Voluminous defect free non-crystal alloy antigravity casting method and special purpose die
An anti-gravity casting and amorphous alloy technology, which is applied in the direction of manufacturing tools, casting equipment, and equipment for feeding molten metal into molds, etc., can solve the problems of poor mechanical properties of amorphous and nanocrystalline alloys and the formation of flow marks. Achieve the effect of ensuring the surface finish of the alloy, avoiding gas flow marks, and ensuring the cooling rate of solidification
- Summary
- Abstract
- Description
- Claims
- Application Information
AI Technical Summary
Problems solved by technology
Method used
Image
Examples
Embodiment 1
[0019] The Zr-Al-Ni-Cu master alloy is configured according to the atomic percentage: Zr 55 -Al 10 -Ni 5 -Cu 30 , melting in a high-frequency induction furnace in a vacuum state, and casting under the protection of an inert gas, the specific steps are:
[0020] 1. Assign Zr according to atomic percentage 55 al 10 Ni 5 Cu 30 The master alloy is coarsely crushed and put into a quartz crucible for casting, the quartz crucible containing the master alloy is placed in a high-frequency induction furnace, and the copper mold for rapid solidification is placed in a vacuum cavity, located in the quartz the lower end of the crucible;
[0021] 2. Pre-adjust the position of the casting nozzle of the quartz crucible and the sprue cup of the copper mold to ensure that the molten alloy completely flows into the copper mold during the casting process;
[0022] 3. Close the furnace door of the vacuum furnace body and evacuate to 5×10 -3 Pa, filled with argon for protection;
[0023] ...
Embodiment 2
[0026] The difference from Example 1 is:
[0027] The alloy smelting and pouring method is the same as in Example 1. The sprue cup of the copper mold and the vertical sprue are socketed with the thermal insulation graphite tube, and the molten alloy is filled to the mold through the thermal insulation graphite tube, ensuring that the alloy in the sprue and the vertical sprue will not be caused by The copper mold is rapidly cooled and solidified, thereby ensuring the integrity of the mold filling.
Embodiment 3
[0029] The alloy smelting and pouring method is the same as in Example 1. The sprue cup and the vertical sprue are graphite external parts connected to the copper mold (as shown in Figure 2). The molten alloy flows against the direction of gravity through the external gating system and fills the copper mold after casting. Rapid solidification forms completely bulk amorphous.
PUM
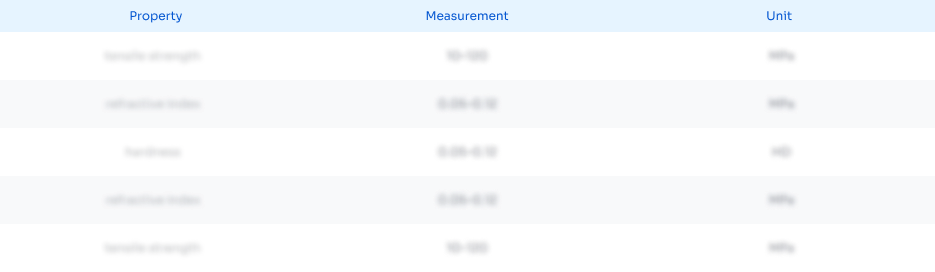
Abstract
Description
Claims
Application Information

- R&D Engineer
- R&D Manager
- IP Professional
- Industry Leading Data Capabilities
- Powerful AI technology
- Patent DNA Extraction
Browse by: Latest US Patents, China's latest patents, Technical Efficacy Thesaurus, Application Domain, Technology Topic, Popular Technical Reports.
© 2024 PatSnap. All rights reserved.Legal|Privacy policy|Modern Slavery Act Transparency Statement|Sitemap|About US| Contact US: help@patsnap.com