Cerium basis composite oxides doped precious metal integer catalyzer and method of manufacturing the same
A technology of composite oxides and monolithic catalysts, applied in metal/metal oxide/metal hydroxide catalysts, physical/chemical process catalysts, chemical instruments and methods, etc., can solve the problems of affecting catalytic activity, complex preparation process, and reducing Catalytic activity and other issues, to achieve the effect of high effective utilization, good catalytic performance and simple preparation process
- Summary
- Abstract
- Description
- Claims
- Application Information
AI Technical Summary
Problems solved by technology
Method used
Examples
Embodiment 1
[0032] (1) Preparation of impregnation solution:
[0033] a. Prepare the precursor solution of noble metal active components, and weigh 1.159g PdCl 2 , add 5.0mL of 1.0mol·L -1 Dissolve dilute hydrochloric acid to form H with a concentration of 6.954g / L 2 PdCl 4 solution;
[0034] b. Weigh 3.729g Ce(NO 3 ) 3 ·6H 2 O(AR), 0.922g Zr(NO 3 ) 4 ·5H 2 O(AR), add 11.0mL of deionized water to dissolve, and make a mixed solution of soluble cerium salt and soluble metal zirconium salt;
[0035]c, add the citric acid (AR) of 3.383g in above-mentioned solution, stir;
[0036] d. Heat the above solution in a water bath at 80°C, add 1.8mL of 95% ethanol dispersant; after the dispersion is complete, add 0.96g of polyethylene glycol (molecular weight M=10000) nonionic surfactant; After the agent is completely dissolved, take 6.954g / L of H 2 PdCl 4 Solution 4.2mL was added to the solution; the whole step was carried out under constant stirring;
[0037] e. Heat the above solution...
Embodiment 2
[0051] (1) Preparation of impregnation solution:
[0052] a, preparation of noble metal active component precursor solution, H 2 PdCl 4 Solution is prepared by the method in embodiment 1, and concentration is 6.954g / L;
[0053] b. Weigh 2.068g Ce(NO 3 ) 3 ·6H 2 O(AR), 3.067g Zr(NO 3 ) 4 ·5H 2 O(AR), add 11.0mL of deionized water to dissolve, and make a mixed solution of soluble cerium salt and soluble metal zirconium salt;
[0054] c, add the citric acid (AR) of 3.752g in above-mentioned solution, stir;
[0055] d. Heat the above solution in a water bath at 80°C, add 1.8mL of 95% ethanol dispersant; after the dispersion is complete, add 0.96g of polyethylene glycol (molecular weight M=10000) nonionic surfactant; After the agent is completely dissolved, take 6.954g / L of H 2 PdCl 4 Solution 4.1mL was added to the solution; the whole step was carried out under constant stirring;
[0056] e. Heat the above solution in a water bath at 80° C. and stir for 5 minutes to ob...
Embodiment 3
[0067] (1) Preparation of impregnation solution:
[0068] a, preparation of noble metal active component precursor solution, H 2 PdCl 4 Solution is prepared by the method in embodiment 1, and concentration is 6.954g / L;
[0069] b. Weigh 3.557g Ce(NO 3 ) 3 ·6H 2 O(AR), 0.879g Zr(NO 3 ) 4 ·5H 2 O(AR), add 11.0mL of deionized water to dissolve, and make a mixed solution of soluble cerium salt and soluble metal zirconium salt;
[0070] c, add the citric acid (AR) of 3.228g in above-mentioned solution, stir;
[0071] d. Heat the above solution in a water bath at 80°C, and add 1.8mL of 95% ethanol dispersant. After dispersing, add 0.96g polyethylene glycol (molecular weight M=10000) non-ionic surfactant; After surfactant dissolves completely, get 6.954g / L H 2 PdCl 4 Solution 4.0mL was added to the solution; the whole step was carried out under constant stirring;
[0072] e. Heat the above solution in a water bath at 80° C. and stir for 5 minutes to obtain an impregnating...
PUM
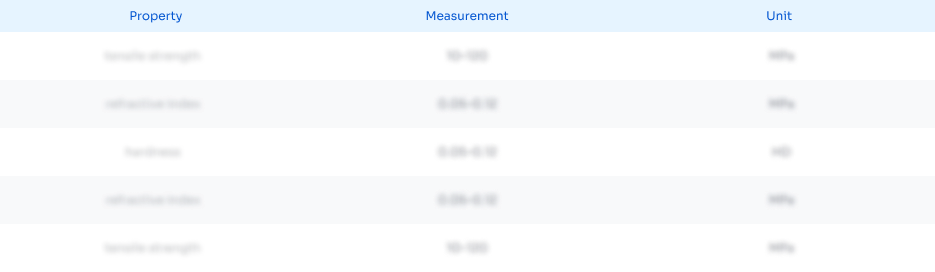
Abstract
Description
Claims
Application Information

- R&D
- Intellectual Property
- Life Sciences
- Materials
- Tech Scout
- Unparalleled Data Quality
- Higher Quality Content
- 60% Fewer Hallucinations
Browse by: Latest US Patents, China's latest patents, Technical Efficacy Thesaurus, Application Domain, Technology Topic, Popular Technical Reports.
© 2025 PatSnap. All rights reserved.Legal|Privacy policy|Modern Slavery Act Transparency Statement|Sitemap|About US| Contact US: help@patsnap.com