Multi-wavelength semiconductor lasers
a semiconductor laser and multi-wavelength technology, applied in the direction of semiconductor laser arrangement, semiconductor laser, laser, etc., can solve the problems of inability to integrate many wavelengths together, device is too long, complex focusing optics, etc., and achieves the effect of high reflectiveness and ease of fabrication and operation
- Summary
- Abstract
- Description
- Claims
- Application Information
AI Technical Summary
Benefits of technology
Problems solved by technology
Method used
Image
Examples
Embodiment Construction
[0019]Referring to FIG. 1a, there is shown a schematic waveguide structure of a dual wavelength laser source monolithically integrated with an isolator and a Y-junction coupler. It contains laser diode sections 1 and 2, an isolator 3 and a Y-junction coupler 4. The structure includes cleaved laser facets 5.
[0020]The Y-junction coupler 4 is used to direct the two signals from the laser diode sections, (i.e. gain regions) 1 and 2 into a single output port. The length of the gain region and isolation region are 700 μm and 300 μm respectively. The Y-junction coupler 4 is composed of two S-bends with a radius of curvature of 1328 μm. The central space between the two branches is 34 μm. The bending loss in the Y-junction waveguide should be kept small in the design. FIG. 1b shows the schematic diagram of a ridge waveguide and vertical layer structure. The ridge waveguide can be formed by either wet chemical etching or Plasma dry etching (ICP or RIB). The wafer is a graded index separate c...
PUM
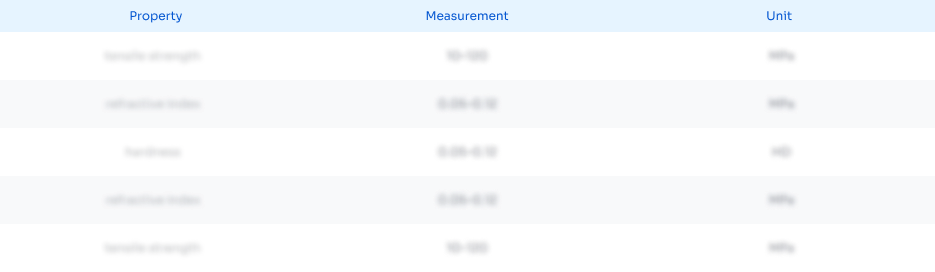
Abstract
Description
Claims
Application Information

- R&D
- Intellectual Property
- Life Sciences
- Materials
- Tech Scout
- Unparalleled Data Quality
- Higher Quality Content
- 60% Fewer Hallucinations
Browse by: Latest US Patents, China's latest patents, Technical Efficacy Thesaurus, Application Domain, Technology Topic, Popular Technical Reports.
© 2025 PatSnap. All rights reserved.Legal|Privacy policy|Modern Slavery Act Transparency Statement|Sitemap|About US| Contact US: help@patsnap.com