powder using with high-energy ball mill
A high-energy ball mill and ball mill technology, applied in the field of alloy powder preparation, can solve the problems of poor powder formability, complex equipment, high cost, etc., and achieve the effect of high sphericity, simple equipment, and low cost
- Summary
- Abstract
- Description
- Claims
- Application Information
AI Technical Summary
Problems solved by technology
Method used
Image
Examples
Embodiment Construction
[0014] Raw materials: Fe powder (-300 mesh) 685 grams, Cr powder (-300 mesh) 170 grams, Mn powder (-300 mesh) 110 grams, Mo powder (-300 mesh) 35 grams.
[0015] Mix the above-mentioned raw material powders together with Φ7mm quenched steel balls and put them into the ball mill tank of the stirring high-energy ball mill. The rotating speed is 400r / min. In order to observe the changing law of the powder during the high-energy ball milling process and prevent the temperature in the spherical tank from being too high, the ball milling process is adopted to stop and cool for 2 hours every 12 hours of ball milling. After a specific time of ball milling, the ball milling tank is opened to take 10-20 grams of powder for nitrogen content detection. And morphology observation, the relationship between the nitrogen content of the powder obtained by ball milling and time is shown in Figure 1, the two are approximately linear, which makes it possible to accurately control the nitrogen con...
PUM
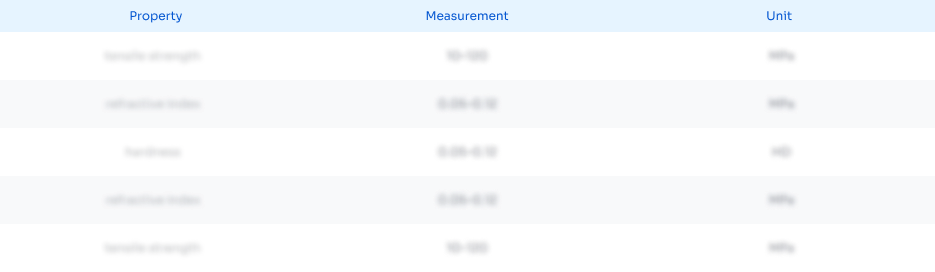
Abstract
Description
Claims
Application Information

- R&D Engineer
- R&D Manager
- IP Professional
- Industry Leading Data Capabilities
- Powerful AI technology
- Patent DNA Extraction
Browse by: Latest US Patents, China's latest patents, Technical Efficacy Thesaurus, Application Domain, Technology Topic, Popular Technical Reports.
© 2024 PatSnap. All rights reserved.Legal|Privacy policy|Modern Slavery Act Transparency Statement|Sitemap|About US| Contact US: help@patsnap.com