Halogen-free reaction extruded expansible flame-proof polythene comprising organic metal complex and its preparation method
A reactive extrusion and organometallic technology, which is applied in the field of halogen-free polyethylene and its preparation, can solve the problems of unsuitability for industrial production, low flame retardant efficiency, and environmental pollution, and achieve easy large-scale industrial production and increase oxygen index resistance. Combustibility, good charcoal effect
- Summary
- Abstract
- Description
- Claims
- Application Information
AI Technical Summary
Problems solved by technology
Method used
Image
Examples
Embodiment 1、8、9、13
[0025] (1) Preparation of reaction extruded flame retardant masterbatch First mix dipentaerythritol and melamine phosphate in a molar ratio of 1:2, and then add 20% of the total weight of the flame retardant masterbatch. Ethylene is mixed as a carrier resin, and the mixture is put into a twin-screw extruder, extruded at a speed of 40 rpm and a temperature of 160-190°C, pelletized, and dried;
[0026] (2) The compounding ratio of reactive extrusion flame retardant masterbatch and ammonium polyphosphate after compounding and mixing, as well as the type and proportion of organometallic complexes mixed in the high-speed mixer and the amount of polyethylene added are shown in Table 1;
[0027] (3) Drying: Dry the uniformly mixed mixture at a temperature of 70°C for 9 hours;
[0028] (4) Melt mixing Put the dried mixture into a twin-screw extruder, and control the temperature in each zone of the extruder to 150°C, 160°C, 170°C, 170°C, 160°C, and 150°C for melt blending Extrusion, ...
Embodiment 2、5~7
[0031] (1) Preparation of reaction extruded flame retardant masterbatch First mix pentaerythritol and melamine phosphate in a molar ratio of 1:1.2, and then add 20% low density polyethylene based on the total weight of the flame retardant masterbatch Mix as a carrier resin, put the mixture into a twin-screw extruder, extrude, pelletize, and dry at a speed of 50 rpm and a temperature of 260-290°C;
[0032] (2) Compounding and mixing The dried reactive extrusion type flame retardant masterbatch and ammonium polyphosphate are compounded in the proportions listed in Table 1 respectively in terms of weight percentage content in expanded flame retardant polyethylene, and compounded with Table 1 The organometallic complexes of the listed varieties and proportions and polyethylene are mixed uniformly in a high-speed mixer;
[0033] (3) Drying: Dry the uniformly mixed mixture at a temperature of 80°C for 8 hours;
[0034] (4) Melt mixing Put the dried mixture into a twin-screw extrude...
Embodiment 3、10、12
[0037] (1) Preparation of reaction extruded flame retardant masterbatch First mix dipentaerythritol and melamine in a molar ratio of 1:1, and then add 20% low density polyethylene based on the total weight of the flame retardant masterbatch as The carrier resin is mixed, and the mixture is put into a twin-screw extruder, extruded at a speed of 10 rpm and a temperature of 270-300°C, pelletized, and dried;
[0038] (2) The compounding ratio of reactive extrusion flame retardant masterbatch and ammonium polyphosphate after compounding and mixing, as well as the type and proportion of organometallic complexes mixed in the high-speed mixer and the amount of polyethylene added are shown in Table 1;
[0039] (3) Vacuum drying Dry the uniformly mixed mixture at a temperature of 90°C for 10 hours;
[0040] The following melt mixing and cooling pelletizing steps are controlled as 50 rev / min except that the screw speed is controlled, all the other are the same as in Example 1, omitted. ...
PUM
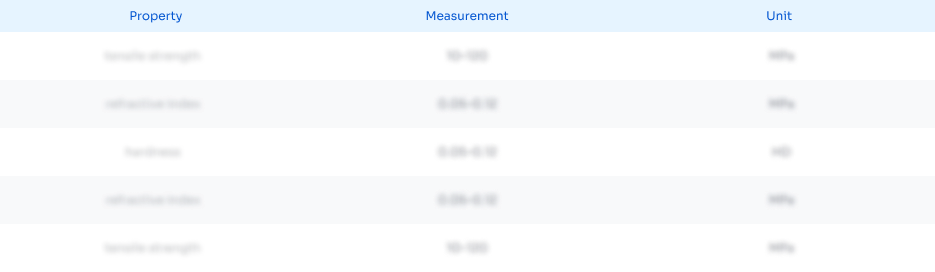
Abstract
Description
Claims
Application Information

- R&D
- Intellectual Property
- Life Sciences
- Materials
- Tech Scout
- Unparalleled Data Quality
- Higher Quality Content
- 60% Fewer Hallucinations
Browse by: Latest US Patents, China's latest patents, Technical Efficacy Thesaurus, Application Domain, Technology Topic, Popular Technical Reports.
© 2025 PatSnap. All rights reserved.Legal|Privacy policy|Modern Slavery Act Transparency Statement|Sitemap|About US| Contact US: help@patsnap.com