Mineral separation process for improving brown iron ore grade
A beneficiation method and limonite technology, applied in chemical instruments and methods, flotation, wet separation, etc., can solve the problems of fine limonite metal particles, large metal loss in the desliming process, and limited classification efficiency, etc. Achieve the effect of improving hydraulic classification efficiency, reducing chemical consumption and improving classification efficiency
- Summary
- Abstract
- Description
- Claims
- Application Information
AI Technical Summary
Problems solved by technology
Method used
Image
Examples
Embodiment 1
[0037] (1) Grinding: Grind the raw ore into a ball mill to -200 mesh, accounting for 98%, and the pulp concentration is 55%, and then overflow through the spiral classifier, enter the -200 mesh high-frequency vibrating screen, and the screened pulp The concentration is adjusted to 25%, and the unscreened ore particles are returned for regrinding;
[0038] (2), re-election: send the above pulp into the spiral chute for roughing, beneficiation and secondary beneficiation;
[0039] a. Rough separation: Desliming of the ore pulp, the concentration of the ore pulp discharged from the concentrate port and the middle ore port is adjusted to 20%, and it enters the selection process, and the ore slime and part of the tailings on the outer edge of the spiral chute are discharged into the tailings pond;
[0040] b. Concentration: Desliming and concentrating the ore pulp, adjusting the width of the concentrate port to 15mm and intercepting the concentrate, adjusting the concentration of t...
Embodiment 2
[0045](1) Grinding: Grind the raw ore into a ball mill to -200 mesh, accounting for 96%, and the concentration of the pulp is 60%. Then, it is classified and overflowed by the spiral classifier, and enters the -200 mesh high-frequency vibrating screen, and the screened pulp The concentration is adjusted to 20%, and the unscreened ore particles are returned for regrinding;
[0046] (2), re-election: send the above pulp into the spiral chute for roughing, beneficiation and secondary beneficiation;
[0047] a. Rough separation: Desliming of the ore pulp, the concentration of the ore pulp discharged from the concentrate port and the middle ore port is adjusted to 20%, and it enters the selection process, and the ore slime and part of the tailings on the outer edge of the spiral chute are discharged into the tailings pond;
[0048] b. Concentration: Desliming and concentrating the ore pulp, adjusting the width of the concentrate port to 25mm and intercepting the concentrate, adjust...
Embodiment 3
[0053] (1) Grinding: Grind the raw ore into the ball mill to -200 mesh, accounting for 99%, the concentration of the pulp is 50%, and then overflow through the spiral classifier, enter the -200 mesh high-frequency vibrating screen, and the pulp after sieving The concentration is adjusted to 20%, and the unscreened ore particles are returned for regrinding;
[0054] (2), re-election: send the above pulp into the spiral chute for roughing, beneficiation and secondary beneficiation;
[0055] a. Rough separation: Desliming of the ore pulp, the concentration of the ore pulp discharged from the concentrate port and the middle ore port is adjusted to 20%, and it enters the selection process, and the ore slime and part of the tailings on the outer edge of the spiral chute are discharged into the tailings pond;
[0056] b. Concentration: Desliming and concentrating the ore pulp, adjusting the width of the concentrate port to 20mm and intercepting the concentrate, adjusting the concentr...
PUM
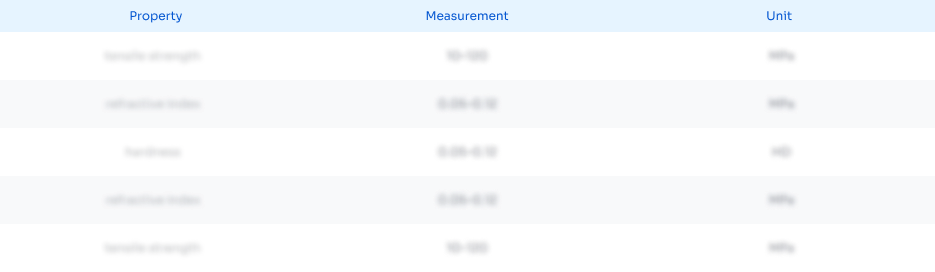
Abstract
Description
Claims
Application Information

- R&D
- Intellectual Property
- Life Sciences
- Materials
- Tech Scout
- Unparalleled Data Quality
- Higher Quality Content
- 60% Fewer Hallucinations
Browse by: Latest US Patents, China's latest patents, Technical Efficacy Thesaurus, Application Domain, Technology Topic, Popular Technical Reports.
© 2025 PatSnap. All rights reserved.Legal|Privacy policy|Modern Slavery Act Transparency Statement|Sitemap|About US| Contact US: help@patsnap.com