Plasma etching method, pattern forming method and cleaning method
a technology of etching method and cleaning method, which is applied in the field of etching method and pattern forming method, and cleaning method, can solve the problems of difficult formation of deep and vertical holes and trenches into the target film to be etched, and the etching properties become wors
- Summary
- Abstract
- Description
- Claims
- Application Information
AI Technical Summary
Benefits of technology
Problems solved by technology
Method used
Image
Examples
experiment 1
[0038]( Gas Species for Zirconium Oxide Film: Single Gas)
[0039]FIG. 2 shows an experimental result of an etching rate (ETCH RATE) and selectivity (SELECTIVITY) when performing the plasma etching on a zirconium oxide film (ZrO), a silicon oxide film (SiO2) and an amorphous carbon film (α-C) when using a plurality of gas species.
[0040]In FIG. 2, and FIGS. 3 through 7 described later, a silicon oxide film of an example of a target film to be etched is expressed as an “Ox,” and an amorphous carbon film of another example of a target film to be etched is expressed as a “CUL.” Also, a “ZrO ER”, an “Ox ER” and a “CUR ER” express etching rates of the zirconium oxide film, the silicon oxide film and the amorphous carbon film, respectively. Moreover, a “ZrO / Ox” expresses selectivity of the zirconium oxide film to the silicon oxide film (which is hereinafter referred to as the selectivity “ZrO / Ox”). A “ZrO / CUL” expresses selectivity of the zirconium oxide film to the amorphous carbon film (whi...
experiment 3
[0049]( Gas Species for Zirconium Oxide Film: Proportion of BCl3, HBr and H2)
[0050]Next, a plasma etching process in which the ratio between hydrogen bromide (HBr) and hydrogen (H2) is varied, while the flow rate of boron trichloride (BCl3) is fixed, was evaluated. FIG. 4 shows the experimental results. In the experiment, the plasma etching process was performed by changing the ratio between hydrogen bromide (HBr) and hydrogen (H2) while setting the flow rate of boron trichloride (BCl3) at “125 sccm.” A proportion of three of the gases is shown in the horizontal axis, and an etching rate is shown in the vertical axis. The ratio of hydrogen (H2) to hydrogen bromide (HBr) increases toward the right side of the graph.
[0051]The results indicated that the selectivity “ZrO / Ox” and the selectivity “ZrO / CUL” basically increased when hydrogen bromide (HBr) was displaced by hydrogen (H2) in this manner. In particular, the selectivity “ZrO / Ox” increased as hydrogen bromide (HBr) was displaced ...
PUM
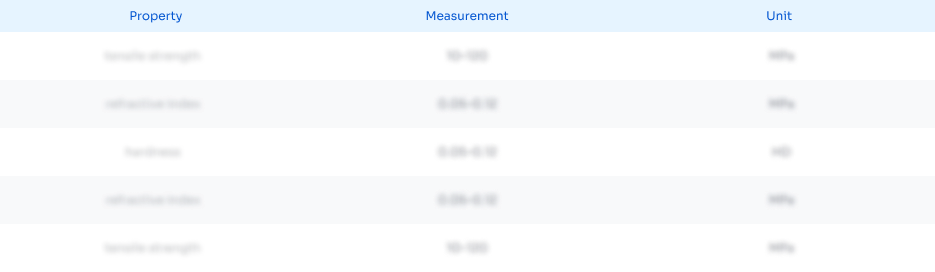
Abstract
Description
Claims
Application Information

- R&D
- Intellectual Property
- Life Sciences
- Materials
- Tech Scout
- Unparalleled Data Quality
- Higher Quality Content
- 60% Fewer Hallucinations
Browse by: Latest US Patents, China's latest patents, Technical Efficacy Thesaurus, Application Domain, Technology Topic, Popular Technical Reports.
© 2025 PatSnap. All rights reserved.Legal|Privacy policy|Modern Slavery Act Transparency Statement|Sitemap|About US| Contact US: help@patsnap.com