Mixing-assisted oxidative desulfurization of diesel fuel using quaternary ammonium salt and portable unit thereof
- Summary
- Abstract
- Description
- Claims
- Application Information
AI Technical Summary
Benefits of technology
Problems solved by technology
Method used
Image
Examples
Embodiment Construction
[0016]Quaternary ammonium salts are compounds comprised of a positively charged nitrogen atom having four substituents, paired with a negatively charged counterion.
[0017]The term “hydroperoxide” is used herein to denote a compound of the molecular structure in which R represents either a hydrogen atom or an organic or inorganic group. Examples of hydroperoxides in which R is an organic group are water-soluble hydroperoxides such as methyl hydroperoxide, ethyl hydroperoxide, isopropyl hydroperoxide, n-butyl hydroperoxide, sec-butyl hydroperoxide, tert-butyl hydroperoxide, 2-methoxy-2-propyl hydroperoxide, tert-amyl hydroperoxide, and cyclohexyl hydroperoxide. Examples of hydroperoxides in which R is an inorganic group are peroxonitrous acid, peroxophosphoric acid, and peroxosulfuric acid. Preferred hydroperoxides are hydrogen peroxide (in which R is a hydrogen atom) and tertiary-alkyl peroxides, notably tert-butyl peroxide.
[0018]The aqueous fluid that is combined with the fossil fuel...
PUM
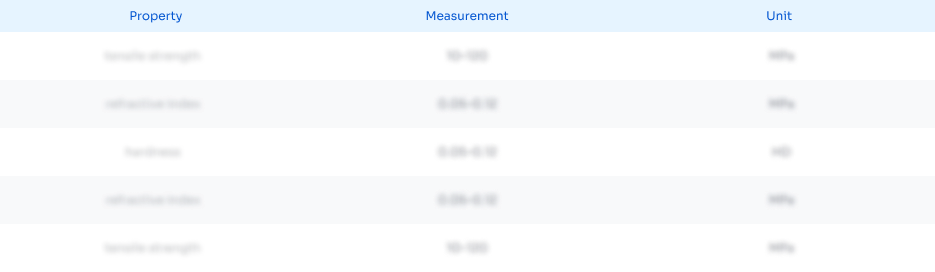
Abstract
Description
Claims
Application Information

- R&D
- Intellectual Property
- Life Sciences
- Materials
- Tech Scout
- Unparalleled Data Quality
- Higher Quality Content
- 60% Fewer Hallucinations
Browse by: Latest US Patents, China's latest patents, Technical Efficacy Thesaurus, Application Domain, Technology Topic, Popular Technical Reports.
© 2025 PatSnap. All rights reserved.Legal|Privacy policy|Modern Slavery Act Transparency Statement|Sitemap|About US| Contact US: help@patsnap.com