Stainless steel surface treatment technique for stainless steel chemical boat
A chemical tanker and surface treatment technology, applied in liquid chemical plating, metal material coating process, coating, etc., can solve problems such as insufficient protection, save valuable time, reduce surface roughness, and improve surface quality Improved effect
- Summary
- Abstract
- Description
- Claims
- Application Information
AI Technical Summary
Problems solved by technology
Method used
Examples
Embodiment 1
[0021] Example 1 Yangyang Company, a subsidiary of CSC Nanjing Yangtze River Tanker Group: 3,000-ton stainless steel chemical tanker "Ninghua 417" (the first ship in China) (operating)
[0022] First of all, segmental polishing is carried out according to the following steps: ①The stainless steel plate is welded and assembled to become segments; ②Add the abrasive brown corundum, and use a 3.0KW flat-panel electric hand-push polishing machine for grinding and polishing. The flat-panel electric hand-push polishing machine is driven by a 3.0KW motor to rotate the shaft. There is a cloth wheel on the shaft. The abrasive brown corundum is adhered to the cloth wheel. When the shaft rotates to drive the cloth wheel to rotate at a high speed, it can grind and polish the stainless steel surface. ; ③The welds are polished and closed after each section is assembled into a ship.
[0023] Then spray pickling passivation: (1) pump the pickling passivation solution into the cabin with the QB...
Embodiment 2
[0026] Example 2 China Changjiang Nanjing Changjiang Tanker Group: four 3,000-ton stainless steel chemical tankers "Ninghua 418" (operating), "Ninghua 419" (operating), "Ninghua 420" (under construction), "Ninghua Chemical 421" (under construction)
[0027] The steps of segmental polishing and spray pickling passivation and the preparation of the corrosion inhibitor are the same as in Example 1, and the formula of the pickling passivation solution used is: 2 Add 2.6 liters of pickling passivation solution to the treatment surface, wherein 2.6 liters of pickling passivation solution is made of 325ml of 98% nitric acid, 182ml of 40% hydrofluoric acid, 18ml of corrosion inhibitor, and 15.6ml of citric acid (food grade) , 0.4ml fatty alcohol polyoxyethylene ether (analytical pure) and 2059ml water.
[0028]Use 500 kg of 8.5% sodium hydroxide aqueous solution to absorb the acid mist in the cabin. The sodium hydroxide solution is an aqueous solution mixed with 42.5 kilograms of so...
Embodiment 3
[0029] Example 3 Sinochem International: 3450-ton stainless steel chemical tanker "Yingchun" (operation), 3600-ton "Dujuan" (operation), 3600-ton "Milan" (operation), 3600-ton "Asparagus" (in operation) establish)
[0030] The steps of segmental polishing and spray pickling passivation and the preparation of the corrosion inhibitor are the same as in Example 1, and the formula of the pickling passivation solution used is: 2 Add 2.7 liters of pickling passivation solution to the treatment surface, wherein 2.7 liters of pickling passivation solution is made of 405ml concentration of 98% nitric acid, 216ml concentration of 40% hydrofluoric acid, 21.6ml corrosion inhibitor, 18.9ml citric acid (food grade ), 0.3ml fatty alcohol polyoxyethylene ether (analytical pure) and 2038.2ml water.
[0031] Use 500 kg of 9% sodium hydroxide aqueous solution to absorb the acid mist in the cabin. The sodium hydroxide solution is an aqueous solution mixed with 45 kilograms of solid sodium hydro...
PUM
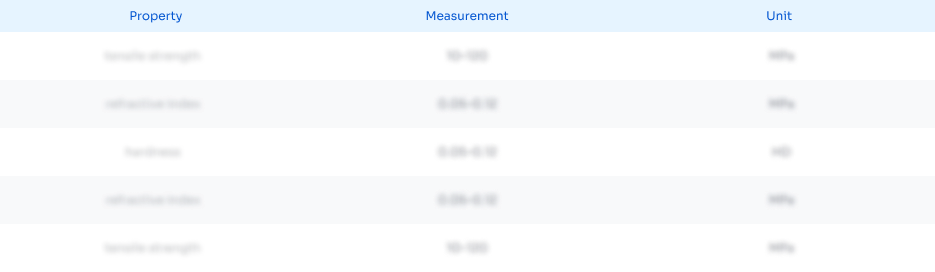
Abstract
Description
Claims
Application Information

- R&D
- Intellectual Property
- Life Sciences
- Materials
- Tech Scout
- Unparalleled Data Quality
- Higher Quality Content
- 60% Fewer Hallucinations
Browse by: Latest US Patents, China's latest patents, Technical Efficacy Thesaurus, Application Domain, Technology Topic, Popular Technical Reports.
© 2025 PatSnap. All rights reserved.Legal|Privacy policy|Modern Slavery Act Transparency Statement|Sitemap|About US| Contact US: help@patsnap.com