Bottom resist layer composition and patterning process using the same
- Summary
- Abstract
- Description
- Claims
- Application Information
AI Technical Summary
Benefits of technology
Problems solved by technology
Method used
Image
Examples
synthetic example 1
[0168] To a 300 mL flask 160 g of m-cresol, 50 g of 1-naphthol, 75 g of 37% formalin solution and 5 g of oxalic acid were added, and the contents were stirred at 100° C. for 24 hours. After the reaction, the contents were dissolved into 500 mL of methyl isobutyl ketone. Then, a catalyst and metallic impurities were removed by sufficient washing with water, and the solvent was removed under a reduced pressure. And the solution was subjected to a condition of at a temperature of 150° C. and at a reduced pressure of 2 mmHg, and water and unreacted monomer were removed to yield 188 g of the following polymer 1.
[0169] Molecular weight (Mw) and distribution (Mw / Mn) of polymer 1 were determined by GPC, and a ratio of repeating units in polymer 1 was determined as follows by 1H-NMR analysis.
[0170] polymer 1; a1:b1 (mole ratio)=0.8:0.2
[0171] Molecular weight (Mw)=12,000
[0172] Molecular-weight distribution (Mw / Mn)=4.60
synthetic example 2
[0173] To a 300 mL flask 160 g of m-cresol, 70 g of 1-hydroxy pyrene, 75 g of 37% formalin solution and 5 g of oxalic acid were added, and the contents were stirred at 100° C. for 24 hours. After the reaction, the contents were dissolved into 500 mL of methyl isobutyl ketone. Then, a catalyst and metallic impurities were removed by sufficient washing with water, and the solvent was removed under a reduced pressure. And the solution was subjected to a condition of at a temperature of 150° C. and at a reduced pressure of 2 mmHg, and water and unreacted monomer were removed to yield 193 g of the following polymer 2.
[0174] Molecular weight (Mw) and molecular-weight distribution (Mw / Mn) of polymer 2 were determined by GPC, and a ratio of repeating units in polymer 2 was determined as follows by 1H-NMR analysis.
[0175] polymer 2; a1:b2 (mole ratio)=0.83:0.17
[0176] Molecular weight (Mw)=12,700
[0177] Molecular-weight distribution (Mw / Mn)=4.80
synthetic example 3
[0178] To a 300 mL flask 160 g of m-cresol, 60 g of 2-hydroxy fluorene, 75 g of 37% formalin solution and 5 g of oxalic acid were added, and the contents were stirred at 100° C. for 24 hours. After the reaction, the contents were dissolved into 500 mL of methyl isobutyl ketone. Then, a catalyst and metallic impurities were removed by sufficient washing with water, and the solvent was removed under a reduced pressure. And the solution was subjected to a condition of at a temperature of 150° C. and at a reduced pressure of 2 mmHg, and water and unreacted monomer were removed to yield 190 g of the following polymer 3.
[0179] Molecular weight (Mw) and a molecular-weight distribution (Mw / Mn) of polymer 3 were determined by GPC, and a ratio of repeating units in polymer 3 was determined as follows by 1H-NMR analysis.
[0180] polymer 3; a1:b3 (mole ratio)=0.75:0.25
[0181] Molecular weight (Mw)=10,800
[0182] Molecular-weight distribution (Mw / Mn)=4.30
PUM
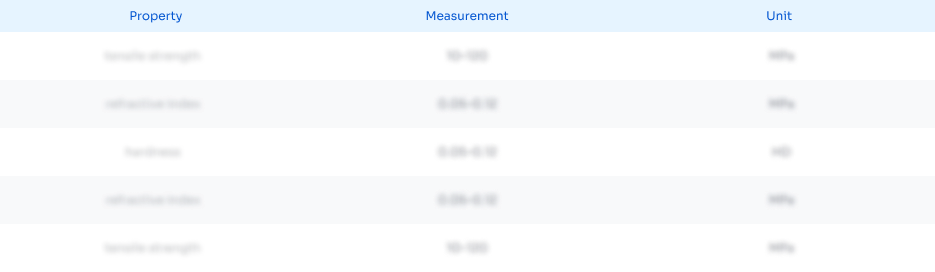
Abstract
Description
Claims
Application Information

- R&D
- Intellectual Property
- Life Sciences
- Materials
- Tech Scout
- Unparalleled Data Quality
- Higher Quality Content
- 60% Fewer Hallucinations
Browse by: Latest US Patents, China's latest patents, Technical Efficacy Thesaurus, Application Domain, Technology Topic, Popular Technical Reports.
© 2025 PatSnap. All rights reserved.Legal|Privacy policy|Modern Slavery Act Transparency Statement|Sitemap|About US| Contact US: help@patsnap.com