Glass ceramic coating produced on metal carrier and its producing method
A technology of metal carrier and glass ceramics, which is applied in the direction of catalyst carrier, chemical instruments and methods, catalyst protection, etc., and can solve the problems of limiting the purification efficiency of catalytic converters
- Summary
- Abstract
- Description
- Claims
- Application Information
AI Technical Summary
Problems solved by technology
Method used
Image
Examples
Embodiment 1
[0081] Potassium nitrate (KNO 3 ) 3 grams; sodium nitrate (NaNO 3 ) 10 grams; Aluminum nitrate nonahydrate (Al(NO 3 ) 3 9H 2 O) 6 grams; calcium nitrate tetrahydrate (Ca(NO 3 ) 2 4H 2 O) 3.5 grams; nickel nitrate hexahydrate (Ni(NO 3 ) 2 6H 2 O) 10 grams; cobalt nitrate hexahydrate (Co(NO 3 ) 2 6H 2 (2) 10 grams; Add 10 milliliters of distilled water and stir respectively, take out the aqueous solution of the above-mentioned salt according to a) described in: 2.3 grams of potassium nitrate, 4 grams of sodium nitrate, 2.1 grams of aluminum nitrate, 2 grams of calcium nitrate, 6 grams of nickel nitrate, 2.4 grams of cobalt nitrate were mixed evenly. Weigh 2 grams of boric acid and add 15 milliliters of water, and mix and stir the two salt solutions (40 minutes at 50° C.).
[0082] Then prepare tetraethyl orthosilicate solution according to the above-mentioned glass solution preparation method b) in the technical scheme, weigh 15 milliliters of tetraethyl orthosilicate...
Embodiment 2
[0087] Potassium nitrate (KNO 3 ) 3 grams, aluminum nitrate nonahydrate (Al(NO 3 ) 3 9H 2 O) 6 grams, calcium nitrate tetrahydrate (Ca(NO 3 ) 2 4H 2 O) 3.5 grams, strontium nitrate (Sr(NO 3 ) 2 ) 3.5 grams, sodium nitrate (NaNO 3 ) 9 grams, add 10 milliliters of distilled water respectively, stir evenly, take out the aqueous solution potassium nitrate 2.3 grams of above-mentioned salt according to a), aluminum nitrate 2.1 grams, calcium nitrate 2 grams, strontium nitrate 1.4 grams, sodium nitrate 4.4 grams mix uniform.
[0088] Weigh 1 gram of boric acid (H 3 BO 3 ), add 10 ml of water, mix and stir the two salt solutions (under the condition of 50° C.), then prepare tetraethyl orthosilicate solution according to the above-mentioned glass solution preparation method b), weigh 20 milliliters of tetraethyl orthosilicate solution, and then Mix 5 ml of ethanol with a concentration of 85%, 2 ml of water and 0.2 ml of nitric acid with a concentration of 65% and stir evenl...
Embodiment 3
[0093] Potassium nitrate (KNO 3 ) 3 grams, nickel nitrate hexahydrate (Ni(NO 3 ) 2 6H 2 O) 10 grams, aluminum nitrate nonahydrate (Al(NO 3 ) 3 9H 2 O) 6 grams, copper nitrate trihydrate (Cu(NO 3 ) 2 3H 2 O) 12 grams, manganese nitrate hexahydrate (Mn(NO 3 ) 2 6H 2 O) 40 grams, calcium nitrate tetrahydrate (Ca(NO 3 ) 2 4H 2 (2) 3.5 grams, add 10 milliliters of distilled water and stir respectively, take out the aqueous solution potassium nitrate 2.3 grams of the above-mentioned salt according to a), 6 grams of nickel nitrate, 2.1 grams of aluminum nitrate, 3.1 grams of copper nitrate, 12 grams of manganese nitrate, nitric acid Calcium 2 grams mix well.
[0094] Weigh 1.3 grams of boric acid (H 3 BO 3 ), add 12 milliliters of water, mix and stir the two salt solutions (at 50° C.), then prepare tetraethyl orthosilicate solution according to the above glass solution preparation method b), weigh 16 milliliters of tetraethyl orthosilicate solution, and then Mix 4 ml...
PUM
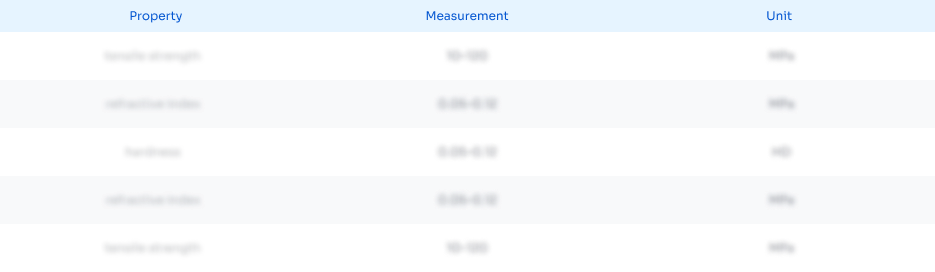
Abstract
Description
Claims
Application Information

- R&D
- Intellectual Property
- Life Sciences
- Materials
- Tech Scout
- Unparalleled Data Quality
- Higher Quality Content
- 60% Fewer Hallucinations
Browse by: Latest US Patents, China's latest patents, Technical Efficacy Thesaurus, Application Domain, Technology Topic, Popular Technical Reports.
© 2025 PatSnap. All rights reserved.Legal|Privacy policy|Modern Slavery Act Transparency Statement|Sitemap|About US| Contact US: help@patsnap.com