Process for preparing diethyl zinc
A diethyl zinc and preparation technology, applied in the direction of zinc organic compounds, etc., can solve the problems of high production cost and high price of diethyl zinc, and achieve the effects of low production cost, reduced production cost, high yield and high purity
- Summary
- Abstract
- Description
- Claims
- Application Information
AI Technical Summary
Problems solved by technology
Method used
Image
Examples
Embodiment 1
[0017] Add 8% of its volume of 40 mesh copper-zinc alloy powder in a sealed stainless steel reactor with a stirrer, and use CO 2 Gas replaces the air in the reactor twice, seals the reactor, and starts the stirrer. The stirring paddle is in the form of an anchor-rake compound. After rising to 80°C, add ethyl iodide and ethyl bromide dropwise at the same time. The mass ratio of ethyl iodide and ethyl bromide is 1:2. After the reaction is triggered, stop adding ethyl iodide and continue to add ethyl bromide dropwise. , the dropping speed is inversely proportional to the reflux speed during the dropping process. The temperature of the reaction process is controlled at 80°C to make the reactant reflux smoothly. After the reflux is completed, close the reflux system of the reactor, control the temperature at 120°C, and continue to stir and react at this temperature After 1 hour, the vacuum system of the reactor was opened, diethyl zinc was recovered by distillation under reduced pr...
Embodiment 2
[0019] Add 12% of the volume of 80 mesh copper-zinc alloy powder in a sealed stainless steel reactor with a stirrer, replace the air in the reactor with nitrogen for 3 times, seal the reactor, start the reactor to stir, stir The form is an anchor-rake compound form. After the temperature inside the reactor is raised to 150°C within 60 minutes, ethyl iodide and ethyl bromide with a mass ratio of 1:1 are added dropwise at the same time, and the dropwise addition is stopped after the reaction is initiated. Ethyl iodide, continue to add ethyl bromide dropwise, the dropping rate during the dropping process is inversely proportional to the reflux rate, and the temperature in the reaction process is controlled at 100°C to make the reactant reflux smoothly. After the reflux is completed, close the reflux system of the reactor, control the temperature at 100°C, continue to stir and react at this temperature for 1.5 hours, open the vacuum system of the reactor, and recover diethyl zinc b...
Embodiment 3
[0021] Add 10% of the volume of 120-mesh copper-zinc alloy powder into a sealed stainless steel reactor with a stirrer, replace the air in the reactor with nitrogen for 3 times, seal the reactor, start the reactor to stir, stir The form is an anchor-rake composite form. After raising the temperature of the reactor to 60°C within 50 minutes, add iodoethane and bromoethane with a mass ratio of 1:1.5. After the reaction is initiated, stop adding iodine Ethane, continue to add bromoethane dropwise. During the dropwise addition, the drop rate is inversely proportional to the reflux rate. The temperature in the reaction process is controlled at 45° C. to make the reactant reflux smoothly. After the reflux is completed, close the reflux system of the reactor, control the temperature at 110°C, continue to stir and react at this temperature for 1.2 hours, open the vacuum system of the reactor, recover diethyl zinc after vacuum distillation, and obtain diethyl zinc with a purity of more ...
PUM
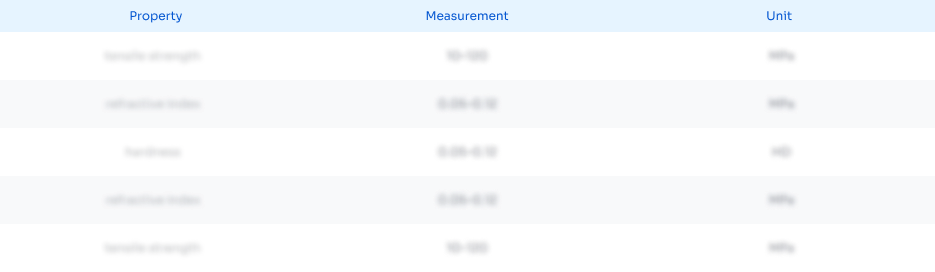
Abstract
Description
Claims
Application Information

- Generate Ideas
- Intellectual Property
- Life Sciences
- Materials
- Tech Scout
- Unparalleled Data Quality
- Higher Quality Content
- 60% Fewer Hallucinations
Browse by: Latest US Patents, China's latest patents, Technical Efficacy Thesaurus, Application Domain, Technology Topic, Popular Technical Reports.
© 2025 PatSnap. All rights reserved.Legal|Privacy policy|Modern Slavery Act Transparency Statement|Sitemap|About US| Contact US: help@patsnap.com