Hydrocracking method
A hydrocracking and hydrotreating technology, applied in hydrotreating process, petroleum industry, treating hydrocarbon oil, etc., can solve problems such as difficult to effectively treat, not economical, large hydrogen consumption, etc. The effect of excessive reduction of unit cell constant, increase of latent aromatics content, and increase of yield
- Summary
- Abstract
- Description
- Claims
- Application Information
AI Technical Summary
Problems solved by technology
Method used
Image
Examples
Embodiment 1
[0048] Weigh the raw material NH 4 NaY molecular sieve (80% ammonium exchange degree, 27.1% weight loss on ignition, SiO 2 / Al 2 O 3 The molar ratio is 5.3, the sodium oxide content is 4.0wt%) 2057.6 g, 9 liters of distilled water is added to make a slurry, and the slurry is heated to 95°C under stirring; 495.0 grams of ammonium hexafluorosilicate is added dropwise to the above slurry The solution prepared with 3500 ml of distilled water was dripped in 2 hours, and then continued stirring at 95°C for 2 hours. After stopping the stirring and letting it stand for about 10 minutes, the settled fluorine (silicon) ammonium sodium aluminate crystals were separated by decantation. After washing with water and drying, a Y-type molecular sieve precursor A1 is obtained.
[0049] Weigh the raw material NH 4 NaY molecular sieve (75% ammonium exchange degree, 26% weight loss on ignition, SiO 2 / Al 2 O 3 Molar ratio is 4.5, sodium oxide content is 4.0wt%) 270g, add 1.2 liters of distilled water...
Embodiment 2
[0051] In this embodiment, the hydrocracking catalyst C1 is prepared, and the specific steps are as follows:
[0052] (1) The Y-type molecular sieve precursor A1 is subjected to hydrothermal treatment, wherein the hydrothermal treatment conditions are as follows: the temperature is 600° C., the water pressure is 0.1 MPa, and the treatment time is 1 hour to obtain the Y-type molecular sieve Y1.
[0053] (2) Take 153.5 grams of the Y-type molecular sieve Y1 obtained in step (1), made of 120 grams of small-pore alumina (pore volume 0.47ml / g, specific surface area of 280m 2 / g), 0.2N dilute nitric acid solution, 440ml of the adhesive prepared by peptizing, after extruding and forming, then drying at 110°C for 5 hours and calcining at 600°C for 6 hours to obtain the catalyst carrier.
[0054] (3) Impregnating the catalyst support obtained in step (2) with an aqueous solution containing molybdenum and nickel, drying at 110°C for 5 hours, and calcining at 500°C for 5 hours to prepare t...
Embodiment 3
[0056] In this embodiment, the hydrocracking catalyst C2 is prepared, and the specific steps are as follows:
[0057] (1) Mix, extrude and shape 170g of Y-type molecular sieve precursor A1 and a binder prepared by peptizing 80g of small-pore alumina and dilute nitric acid solution (same as in implementation 2),
[0058] (2) Treat the molded product obtained in step (1) with ammonia gas-steam at high temperature. The treatment conditions are as follows: temperature is 550°C, pressure is 0.1MPa, ammonia partial pressure is 0.01MPa, and the treatment time is 1 hour. Carrier containing Y-type molecular sieve Y2;
[0059] (3) The catalyst carrier obtained in step (2) is impregnated with an aqueous solution containing tungsten and nickel, dried at 110°C for 5 hours, and calcined at 500°C for 5 hours to prepare the hydrocracking catalyst C2 of the present invention.
PUM
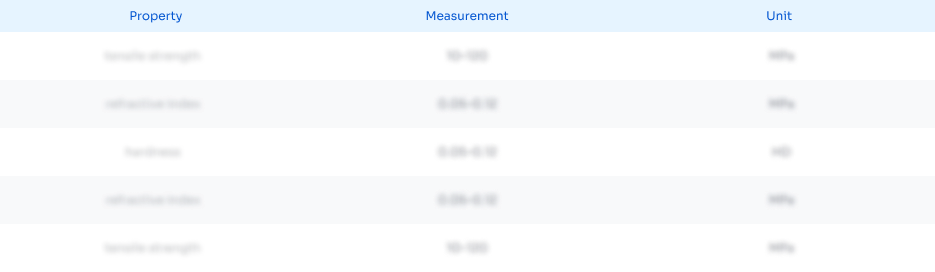
Abstract
Description
Claims
Application Information

- R&D
- Intellectual Property
- Life Sciences
- Materials
- Tech Scout
- Unparalleled Data Quality
- Higher Quality Content
- 60% Fewer Hallucinations
Browse by: Latest US Patents, China's latest patents, Technical Efficacy Thesaurus, Application Domain, Technology Topic, Popular Technical Reports.
© 2025 PatSnap. All rights reserved.Legal|Privacy policy|Modern Slavery Act Transparency Statement|Sitemap|About US| Contact US: help@patsnap.com