Silicon solar cell module using conductive npaste as electrode and method for manufacturing same
a solar cell and silicon substrate technology, applied in the direction of non-conductive materials with dispersed conductive materials, semiconductor devices, pv power plants, etc., can solve the problems of poor electrical/mechanical contact of aluminum rear electrodes with metal ribbons, expensive materials that need to be replaced with inexpensive materials, and high cost of silicon solar cells, so as to reduce power, reduce production costs, and reduce the effect of electric curren
- Summary
- Abstract
- Description
- Claims
- Application Information
AI Technical Summary
Benefits of technology
Problems solved by technology
Method used
Image
Examples
example 1
[0057]The silicon solar cell module according to the present invention was fabricated by the following process.
[0058]To fabricate the silicon solar cell, a p-type single-crystal silicon substrate (165×165 mm; thickness: 180 μm) was used. POCl3 was thermally diffused into the front surface of the silicon substrate to form an n-type layer, thereby forming a p-n junction in the silicon substrate. On the n-type layer, a silicon nitride layer was deposited to form an antireflective layer. To form a front electrode on the antireflective layer of the silicon substrate, a high-temperature silver paste was screen-printed on the antireflective layer to form finger lines having a width of 100 μm. An aluminum paste was applied to the entire rear surface of the silicon substrate. The electrode pastes on the front and rear surfaces were calcined at a temperature of 910° C. During this calcining process, the silver paste of the front electrode penetrated through the antireflective layer so as to b...
PUM
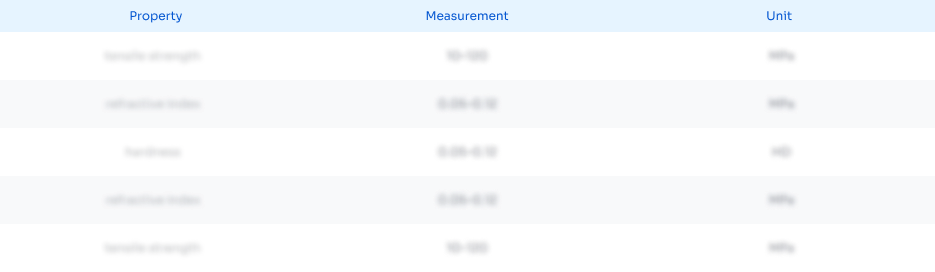
Abstract
Description
Claims
Application Information

- R&D
- Intellectual Property
- Life Sciences
- Materials
- Tech Scout
- Unparalleled Data Quality
- Higher Quality Content
- 60% Fewer Hallucinations
Browse by: Latest US Patents, China's latest patents, Technical Efficacy Thesaurus, Application Domain, Technology Topic, Popular Technical Reports.
© 2025 PatSnap. All rights reserved.Legal|Privacy policy|Modern Slavery Act Transparency Statement|Sitemap|About US| Contact US: help@patsnap.com