Process and apparatus for high energy efficiency chemical looping combustion
a looping combustion and process technology, applied in the direction of combustion types, lighting and heating apparatus, machines/engines, etc., can solve the problems of environmental pollution, potential health effects on plants and animals, and environmental impact to date, and achieve the effect of reducing the number of contaminated water sources
- Summary
- Abstract
- Description
- Claims
- Application Information
AI Technical Summary
Benefits of technology
Problems solved by technology
Method used
Image
Examples
example 1
Molybdenum was used as the metal and reacted with oxygen to form molybdenum trioxide as the oxidized oxygen carrier. Table 1 demonstrates the thermodynamic analyses of the chemical looping combustion process of the invention using molybdenum trioxide with the following combustion reaction: 2MoO3+C=2MoO2+CO2(g)
TABLE 1TΔHΔSΔGCkcalcal / KkcalK100.000−19.27734.432−32.1266.565E+018200.000−19.41234.113−35.5522.649E+016300.000−19.57733.797−38.9487.124E+014400.000−19.80233.437−42.3105.469E+013500.000−20.09533.033−45.6347.956E+012600.000−20.45332.597−48.9161.757E+012700.000−20.87732.139−52.1535.169E+011800.000−21.36031.667−55.3431.870E+011900.000−45.8768.910−56.3293.122E+0101000.000−47.0067.984−57.1726.531E+0091100.000−48.0107.225−57.9311.663E+0091200.000−48.8806.613−58.6224.984E+0081300.000−49.6096.134−59.2581.710E+0081400.000−50.1905.775−59.8526.587E+007I500.000−50.6165.527−60.4172.801E+007
example 2
Vanadium pentoxide was used as the reduced oxygen carrier and reacted with oxygen as follows: V2O5+C═V2O3+CO2(g). Table 2 demonstrates the thermodynamic analyses of the CLC process of the invention using vanadium pentoxide.
TABLE 2TΔHΔSΔGCkcalcal / KkcalK100.000−14.61842.080−30.3205.746E+017200.000−14.57342.187−34.5338.963E+015300.000−14.55342.227−38.7556.011E+014400.000−14.58742.172−42.9768.994E+013500.000−14.71042.005−47.1862.184E+013600.000−14.95741.706−51.3727.237E+012700.000−30.68425.207−55.2152.518E+012800.000−31.25324.651−57.7075.664E+011900.000−31.78624.175−60.1471.607E+0111000.000−32.28423.768−62.5445.461E+0101100.000−32.74423.420−64.9032.142E+0101200.000−33.16523.124−67.2309.435E+0091300.000−33.54322.875−69.5294.573E+0091400.000−33.87422.671−71.8062.400E+0091500.000−34.15622.507−74.0651.348E+009
example 3
Table 3 sets forth the thermodynamic analyses of methane gas using molybdenum trioxide as the reduced oxygen carrier with the following reaction formula: 4MoO3+CH4(g)=4MoO2+CO2(g)+2H2O(g)
TABLE 3TΔHΔSΔGCkJJ / KkJK100.000−176.034279.607−280.3701.780E+039200.000−176.182279.264−308.3161.097E+034300.000−176.765278.165−336.1964.387E+030400.000−178.059276.101−363.9171.743E+028500.000−180.146273.224−391.3892.785E+026600.000−183.023269.734−418.5411.098E+025700.000−186.645265.814−445.3218.035E+023800.000−190.942261.616−471.6959.147E+022900.000−396.47770.843−479.5862.267E+0211000.000−406.41362.709−486.2518.944E+0191100.000−415.36455.936−492.1735.295E+0181200.000−423.26650.377−497.4794.375E+0171300.000−430.04545.920−502.2854.778E+0161400.000−435.63142.474−506.6976.608E+0151500.000−439.94839.964−510.8111.120E+015
PUM
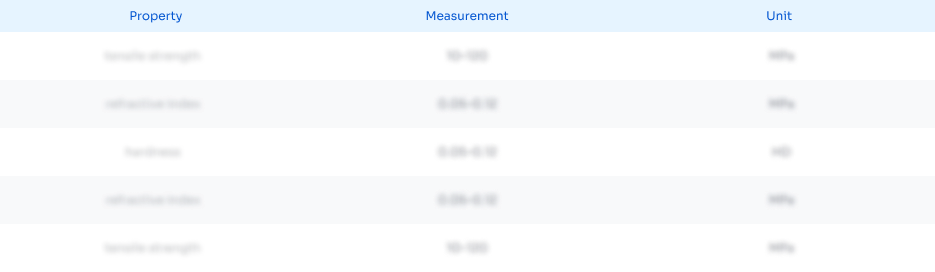
Abstract
Description
Claims
Application Information

- R&D
- Intellectual Property
- Life Sciences
- Materials
- Tech Scout
- Unparalleled Data Quality
- Higher Quality Content
- 60% Fewer Hallucinations
Browse by: Latest US Patents, China's latest patents, Technical Efficacy Thesaurus, Application Domain, Technology Topic, Popular Technical Reports.
© 2025 PatSnap. All rights reserved.Legal|Privacy policy|Modern Slavery Act Transparency Statement|Sitemap|About US| Contact US: help@patsnap.com