High temperature flame-proof protecting method for magnesium and alloy thereof
An alloy, high temperature technology, applied in the field of light metal materials and their metallurgy, which can solve the problems of high flammability, reduced chemical stability, insufficient odor and toxicity
- Summary
- Abstract
- Description
- Claims
- Application Information
AI Technical Summary
Problems solved by technology
Method used
Examples
Embodiment 1
[0060] Embodiment 1: In a box-type resistance heat treatment furnace, a flame retardant protection experiment was carried out during the heat treatment process of magnesium alloy parts. The inner cavity of the heat treatment furnace is 0.2m×0.32m×0.5m, that is, the furnace volume is 32L, and the power is 10KW. A stainless steel tube with an inner diameter of Φ=10mm is inserted into the air inlet behind it, which is used as an introduction pipe for mixed protective gas, and its inlet end is located outside the heat treatment furnace. The magnesium alloy parts used are AZ91D alloy castings, which are placed in a heat treatment furnace. The gas source for flame retardant protection is purchased industrial bottled HFC-125 and CO 2 . HFC-125 and CO 2 The gas sources are respectively sealed and connected to the pressure reducing valve and the flow controller in turn, the outlet of the flow controller is sealed and connected to the inlet of the gas delivery pipe, and the outlet of...
Embodiment 2
[0062]Embodiment 2: In a box-type resistance heat treatment furnace, a flame retardant protection experiment was carried out during the heat treatment process of magnesium alloy parts. The inner cavity of the heat treatment furnace is 0.2m×0.32m×0.5m, that is, the furnace volume is 32L, and the power is 10KW. A stainless steel tube with an inner diameter of Φ=10mm is inserted into the air inlet behind it, which is used as an introduction pipe for mixed protective gas, and its inlet end is located outside the heat treatment furnace. The magnesium alloy parts used are AM60A alloy castings, which are placed in a heat treatment furnace. The gas source for flame retardant protection is purchased industrial bottled HFC-125 and N 2 . HFC-125 and N 2 The gas sources are respectively sealed and connected to the pressure reducing valve and the flow controller in turn, the outlet of the flow controller is sealed and connected to the inlet of the gas delivery pipe, and the outlet of th...
Embodiment 3
[0064] Example 3: An industrial magnesium alloy melting furnace was used to conduct a flame retardant protection experiment of melting, heat preservation and cooling of pure magnesium. The melting furnace used is the HS-350 die-casting magnesium alloy melting and pouring furnace produced by Chongqing Shuolong Technology Co., Ltd. The inner area of the crucible is about 0.32m 3 , which has its own high-temperature-resistant protective gas introduction pipeline, which is used to introduce the mixed protective gas above the crucible in the furnace, and its inlet port is located outside the furnace. The magnesium used is industrial pure magnesium, which is placed in the crucible of the furnace. The gas sources for flame retardant protection are purchased industrial bottled HFC-125 and dry compressed air. The HFC-125 and dry compressed air sources are respectively sealed and connected to the pressure reducing valve and the flow controller in turn. The inlet end of the pipeline ...
PUM
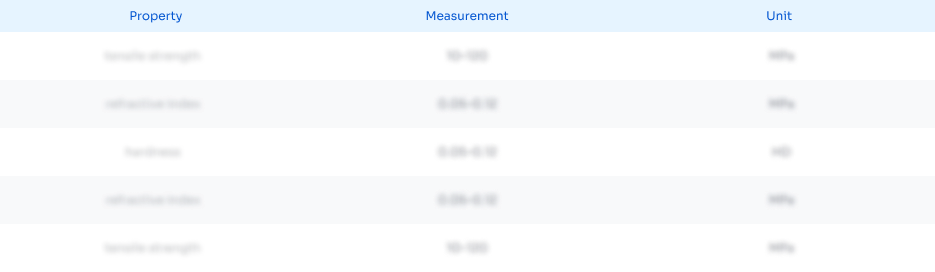
Abstract
Description
Claims
Application Information

- R&D Engineer
- R&D Manager
- IP Professional
- Industry Leading Data Capabilities
- Powerful AI technology
- Patent DNA Extraction
Browse by: Latest US Patents, China's latest patents, Technical Efficacy Thesaurus, Application Domain, Technology Topic, Popular Technical Reports.
© 2024 PatSnap. All rights reserved.Legal|Privacy policy|Modern Slavery Act Transparency Statement|Sitemap|About US| Contact US: help@patsnap.com