Online softening rolling method for medium carbon alloy cold forging steel
A technology of cold heading steel and carbon alloy, which is applied in the direction of metal rolling, metal rolling, rolling mill control devices, etc., which can solve the problems of increasing the chance of decarburization on the surface of steel wire, low section shrinkage, and high production cost, so as to reduce spheroidization Improvement of annealing time, reduction of area, and cost saving of deep processing
- Summary
- Abstract
- Description
- Claims
- Application Information
AI Technical Summary
Problems solved by technology
Method used
Examples
Embodiment 1
[0011] The steel mill refines qualified molten steel and continuously casts it into 140 square billets. The chemical composition is C: 0.35%, Si: 0.18%, Mn: 0.68%, P: 0.015%, S: 0.006%, Cr: 1.0%, Mo: 0.18% ; The steel billet in the wire rod factory is reheated to 1150°C, first rolled by the primary, intermediate and pre-finishing rolling units, and then cooled by controlled water, the rolled piece is finished rolled at 765°C in the finishing rolling unit to form a Φ8mm wire rod, and the deformation reduction rate is 54.5%, deformation rate 1 / 20s, after finishing rolling, the rolled piece is water-cooled to 750°C and exits the laying machine, after spinning, the loose coil is slowly cooled at a cooling rate of 0.2°C / s for 1200 seconds, and the wire is naturally cooled to room temperature and bundled . The chemical composition of the medium carbon alloy cold heading steel is listed in Table 1, the process parameters are listed in Table 2, and the mechanical properties of the mat...
Embodiment 2
[0013] The steel mill refines qualified molten steel and continuously casts it into 140 square billets. The chemical composition is C: 0.34%, Si: 0.20%, Mn: 0.65%, P: 0.011%, S: 0.005%, Cr: 0.9%, Mo: 0.19% ; The steel billet in the wire rod factory is reheated to 1100°C, first rolled by the primary, intermediate and pre-finishing rolling units, and then cooled by controlled water, the rolled piece is finished rolled at 750°C in the finishing rolling unit to form a Φ10mm wire rod, and the deformation reduction rate is 56.6%, deformation rate 1 / 20s, after finishing rolling, the rolled piece is water-cooled to 720°C and exits the laying machine, after spinning, the loose coil is slowly cooled at a cooling rate of 0.25°C / s for 1000 seconds, and the wire is naturally cooled to room temperature and bundled . The chemical composition of the medium carbon alloy cold heading steel is listed in Table 1, the process parameters are listed in Table 2, and the mechanical properties of the m...
Embodiment 3
[0015] The steel mill refines qualified molten steel and continuously casts it into 140 square billets. The chemical composition is C: 0.36%, Si: 0.19%, Mn: 0.63%, P: 0.019%, S: 0.004%, Cr: 1.01%, Mo: 0.19% ; The steel billet in the wire rod factory is reheated to 1180°C, first rolled by the primary, intermediate and pre-finishing rolling units, and then cooled by controlled water, the rolled piece is finished rolled at 800°C in the finishing rolling unit to form a Φ12mm wire rod, and the deformation reduction rate is 58.2%, deformation rate 1 / 20s, after finishing rolling, the rolled piece is water-cooled to 760°C and exits the laying machine, after spinning, the loose coil is slowly cooled at a cooling rate of 0.3°C / s for 900 seconds, and the wire is naturally cooled to room temperature and bundled . The chemical composition of the medium carbon alloy cold heading steel is listed in Table 1, the process parameters are listed in Table 2, and the mechanical properties of the ma...
PUM
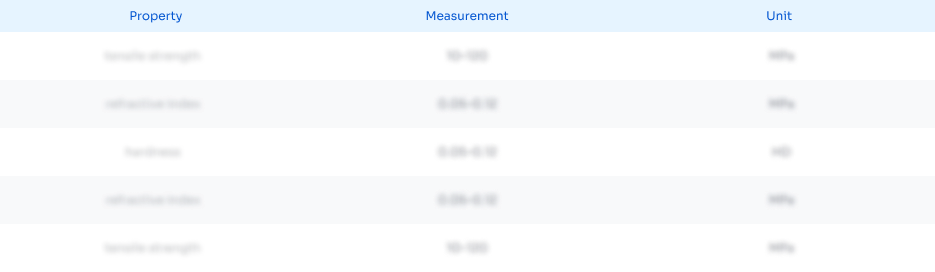
Abstract
Description
Claims
Application Information

- R&D
- Intellectual Property
- Life Sciences
- Materials
- Tech Scout
- Unparalleled Data Quality
- Higher Quality Content
- 60% Fewer Hallucinations
Browse by: Latest US Patents, China's latest patents, Technical Efficacy Thesaurus, Application Domain, Technology Topic, Popular Technical Reports.
© 2025 PatSnap. All rights reserved.Legal|Privacy policy|Modern Slavery Act Transparency Statement|Sitemap|About US| Contact US: help@patsnap.com